Zinc vaporization refers to the process by which zinc transitions from a solid or liquid state to a gaseous state. This occurs when zinc is heated to its boiling point, which is approximately 907°C (1665°F). Vaporization is a critical aspect in various industrial processes, such as galvanizing, alloy production, and metallurgical operations. Understanding zinc vaporization is essential for controlling its behavior in high-temperature environments, ensuring efficient material usage, and minimizing waste. The process is influenced by factors such as temperature, pressure, and the presence of other elements or compounds.
Key Points Explained:
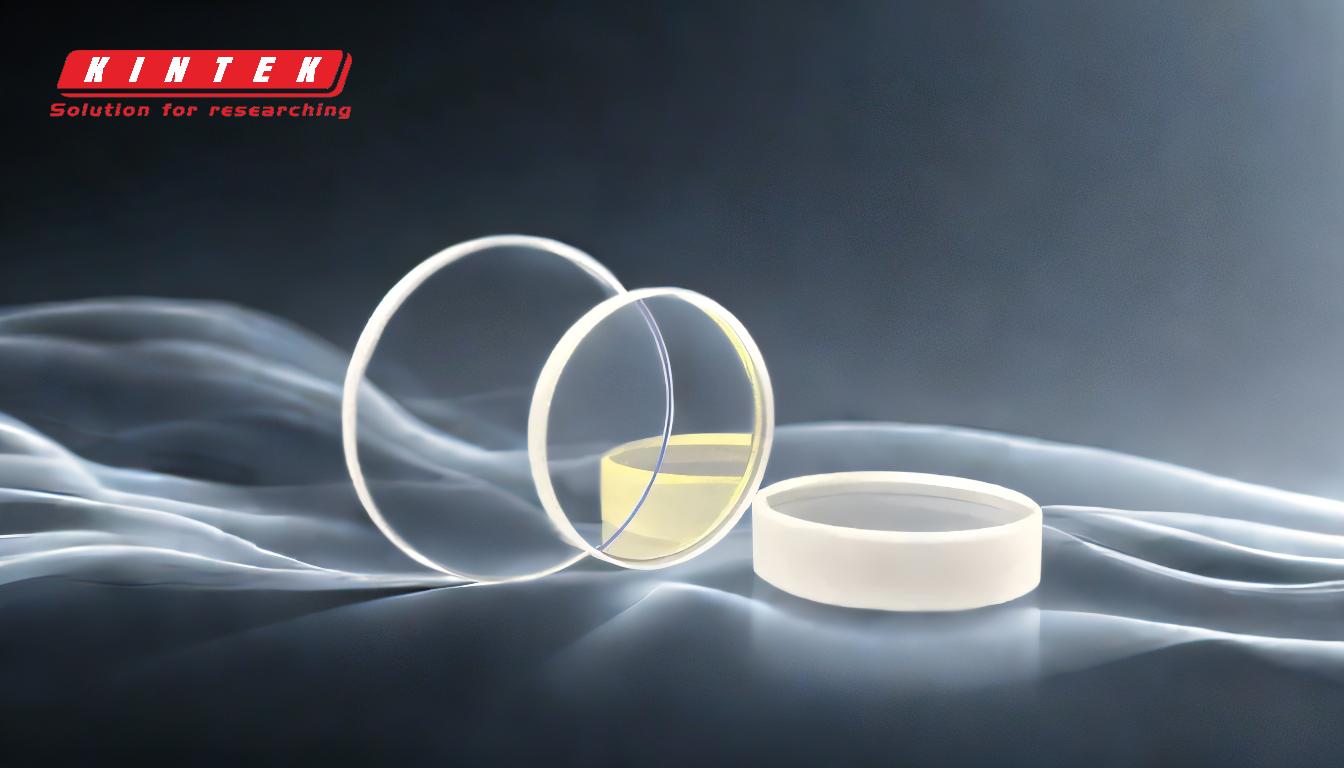
-
Definition of Zinc Vaporization:
- Zinc vaporization is the phase transition of zinc from a solid or liquid state to a gaseous state. This occurs when zinc is heated to its boiling point, which is approximately 907°C (1665°F). At this temperature, the thermal energy overcomes the intermolecular forces holding the zinc atoms together, allowing them to escape into the gas phase.
-
Factors Influencing Zinc Vaporization:
- Temperature: The primary factor affecting zinc vaporization is temperature. As the temperature increases, the kinetic energy of the zinc atoms increases, leading to a higher rate of vaporization.
- Pressure: The vaporization rate is also influenced by the surrounding pressure. Lower pressures can lower the boiling point of zinc, making it easier to vaporize.
- Environmental Conditions: The presence of other elements or compounds can affect the vaporization process. For example, in a reducing atmosphere, zinc oxide (ZnO) can be reduced to metallic zinc, which then vaporizes.
-
Industrial Applications:
- Galvanizing: In the galvanizing process, zinc vaporization is used to coat steel or iron with a protective layer of zinc. The metal is heated in a zinc bath, and the vaporized zinc adheres to the surface, providing corrosion resistance.
- Alloy Production: Zinc vaporization is also important in the production of zinc-based alloys. By controlling the vaporization process, manufacturers can ensure the desired composition and properties of the alloy.
- Metallurgical Operations: In metallurgy, zinc vaporization is used to separate zinc from other metals or impurities. This is particularly important in the recovery of zinc from ores or recycled materials.
-
Challenges and Considerations:
- Loss of Material: One of the main challenges in zinc vaporization is the potential loss of material due to excessive vaporization. This can lead to inefficiencies and increased costs.
- Environmental Impact: The release of zinc vapor into the atmosphere can have environmental consequences. Proper containment and filtration systems are necessary to minimize emissions.
- Safety Concerns: Zinc vapor can be hazardous to human health if inhaled. Adequate ventilation and protective measures are essential in environments where zinc vaporization occurs.
-
Control and Optimization:
- Temperature Control: Precise control of temperature is crucial to optimize the vaporization process. This ensures that zinc vaporizes at the desired rate without excessive loss or waste.
- Pressure Management: Adjusting the pressure in the vaporization environment can help control the boiling point and rate of vaporization.
- Use of Additives: In some cases, additives can be used to modify the vaporization behavior of zinc. For example, certain fluxes can reduce the vaporization rate, improving efficiency.
-
Future Developments:
- Advanced Materials: Research is ongoing to develop new materials and coatings that can withstand higher temperatures, reducing the need for zinc vaporization in certain applications.
- Sustainable Practices: Efforts are being made to develop more sustainable methods of zinc vaporization, such as using renewable energy sources or recycling zinc vapor for reuse.
- Automation and Monitoring: Advances in automation and real-time monitoring technologies are expected to improve the precision and efficiency of zinc vaporization processes.
In conclusion, zinc vaporization is a critical process in various industrial applications, but it requires careful control and management to ensure efficiency, safety, and environmental sustainability. Understanding the factors that influence zinc vaporization and implementing best practices can help optimize the process and minimize its challenges.
Summary Table:
Aspect | Details |
---|---|
Definition | Transition of zinc from solid/liquid to gas at ~907°C (1665°F). |
Key Influencing Factors | Temperature, pressure, and environmental conditions. |
Industrial Applications | Galvanizing, alloy production, and metallurgical operations. |
Challenges | Material loss, environmental impact, and safety concerns. |
Optimization Strategies | Temperature control, pressure management, and use of additives. |
Future Developments | Advanced materials, sustainable practices, and automation. |
Optimize your zinc vaporization process today—contact our experts for tailored solutions!