Electric arc furnaces (EAFs) are widely used in steelmaking due to their energy efficiency, especially when using scrap metal as the primary feedstock. The choice of materials for the EAF process plays a critical role in optimizing energy consumption. Key considerations include the type of scrap metal, the use of oxidants, and the physical and chemical properties of the materials involved. By selecting appropriate materials and optimizing the process, significant energy savings can be achieved.
Key Points Explained:
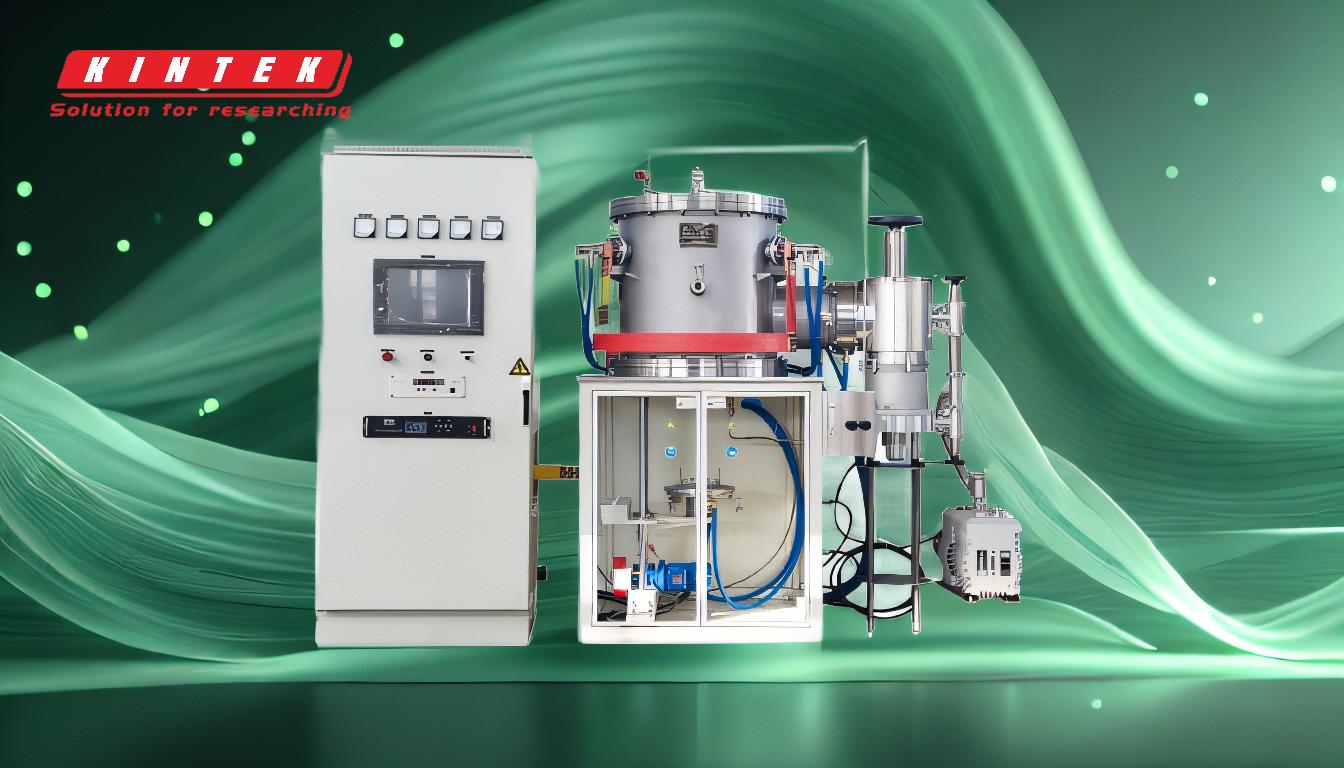
-
Use of Scrap Metal as Feedstock
- Electric arc furnaces are most energy-efficient when using 100% scrap metal as the feedstock.
- Scrap metal requires significantly less energy to melt compared to primary steelmaking from iron ore, as it bypasses the energy-intensive steps of ore reduction and refining.
- The quality and composition of the scrap metal should be carefully selected to ensure consistent melting and minimize impurities, which can increase energy consumption.
-
Material Properties for Energy Efficiency
- The physical properties of the materials, such as melting point and thermal conductivity, directly impact energy consumption.
- Metals with lower melting points (e.g., aluminum or copper) require less energy to melt compared to those with higher melting points (e.g., steel or titanium).
- The chemical composition of the scrap metal should be optimized to reduce the need for additional chemical treatments, which can increase energy usage.
-
Role of Oxidants in the Process
- Oxidants are often used to accelerate the melting process by promoting exothermic reactions, which release heat and reduce the energy required from the electric arc.
- Common oxidants include oxygen and iron oxide, which react with impurities in the scrap metal to form slag.
- The judicious use of oxidants can enhance energy efficiency, but excessive use can lead to unnecessary energy losses and increased wear on furnace components.
-
Importance of Preheating Scrap Metal
- Preheating scrap metal before charging it into the furnace can significantly reduce energy consumption.
- Waste heat from the furnace exhaust gases can be used to preheat the scrap, improving overall energy efficiency.
- Proper insulation and heat recovery systems should be implemented to maximize the benefits of preheating.
-
Optimization of Furnace Lining Materials
- The refractory lining of the electric arc furnace must be made from materials that can withstand high temperatures and chemical reactions without degrading.
- High-quality refractory materials, such as magnesia-carbon bricks, improve thermal efficiency and reduce heat loss.
- Regular maintenance and replacement of the lining are essential to maintain energy efficiency.
-
Use of Additives and Alloys
- Additives such as fluxes and alloys can improve the melting process and reduce energy consumption by lowering the melting point of the scrap metal.
- Fluxes help remove impurities and form slag, while alloys can enhance the properties of the final product.
- The selection of additives should be based on the specific requirements of the steel being produced.
-
Advanced Process Control and Automation
- Implementing advanced process control systems can optimize energy usage by precisely controlling the electric arc, temperature, and chemical reactions.
- Automation reduces human error and ensures consistent operation, leading to improved energy efficiency.
- Real-time monitoring and data analysis can identify areas for further energy savings.
By focusing on these key points, the electric arc furnace process can be optimized for energy efficiency, reducing both operational costs and environmental impact. The careful selection of materials, combined with advanced technologies and process controls, ensures that the EAF remains a sustainable and cost-effective method for steel production.
Summary Table:
Key Factor | Impact on Energy Efficiency |
---|---|
Scrap Metal as Feedstock | 100% scrap metal reduces energy by bypassing ore reduction and refining steps. |
Material Properties | Lower melting points and optimized chemical composition minimize energy consumption. |
Use of Oxidants | Promotes exothermic reactions, reducing energy needed from the electric arc. |
Preheating Scrap Metal | Waste heat preheating reduces energy consumption and improves efficiency. |
Furnace Lining Materials | High-quality refractory materials reduce heat loss and improve thermal efficiency. |
Additives and Alloys | Lower melting points and remove impurities, reducing energy usage. |
Advanced Process Control | Automation and real-time monitoring optimize energy usage and reduce human error. |
Ready to optimize your electric arc furnace for energy efficiency? Contact our experts today for tailored solutions!