Thermal Chemical Vapor Deposition (CVD) is a technique used to deposit thin solid films onto a substrate through thermally induced chemical reactions of gaseous precursors. This method involves exposing the substrate to volatile precursors that react or decompose at high temperatures, forming a solid film on the surface. Thermal CVD is widely used in industries such as semiconductors, electronics, and nanotechnology due to its ability to produce high-quality, uniform films with specific properties. It differs from other CVD methods, such as Plasma-Enhanced CVD (PECVD), as it relies solely on thermal energy rather than plasma excitation. This technique is particularly valuable for applications requiring precise control over film composition, thickness, and structure.
Key Points Explained:
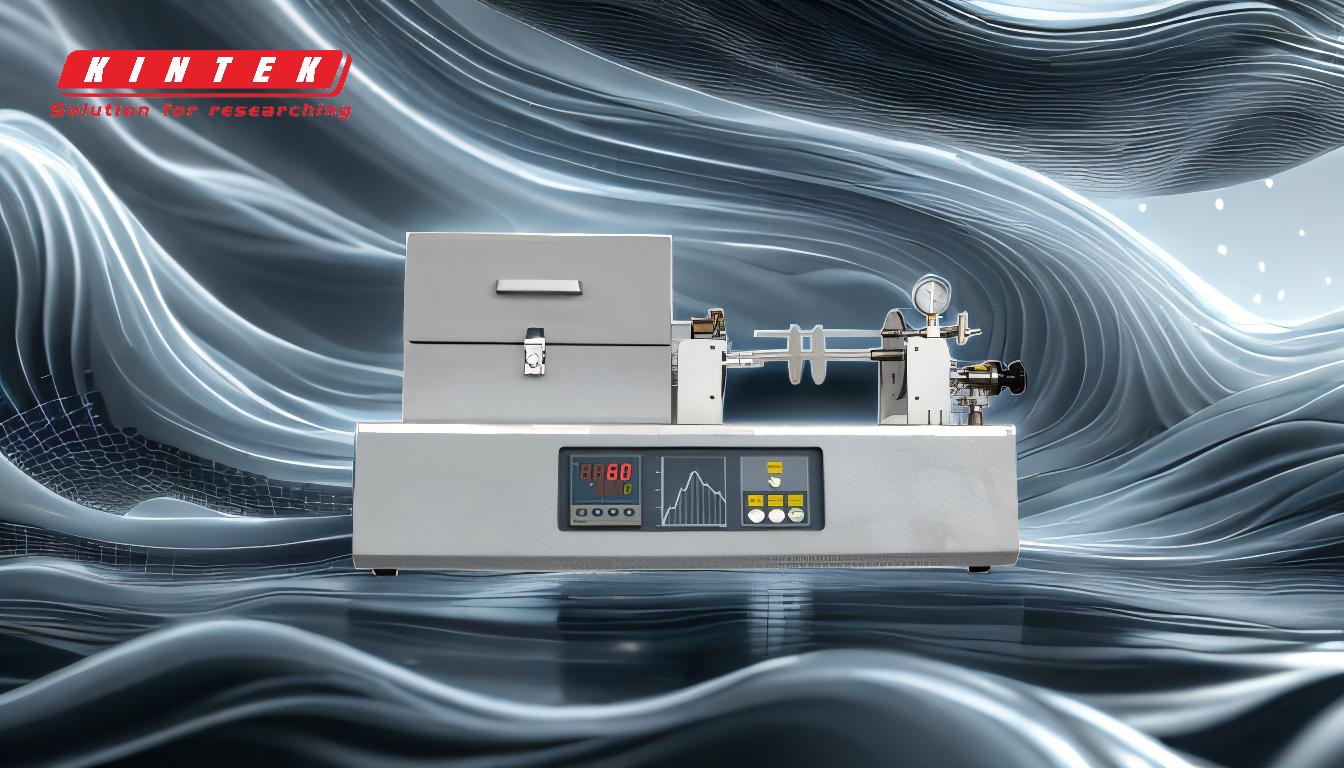
-
Definition of Thermal CVD:
- Thermal CVD is a process where gaseous precursors undergo chemical reactions or decomposition at elevated temperatures to form a solid film on a substrate. The reactions are thermally driven, meaning they rely on heat rather than plasma or other energy sources.
- This method is distinct from physical vapor deposition (PVD) techniques like evaporation or sputtering, as it involves chemical reactions rather than physical processes.
-
Mechanism of Thermal CVD:
- In thermal CVD, the substrate is placed in a reaction chamber and heated to a high temperature. Gaseous precursors are introduced into the chamber, where they adsorb onto the substrate surface.
- The adsorbed precursors undergo chemical reactions or decomposition, resulting in the deposition of a solid film. Byproducts of the reaction are typically gaseous and are removed from the chamber.
-
Applications of Thermal CVD:
- Thermal CVD is extensively used in the semiconductor industry for depositing thin films of materials like silicon, silicon dioxide, and silicon nitride, which are critical for manufacturing integrated circuits.
- It is also employed in the production of graphene, where it enables the growth of high-quality, low-defect graphene sheets for applications in electronics and sensors.
- Additionally, thermal CVD is used in creating nanostructured materials, high-quality polymers, and biomedical devices such as biosensors.
-
Advantages of Thermal CVD:
- High-Quality Films: Thermal CVD produces films with excellent uniformity, purity, and controlled composition.
- Versatility: It can deposit a wide range of materials, including metals, ceramics, and semiconductors.
- Scalability: The process is suitable for large-scale production, making it ideal for industrial applications.
-
Comparison with Other CVD Techniques:
- Unlike Plasma-Enhanced CVD (PECVD), which uses plasma to initiate chemical reactions at lower temperatures, thermal CVD relies solely on heat. This makes thermal CVD more suitable for applications requiring high-temperature processing.
- Thermal CVD typically results in films with fewer defects compared to PECVD, as the absence of plasma reduces the risk of ion-induced damage.
-
Challenges and Considerations:
- Thermal CVD requires precise control over temperature, pressure, and gas flow rates to achieve desired film properties.
- The high temperatures involved can limit the choice of substrates, as some materials may degrade or react at elevated temperatures.
- The process can be energy-intensive, which may increase operational costs.
In summary, thermal CVD is a versatile and widely used technique for depositing high-quality thin films and nanostructured materials. Its reliance on thermal energy makes it particularly suitable for applications requiring precise control over film properties, though it also presents challenges related to energy consumption and substrate compatibility.
Summary Table:
Aspect | Details |
---|---|
Definition | Thermal CVD deposits thin films via thermally induced chemical reactions. |
Mechanism | Gaseous precursors react or decompose at high temperatures on a substrate. |
Applications | Semiconductors, graphene production, nanostructured materials, biosensors. |
Advantages | High-quality films, versatility, scalability. |
Challenges | High energy consumption, substrate compatibility, precise control required. |
Discover how thermal CVD can enhance your material deposition processes—contact us today for expert guidance!