Electron beam evaporation is a sophisticated thin-film deposition technique widely used in various industries due to its ability to handle high-melting-point materials and achieve high deposition rates. It operates by focusing an electron beam onto a target material, causing it to vaporize and deposit onto a substrate. This method is particularly advantageous for applications requiring precise and high-quality thin films, such as in laser optics, aerospace, and automotive industries. However, it comes with challenges, including high equipment costs, safety hazards, and limitations in producing dense films suitable for harsh environments. Despite these drawbacks, its versatility and efficiency make it a valuable tool in advanced material processing.
Key Points Explained:
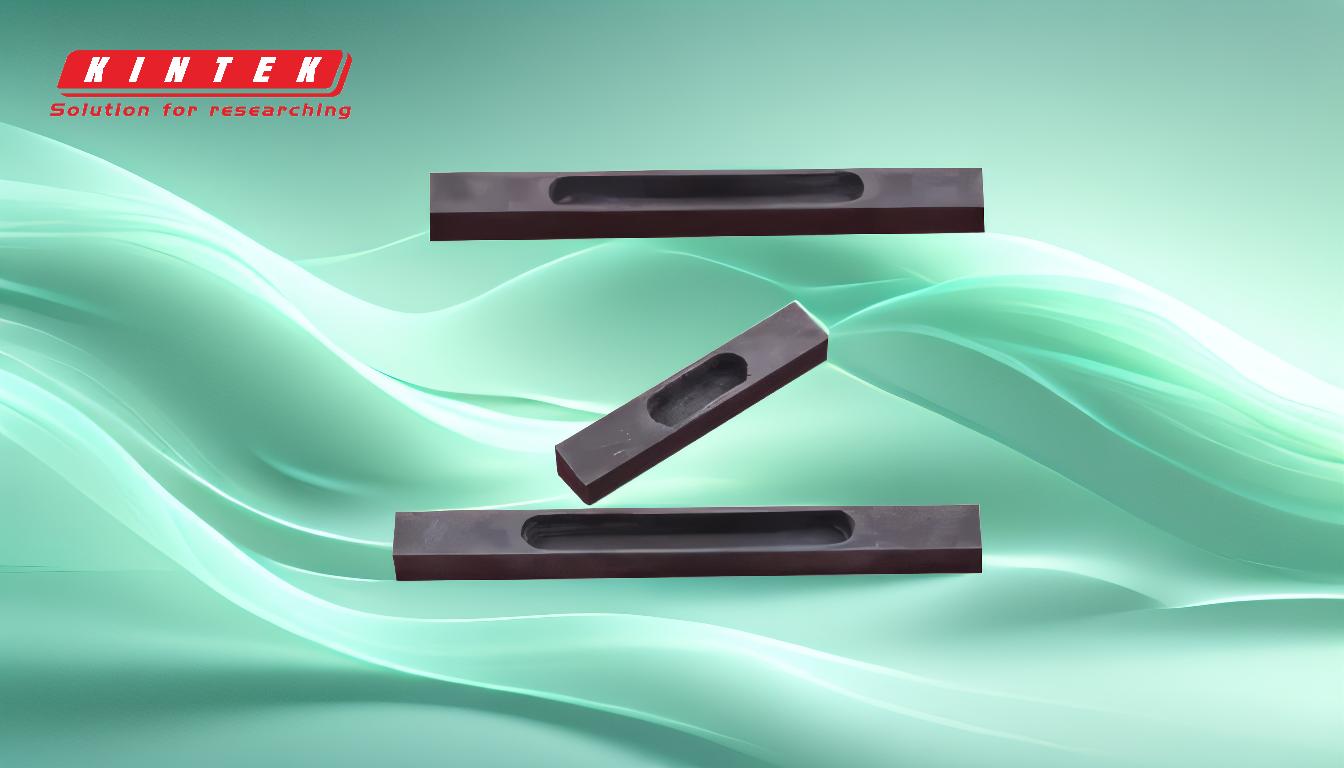
-
High-Temperature Capability:
- Electron beam evaporation can heat materials to extremely high temperatures, making it suitable for vaporizing high-melting-point materials like ceramics and metals. This is a significant advantage over traditional thermal evaporation methods, which struggle with such materials.
- Applications include the deposition of ceramic coatings, zinc oxide thin films, and protective coatings for corrosive environments.
-
Localized Heating:
- The process involves focusing an electron beam on a small area of the target material, allowing for precise and localized heating. This minimizes contamination and ensures efficient material utilization.
- This feature is particularly beneficial in applications requiring high purity, such as in the production of optical coatings for laser systems.
-
High Deposition Rates:
- Electron beam evaporation offers very high deposition rates, making it a time-efficient method for thin-film production. This is crucial for industrial applications where large-scale production is required.
- Industries such as aerospace and automotive benefit from this capability when producing coatings that require durability and high performance.
-
Versatility in Material Compatibility:
- The technique can evaporate almost any vacuum-compatible material, provided it does not decompose under high temperatures. This versatility makes it applicable across a broad range of materials, including metals, ceramics, and semiconductors.
- Examples include the growth of zinc oxide thin films and the deposition of protective coatings for use in harsh environments.
-
Challenges and Limitations:
- Cost and Complexity: The equipment for electron beam evaporation is significantly more expensive and complex compared to traditional methods like filament or boat evaporation. This can be a barrier for smaller labs or budget-constrained projects.
- Safety Hazards: The process involves high voltages, posing significant safety risks that require careful handling and robust safety protocols.
- Porosity of Deposited Layers: The films produced by electron beam evaporation are often porous, which limits their suitability for applications in climatic or corrosive environments where dense, impermeable coatings are required.
-
Applications in Key Industries:
- Laser Optics: The method is ideal for producing high-quality optical coatings used in laser systems, where precision and performance are critical.
- Aerospace and Automotive: Electron beam evaporation is used to create protective coatings that can withstand high temperatures and corrosive conditions, making it valuable in these industries.
- Research and Development: The technique is also employed in R&D for concentrating solutions and extracting inorganic pollutants, highlighting its importance in scientific advancements.
In summary, electron beam evaporation is a powerful and versatile technique with significant advantages in handling high-melting-point materials and achieving high deposition rates. However, its high cost, safety concerns, and limitations in film density must be carefully considered when selecting it for specific applications. Its widespread use in industries like laser optics, aerospace, and automotive underscores its importance in advanced material processing and thin-film technology.
Summary Table:
Aspect | Details |
---|---|
High-Temperature Capability | Vaporizes high-melting-point materials like ceramics and metals. |
Localized Heating | Precise heating minimizes contamination, ideal for high-purity applications. |
High Deposition Rates | Enables fast, large-scale production of thin films. |
Material Compatibility | Works with metals, ceramics, and semiconductors. |
Challenges | High cost, safety hazards, and porous film limitations. |
Applications | Laser optics, aerospace, automotive, and R&D. |
Learn how electron beam evaporation can elevate your material processing—contact our experts today!