Microwave sintering is a modern technique that leverages the dielectric properties of materials to achieve sintering and densification in a highly efficient and energy-saving manner. Unlike traditional sintering methods, microwave sintering provides uniform heating, reduces internal temperature gradients, and enables rapid sintering at lower temperatures. This method is particularly advantageous for ceramic materials, offering faster heating rates, improved material density, and fine-grained structures. It also has applications in metal sintering, 3D printing, and surface property enhancement, making it a versatile and promising technology for material preparation and manufacturing.
Key Points Explained:
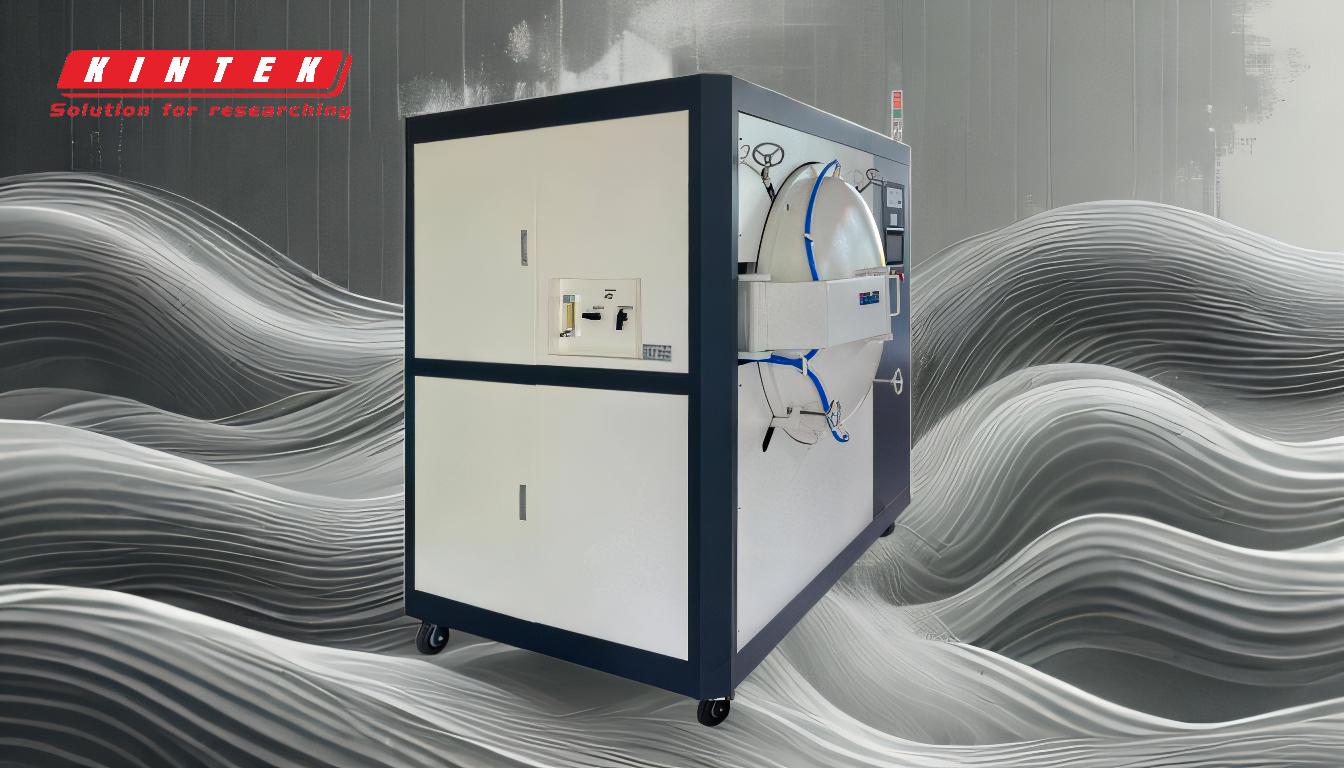
-
Mechanism of Microwave Sintering:
- Microwave sintering utilizes the dielectric loss of materials in a microwave electromagnetic field. This means that the material absorbs microwave energy, causing its molecules to vibrate and generate heat internally. This internal heating mechanism ensures uniform temperature distribution and minimizes thermal gradients, which are common issues in conventional sintering methods.
-
Advantages of Microwave Sintering:
- Fast Heating Rate: Microwave sintering achieves rapid heating, significantly reducing the time required for the sintering process compared to traditional methods.
- Low-Temperature Sintering: It enables sintering at lower temperatures, which is particularly beneficial for materials that are sensitive to high temperatures or prone to thermal degradation.
- Energy Efficiency: The method is highly energy-efficient, as it directly heats the material rather than relying on external heat sources.
- Improved Material Properties: Microwave sintering results in better material density and fine-grained structures, enhancing the mechanical and physical properties of the sintered products.
-
Applications of Microwave Sintering:
- Ceramic Materials: Microwave sintering is widely used in the preparation of ceramic materials, offering uniform heating and improved material properties. It is particularly suitable for advanced ceramics used in electronics, aerospace, and biomedical applications.
- Metal Sintering: This method is effective for sintering metal particles, especially those with high melting points. It avoids the need to reach melting temperatures, saving energy and allowing for greater control over the sintering process.
- 3D Printing: Microwave sintering is increasingly used in 3D printing to form custom metal shapes. It enables precise control over the sintering process, resulting in consistent and high-quality printed parts.
- Surface Property Enhancement: By reducing the porosity of material surfaces, microwave sintering improves properties such as strength, wear resistance, and corrosion resistance.
-
Comparison with Conventional Sintering:
- Temperature Control: Microwave sintering offers better temperature control, reducing the risk of overheating and thermal stress.
- Heating Uniformity: The uniform heating provided by microwave sintering minimizes internal temperature gradients, leading to more consistent material properties.
- Process Speed: The rapid heating and sintering speeds of microwave sintering significantly reduce processing time, increasing production efficiency.
-
Future Prospects:
- Microwave sintering has broad application prospects in various industries, including electronics, aerospace, automotive, and biomedical engineering. Its ability to produce high-quality materials with improved properties at lower energy costs makes it a promising technology for future material development and manufacturing processes.
In summary, microwave sintering is a cutting-edge technology that offers numerous advantages over traditional sintering methods. Its ability to provide uniform heating, fast sintering speeds, and improved material properties makes it a valuable tool for a wide range of applications, from ceramics to metals and 3D printing. As industries continue to seek more efficient and sustainable manufacturing processes, microwave sintering is likely to play an increasingly important role.
Summary Table:
Aspect | Details |
---|---|
Mechanism | Uses dielectric loss to generate internal heat, ensuring uniform heating. |
Advantages | Fast heating, low-temperature sintering, energy efficiency, improved density. |
Applications | Ceramics, metal sintering, 3D printing, surface property enhancement. |
Comparison | Better temperature control, uniform heating, faster processing than traditional methods. |
Future Prospects | Promising for electronics, aerospace, automotive, and biomedical industries. |
Unlock the potential of microwave sintering for your materials—contact our experts today to learn more!