Chamber furnaces are versatile and essential tools in both laboratory and industrial settings, designed to handle a wide range of high-temperature processes. They are used for applications such as heat treatment, annealing, sintering, curing, and material analysis. These furnaces provide precise temperature control and uniform heating, making them ideal for processes like ashing, calcination, crystal growth, and thermogravimetric analysis. Additionally, they are employed in specialized tasks such as carbon nanotube production, polymer curing, and stress relief. Chamber furnaces are indispensable in industries like manufacturing, materials science, and research, where controlled high-temperature environments are required for material processing and analysis.
Key Points Explained:
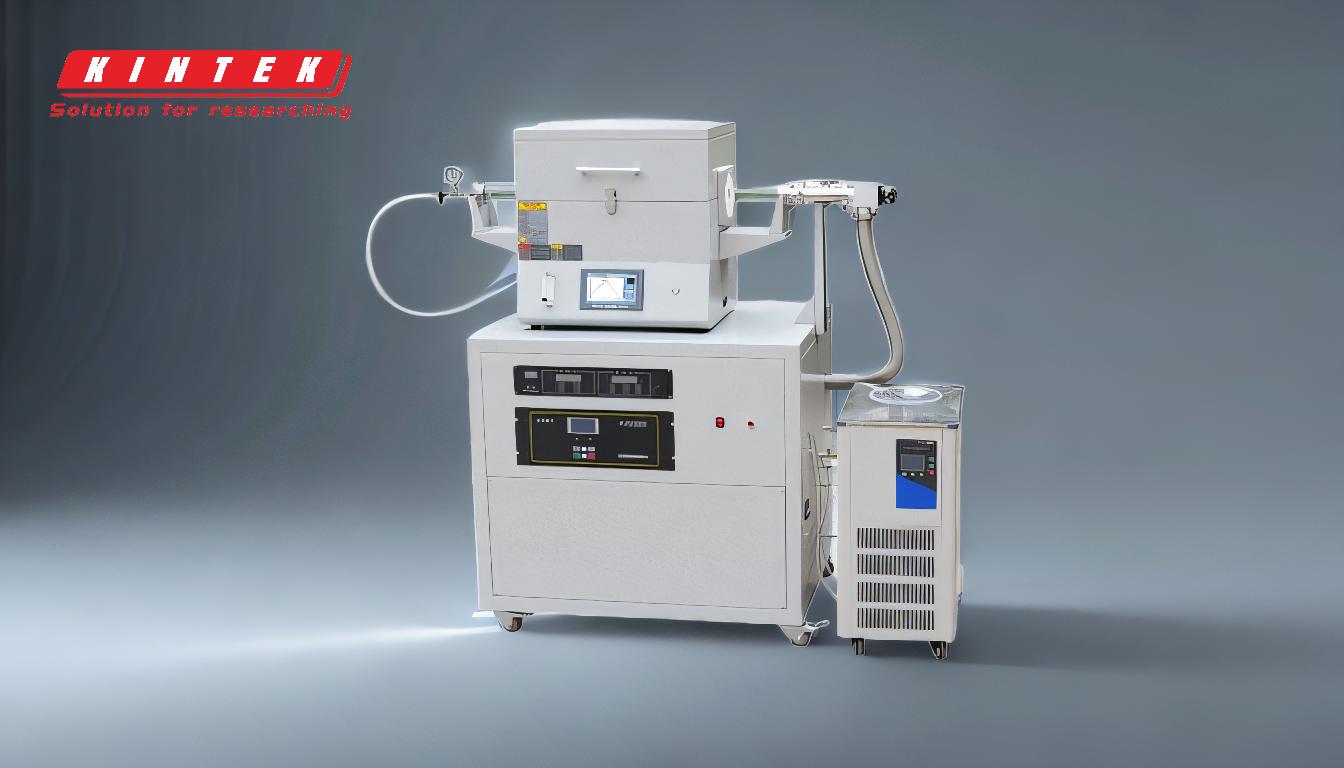
-
Heat Treatment and Annealing:
- Chamber furnaces are widely used for heat treatment processes, including annealing, which improves the ductility and malleability of metals. This process involves heating materials to a specific temperature and then cooling them slowly to reduce hardness and increase toughness.
- Annealing is crucial in metallurgy and materials science, as it helps in relieving internal stresses, refining grain structure, and enhancing material properties.
-
Sintering and Hardening:
- Sintering is a process where powdered materials are heated to a temperature below their melting point, causing particles to bond and form a solid mass. This is essential in the production of ceramics, metals, and composites.
- Hardening involves heating materials to high temperatures and then rapidly cooling them (quenching) to increase hardness and strength. This is commonly used in the manufacturing of tools and machine parts.
-
Ashing and Calcination:
- Ashing is the process of burning off organic material from a sample, leaving behind inorganic residues. This is often used in analytical chemistry to determine the ash content of materials.
- Calcination involves heating materials to high temperatures to drive off volatile substances, decompose compounds, or induce phase transitions. This is common in the production of cement, lime, and ceramics.
-
Crystal Growth and Carbon Nanotube Production:
- Chamber furnaces are used in the growth of single crystals, which are essential in electronics, optics, and materials science. The controlled environment ensures the formation of high-quality crystals.
- Carbon nanotube production involves the synthesis of carbon nanotubes at high temperatures, which are used in nanotechnology, electronics, and composite materials.
-
Curing and Polymer Processing:
- Curing is the process of hardening a material through chemical reactions, often induced by heat. This is used in the production of polymers, coatings, and adhesives.
- Polymer curing and polyimide baking are specific applications where chamber furnaces provide the necessary heat to achieve desired material properties.
-
Thermogravimetric Analysis (TGA) and Loss on Ignition (LOI):
- TGA is a technique used to measure changes in the weight of a material as a function of temperature. This is important in material science for understanding thermal stability and composition.
- LOI analysis involves heating a sample to determine the amount of volatile material present. This is used in quality control and material characterization.
-
Quenching and Stress Relief:
- Quenching is the rapid cooling of a material to achieve specific mechanical properties, such as increased hardness. This is commonly used in the heat treatment of metals.
- Stress relief involves heating materials to a temperature below their critical point to relieve internal stresses without altering the microstructure. This is important in preventing distortion and cracking in metal parts.
-
Specialized Applications:
- Chamber furnaces are used in specialized processes such as melting glass, creating enamel coatings, producing technical ceramics, and soldering and brazing. These applications require precise temperature control and uniform heating.
- They are also used in misfire analysis, which involves testing the thermal properties of materials to ensure they meet specific performance criteria.
In summary, chamber furnaces are indispensable tools in various industries, providing the controlled high-temperature environments necessary for a wide range of material processing and analysis applications. Their versatility and precision make them essential for tasks ranging from simple heat treatment to complex material synthesis and analysis.
Summary Table:
Application | Description |
---|---|
Heat Treatment & Annealing | Improves ductility, relieves stress, and enhances material properties. |
Sintering & Hardening | Bonds powdered materials and increases hardness through rapid cooling. |
Ashing & Calcination | Burns organic material and drives off volatile substances for analysis. |
Crystal Growth & Nanotubes | Produces high-quality crystals and synthesizes carbon nanotubes. |
Curing & Polymer Processing | Hardens materials through heat-induced chemical reactions. |
TGA & LOI Analysis | Measures weight changes and volatile content for material characterization. |
Quenching & Stress Relief | Rapidly cools materials for hardness and relieves internal stresses. |
Specialized Applications | Includes glass melting, enamel coatings, technical ceramics, and misfire analysis. |
Unlock the potential of chamber furnaces for your high-temperature processes—contact our experts today!