Silicon carbide (SiC) is a versatile ceramic material widely used in industrial applications due to its exceptional hardness, thermal conductivity, and chemical resistance. It is primarily classified into two types: black silicon carbide and green silicon carbide, both predominantly consisting of α-SiC. Black silicon carbide contains approximately 95% SiC, while green silicon carbide has a higher purity of around 97% or more. Additionally, silicon carbide ceramics are produced using different sintering methods, including reaction sintering, atmospheric pressure sintering, and recrystallization sintering, each offering unique microstructures and properties suited for specific applications. In industries such as metallurgy, silicon carbide is utilized in the form of lining blocks, bricks, and crucibles for high-temperature furnaces, making it an indispensable material.
Key Points Explained:
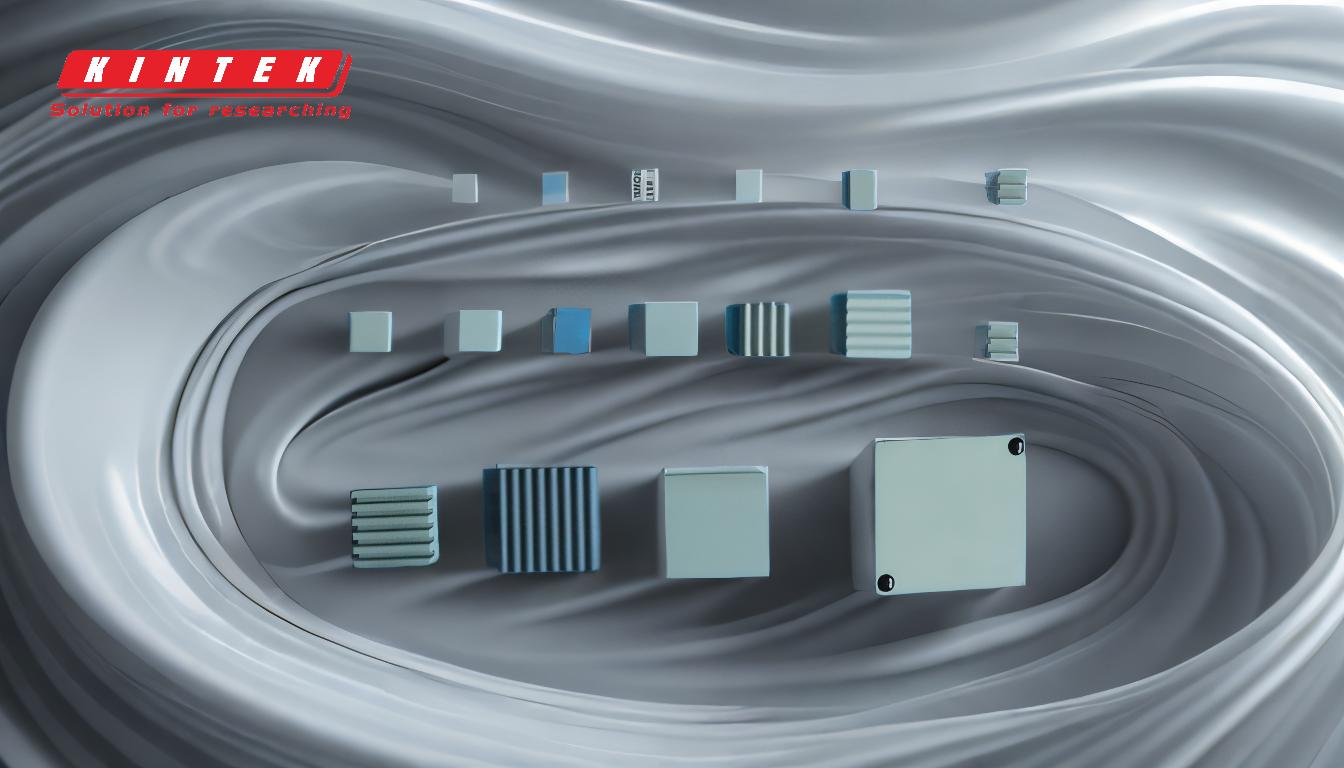
-
Types of Silicon Carbide:
- Black Silicon Carbide: Contains about 95% SiC and is commonly used for grinding and cutting applications due to its hardness and durability.
- Green Silicon Carbide: Contains about 97% or more SiC, offering higher purity and better performance in precision grinding and polishing applications.
-
Sintering Methods:
- Reaction Sintering: This method involves a chemical reaction between silicon and carbon to form silicon carbide. It is cost-effective and produces materials with good mechanical properties.
- Atmospheric Pressure Sintering: This process occurs under normal atmospheric conditions and results in high-density silicon carbide ceramics with excellent thermal and mechanical properties.
- Recrystallization Sintering: This method involves heating silicon carbide to high temperatures without applying pressure, leading to the growth of silicon carbide crystals and improved thermal shock resistance.
-
Industrial Applications:
- Metallurgical Industry: Silicon carbide is used as lining blocks and bricks for various types of furnaces, including blast furnaces, muffle furnaces, walk-through, rotary, and shaft furnaces. It is also used as guide rails in blast furnaces and continuous furnaces due to its high thermal conductivity and resistance to thermal shock.
- Silicon Carbide Crucibles: These are essential for high-temperature applications, such as melting metals and alloys, due to their excellent thermal and chemical stability.
-
Microstructure and Properties:
- The microstructure of silicon carbide varies depending on the sintering method used. Reaction-sintered silicon carbide typically has a fine-grained structure, while recrystallized silicon carbide has larger grains, which enhance its thermal shock resistance.
- The properties of silicon carbide, such as hardness, thermal conductivity, and chemical resistance, make it suitable for a wide range of applications, from abrasive tools to high-temperature furnace components.
-
Advantages of Silicon Carbide:
- High Hardness: Silicon carbide is one of the hardest materials available, making it ideal for abrasive applications.
- Thermal Conductivity: Its high thermal conductivity allows for efficient heat dissipation, which is crucial in high-temperature environments.
- Chemical Resistance: Silicon carbide is resistant to most chemicals, making it suitable for use in corrosive environments.
In summary, silicon carbide is a critical material in various industrial applications, with its types and sintering methods tailored to meet specific performance requirements. Its use in silicon carbide crucibles and furnace linings highlights its importance in high-temperature processes, ensuring durability and efficiency in demanding environments.
Summary Table:
Type | SiC Content | Applications |
---|---|---|
Black Silicon Carbide | ~95% SiC | Grinding, cutting, abrasive tools |
Green Silicon Carbide | ≥97% SiC | Precision grinding, polishing, high-purity applications |
Sintering Methods | Microstructure | Properties |
Reaction Sintering | Fine-grained | Cost-effective, good mechanical properties |
Atmospheric Pressure | High-density | Excellent thermal and mechanical properties |
Recrystallization | Large grains | Improved thermal shock resistance |
Discover the right silicon carbide solution for your industrial needs—contact our experts today!