Induction melting furnaces are highly versatile and efficient tools used in metal melting processes, capable of reaching extremely high temperatures. The temperature range of these furnaces is a critical factor for users, as it determines the types of materials that can be melted and the efficiency of the process. Based on the provided references, induction melting furnaces can achieve temperatures up to 2000℃, making them suitable for melting a wide range of metals, including those with high melting points like steel and iron. Additionally, the furnace drain temperature is typically controlled between 100°F (37°C) and 150°F (65°C), with safety mechanisms in place to prevent overheating. This ensures both operational safety and consistency in the melting process.
Key Points Explained:
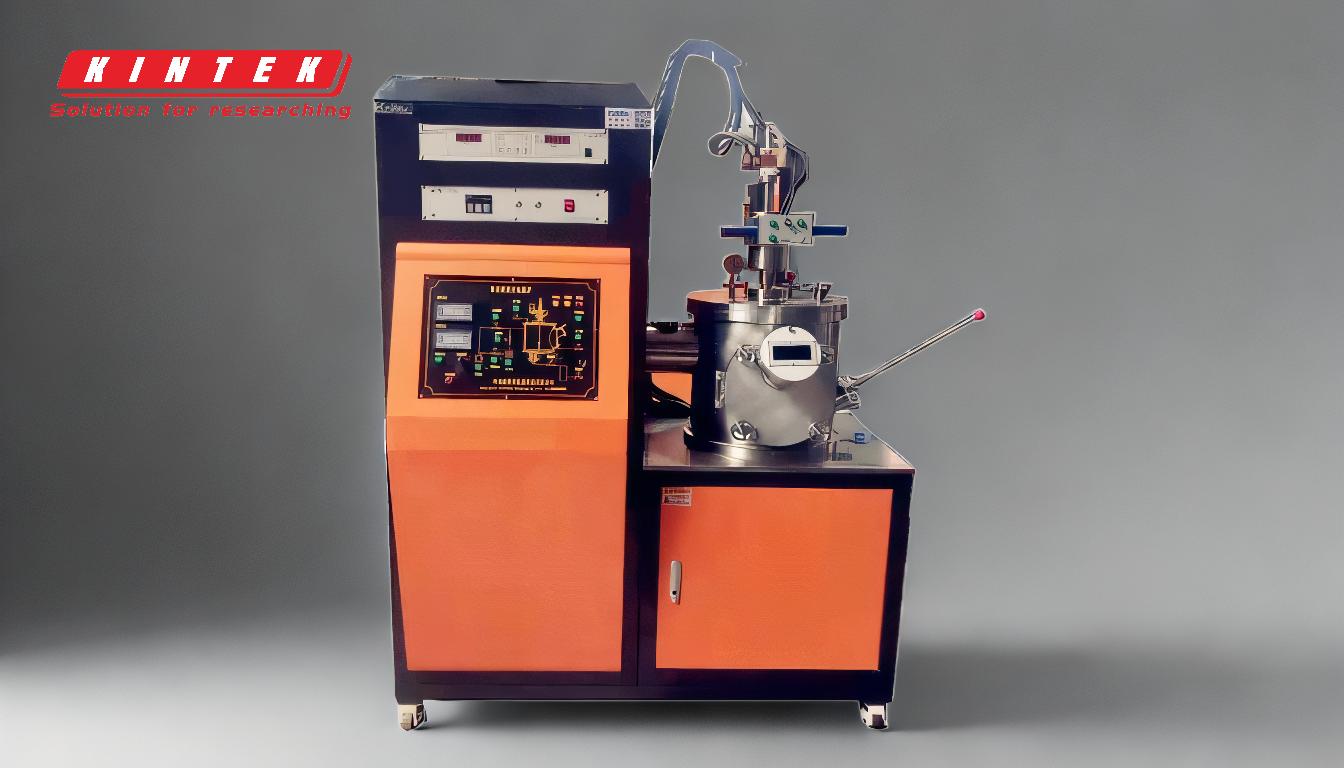
-
Maximum Temperature Capability:
- Induction melting furnaces can reach temperatures as high as 2000℃, as stated in the references. This makes them suitable for melting high-temperature metals such as steel, iron, and other alloys. The high temperature is achieved through efficient inductive coupling between the coil and the charge materials, ensuring rapid and uniform heating.
-
Drain Temperature Control:
- The drain temperature of the furnace is typically maintained between 100°F (37°C) and 150°F (65°C). This range ensures that the molten metal is at an optimal temperature for pouring or further processing. A fixed furnace drain temperature switch is often set at 175°F (79°C), which acts as a safety mechanism. If the temperature exceeds this threshold, the power supply is automatically turned off, preventing overheating and potential damage to the furnace. The switch resets when the temperature cools below 165°F (73°C).
-
Temperature Consistency and Uniformity:
- One of the key advantages of induction melting furnaces is their ability to maintain uniform temperature distribution throughout the molten metal. This is achieved through the medium-frequency magnetic field, which provides magnetic stirring. This stirring action not only ensures uniform temperature but also improves the chemical composition consistency of the metal and aids in the removal of impurities or scum.
-
Operational Flexibility and Safety:
- Induction melting furnaces are designed with advanced features such as IGBT frequency conversion and power regulation, which allow for flexible and smooth operation. These furnaces can operate continuously for 24 hours, making them ideal for industrial applications. Additionally, they are equipped with comprehensive protection functions, including overcurrent, water shortage, overheating, overvoltage, short circuit, and phase loss protection. These features ensure higher reliability, durability, and safety during operation.
-
Energy Efficiency and Environmental Benefits:
- Induction melting furnaces are energy-efficient and environmentally friendly. They offer cleaner operations with less waste production, greater control over emissions, and reduced noise levels. The efficient heat transmission and uniform temperature distribution contribute to reduced oxidation losses and lower operational costs.
-
Design and Portability:
- Modern induction melting furnaces are designed to be compact, lightweight, and portable. They occupy less than one square meter of space, making them suitable for small workshops or facilities with limited space. The furnace bodies are easily replaceable, allowing for flexibility in handling different materials, weights, and starting methods.
-
Smelting Time and Efficiency:
- The smelting time per furnace is typically 20-30 minutes, which is relatively fast compared to traditional melting methods. This efficiency, combined with the ability to operate continuously, makes induction melting furnaces highly productive tools for industrial applications.
In summary, the temperature range of an induction melting furnace is a critical factor that determines its suitability for various metal melting applications. With a maximum temperature capability of 2000℃ and precise control over drain temperatures, these furnaces offer a combination of high performance, safety, and efficiency. Their advanced features, such as IGBT frequency conversion, magnetic stirring, and comprehensive protection mechanisms, make them a reliable choice for industries requiring consistent and high-quality metal melting processes.
Summary Table:
Feature | Details |
---|---|
Maximum Temperature | Up to 2000℃, suitable for melting steel, iron, and high-temperature alloys. |
Drain Temperature Range | 100°F (37°C) to 150°F (65°C) with safety cutoff at 175°F (79°C). |
Uniform Heating | Achieved through magnetic stirring for consistent temperature distribution. |
Operational Safety | Includes overcurrent, overheating, and phase loss protection mechanisms. |
Energy Efficiency | Reduces oxidation losses, emissions, and operational costs. |
Smelting Time | 20-30 minutes per furnace, ideal for continuous industrial use. |
Ready to optimize your metal melting process? Contact us today to find the perfect induction melting furnace for your needs!