Thin film deposition is a process used to apply a thin layer of material onto a substrate, typically within a vacuum chamber. This technique is essential in various industries, including electronics, optics, and coatings, due to its ability to produce high-quality, uniform films with precise thicknesses. The process involves several key steps, including selecting a pure material source, transporting it to the substrate, depositing it to form a thin film, and optionally treating the film to enhance its properties. The choice of deposition method, such as Physical Vapor Deposition (PVD) or Chemical Vapor Deposition (CVD), depends on the desired film characteristics and the specific application. Advanced technologies, such as atomic resolution surface imaging, have further refined these processes, enabling the development of new applications and improving the quality of thin films.
Key Points Explained:
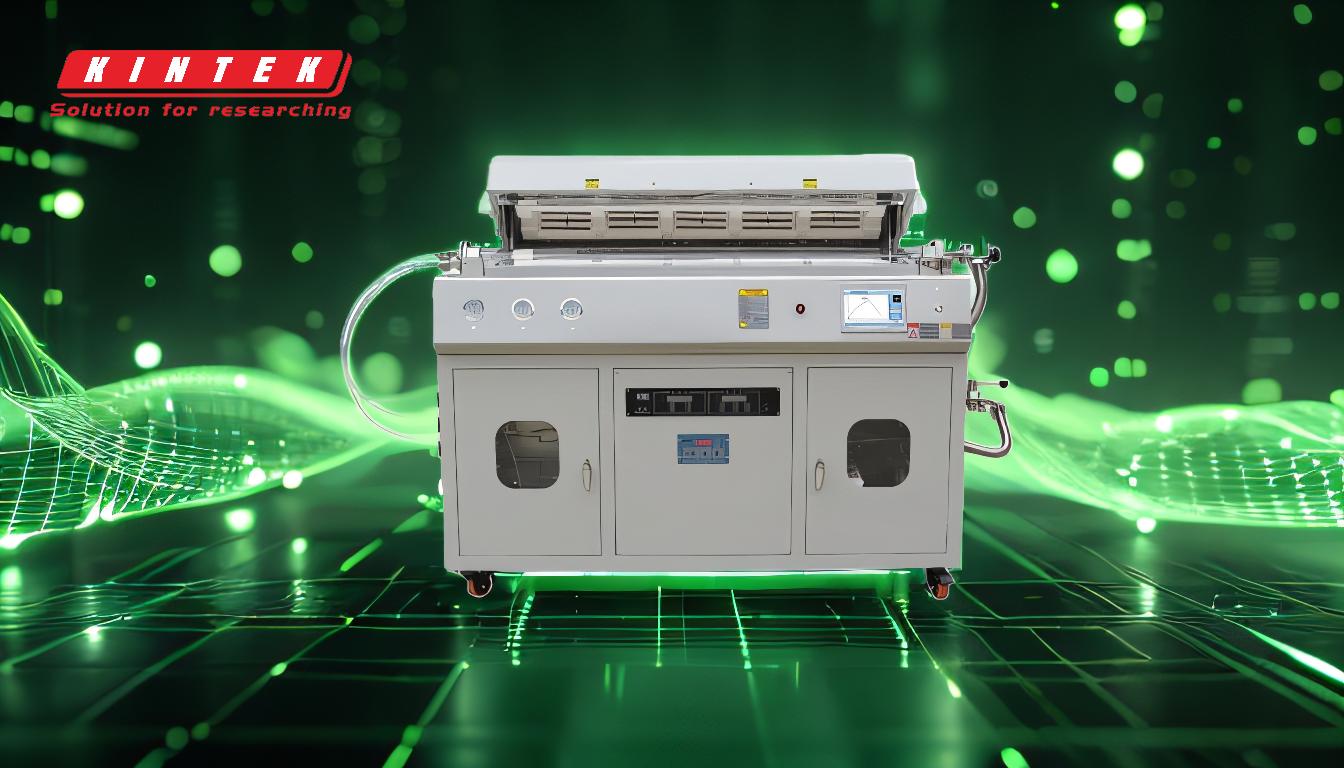
-
Definition and Purpose of Thin Film Deposition:
- Thin film deposition is the process of applying a thin layer of material onto a substrate. This layer can range from a few nanometers to several micrometers in thickness.
- The primary purpose is to create films with specific properties, such as electrical conductivity, optical transparency, or mechanical strength, which are crucial for various applications in electronics, optics, and coatings.
-
Basic Steps in Thin Film Deposition:
- Selection of Material Source: A pure material source (target) is chosen based on the desired properties of the thin film.
- Transportation to Substrate: The target material is transported to the substrate through a medium, which can be a fluid or a vacuum.
- Deposition: The material is deposited onto the substrate to form a thin film. This step can involve various techniques, such as evaporation, sputtering, or chemical reactions.
- Optional Treatment: The film may undergo annealing or heat treatment to enhance its properties.
- Analysis and Modification: The properties of the deposited film are analyzed, and the deposition process may be modified to achieve the desired characteristics.
-
Types of Thin Film Deposition Techniques:
- Physical Vapor Deposition (PVD): Techniques such as evaporation and sputtering are used to deposit thin films. PVD involves the physical transfer of material from a source to the substrate.
- Chemical Vapor Deposition (CVD): This method uses chemical reactions to deposit a thin coating on the substrate. Techniques include chemical bath deposition, electroplating, molecular beam epitaxy, and thermal oxidation.
- Atomic Layer Deposition (ALD): ALD deposits films one atomic layer at a time, allowing for precise control over film thickness and composition.
- Spray Pyrolysis: This technique involves spraying a material solution onto the substrate and thermally degrading it to form a thin film.
-
Materials Used in Thin Film Deposition:
- Metals: Commonly used for their electrical conductivity and reflectivity. Examples include aluminum, copper, and gold.
- Oxides: Used for their optical and electrical properties. Examples include silicon dioxide and titanium dioxide.
- Compounds: These materials offer a combination of properties, such as hardness and thermal stability. Examples include silicon carbide and gallium nitride.
-
Advancements in Thin Film Deposition:
- Atomic Resolution Surface Imaging: This technology has allowed for the precise characterization of thin films, leading to improvements in deposition techniques and film quality.
- Development of New Applications: Advances in deposition methods, such as sputtering-based techniques, have enabled the creation of thin films for new applications, including flexible electronics and advanced coatings.
-
Importance of Deposition Techniques:
- The choice of deposition technique is crucial for achieving the desired properties of the thin film. Each technique has its advantages and limitations, and the selection depends on factors such as the material, substrate, and application requirements.
- High-quality thin films are essential for the performance of various electronic devices, including semiconductors, solar cells, and displays.
In summary, thin film deposition is a critical process in modern technology, enabling the creation of high-quality films with precise properties. The process involves several key steps and can be achieved through various techniques, each with its own advantages and applications. Advances in technology continue to refine these processes, leading to new applications and improved film quality.
Summary Table:
Aspect | Details |
---|---|
Definition | Process of applying a thin layer of material onto a substrate. |
Purpose | Creates films with specific properties like conductivity or transparency. |
Key Steps | Material selection, transportation, deposition, treatment, and analysis. |
Techniques | PVD, CVD, ALD, and spray pyrolysis. |
Materials Used | Metals, oxides, and compounds. |
Advancements | Atomic resolution imaging and new applications like flexible electronics. |
Importance | Crucial for semiconductors, solar cells, and displays. |
Discover how thin film deposition can enhance your projects—contact our experts today!