The thermal evaporation process in Physical Vapor Deposition (PVD) is a widely used technique for depositing thin films onto substrates. It involves heating a source material in a high-vacuum environment until it vaporizes, forming a stream of vapor that condenses onto the substrate to create a solid film. This method is known for its simplicity, high deposition rates, and ability to produce pure films with minimal substrate damage. Compared to other PVD techniques like sputtering, thermal evaporation is less complex and does not require reactive gases or complex precursors, making it a cost-effective and efficient choice for many applications.
Key Points Explained:
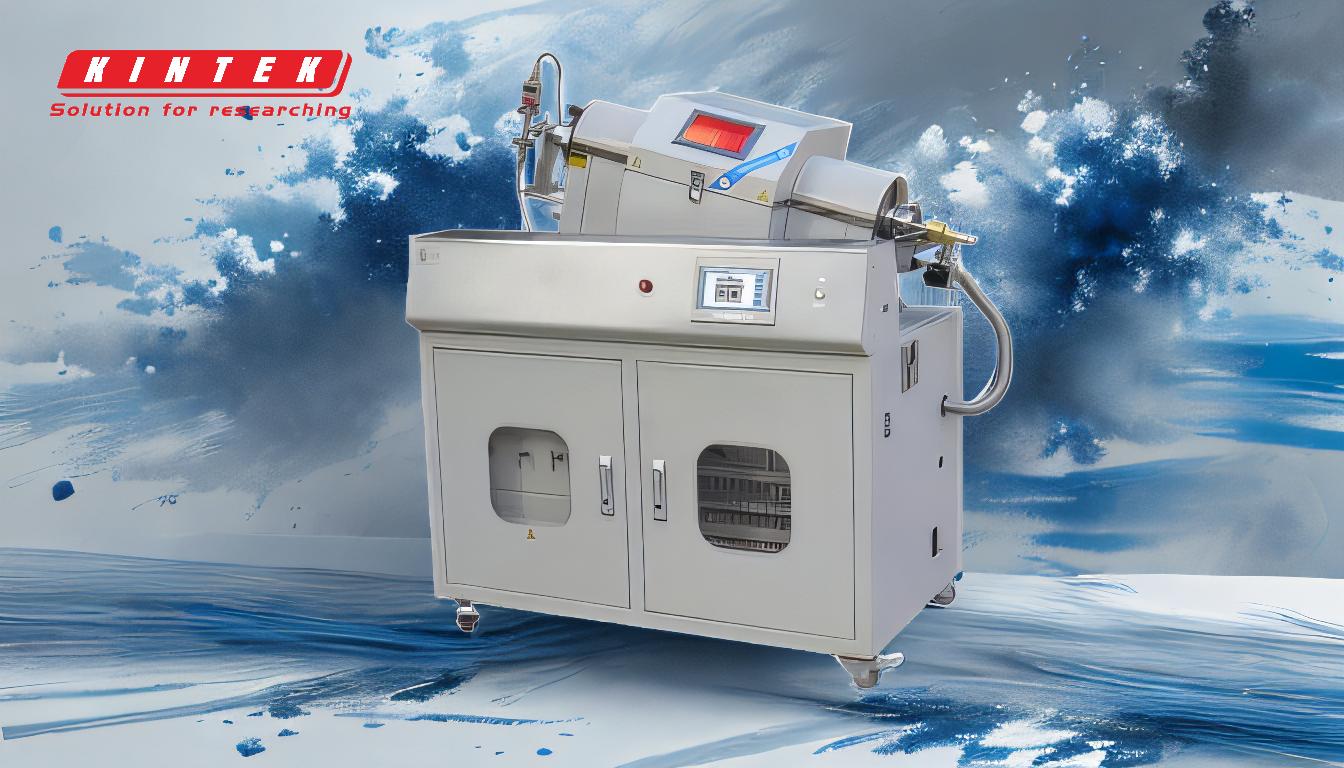
-
Definition of Thermal Evaporation in PVD:
- Thermal evaporation is a PVD technique where a source material is heated to its vaporization point in a high-vacuum environment. The vaporized material then travels through the vacuum and condenses onto a substrate, forming a thin film. This process is one of the oldest and most straightforward methods in the thin film industry.
-
Steps Involved in Thermal Evaporation:
- Creation of a High-Vacuum Environment: A vacuum chamber is essential to minimize contamination and ensure the vaporized material travels unimpeded to the substrate.
- Heating the Source Material: The target material is heated using resistive heating, electron beams, or other methods until it reaches its vaporization temperature.
- Vaporization and Deposition: The vaporized material forms a stream that travels through the vacuum and condenses onto the substrate, forming a solid film.
-
Advantages of Thermal Evaporation:
- High Film Deposition Rates: Thermal evaporation allows for rapid deposition of thin films, making it suitable for high-throughput applications.
- Minimal Substrate Surface Damage: Unlike sputtering, thermal evaporation causes less damage to the substrate surface, preserving its integrity.
- Excellent Film Purity: The high-vacuum environment ensures minimal contamination, resulting in highly pure films.
- Reduced Substrate Heating: The process generates less unintentional heating of the substrate, which is beneficial for heat-sensitive materials.
-
Comparison with Sputtering:
- While both thermal evaporation and sputtering are PVD techniques, they differ in their mechanisms. Sputtering involves bombarding a target material with plasma to knock out atoms, which then deposit onto the substrate. In contrast, thermal evaporation relies on heating the material to create vapor. Thermal evaporation is simpler and less expensive but may not achieve the same level of film density and adhesion as sputtering.
-
Applications of Thermal Evaporation:
- Thermal evaporation is used in various industries, including electronics, optics, and coatings. It is particularly effective for depositing metals, alloys, and some organic materials onto substrates for applications such as solar cells, sensors, and decorative coatings.
-
Limitations of Thermal Evaporation:
- Limited Material Compatibility: Some materials, such as high-melting-point metals and ceramics, are challenging to evaporate using this method.
- Lower Film Density: Films produced by thermal evaporation may have lower density and higher porosity compared to those produced by sputtering.
- Line-of-Sight Deposition: The process is limited to line-of-sight deposition, which can result in uneven coating on complex geometries.
In summary, thermal evaporation is a fundamental PVD technique that offers simplicity, high deposition rates, and excellent film purity. While it has some limitations, it remains a popular choice for many thin film applications due to its cost-effectiveness and efficiency.
Summary Table:
Aspect | Details |
---|---|
Definition | Heating a source material in a high-vacuum environment to create thin films. |
Steps | 1. Create high-vacuum environment. 2. Heat source material. 3. Deposit vapor. |
Advantages | High deposition rates, minimal substrate damage, excellent film purity. |
Applications | Electronics, optics, coatings (e.g., solar cells, sensors, decorative films). |
Limitations | Limited material compatibility, lower film density, line-of-sight deposition. |
Discover how thermal evaporation can enhance your thin film applications—contact our experts today!