Radio Frequency (RF) magnetron sputtering is a sophisticated technique used to deposit thin films of materials onto substrates. It operates by generating a plasma in a vacuum chamber, where a target material is bombarded by energetic ions, causing atoms to be ejected and subsequently deposited onto a substrate. The process is enhanced by the use of a magnetic field, which confines electrons near the target surface, increasing ionization and plasma density. This method is particularly effective for depositing high-quality coatings, especially for insulating materials, due to its ability to operate at lower voltages and higher currents, resulting in faster deposition rates and better film quality.
Key Points Explained:
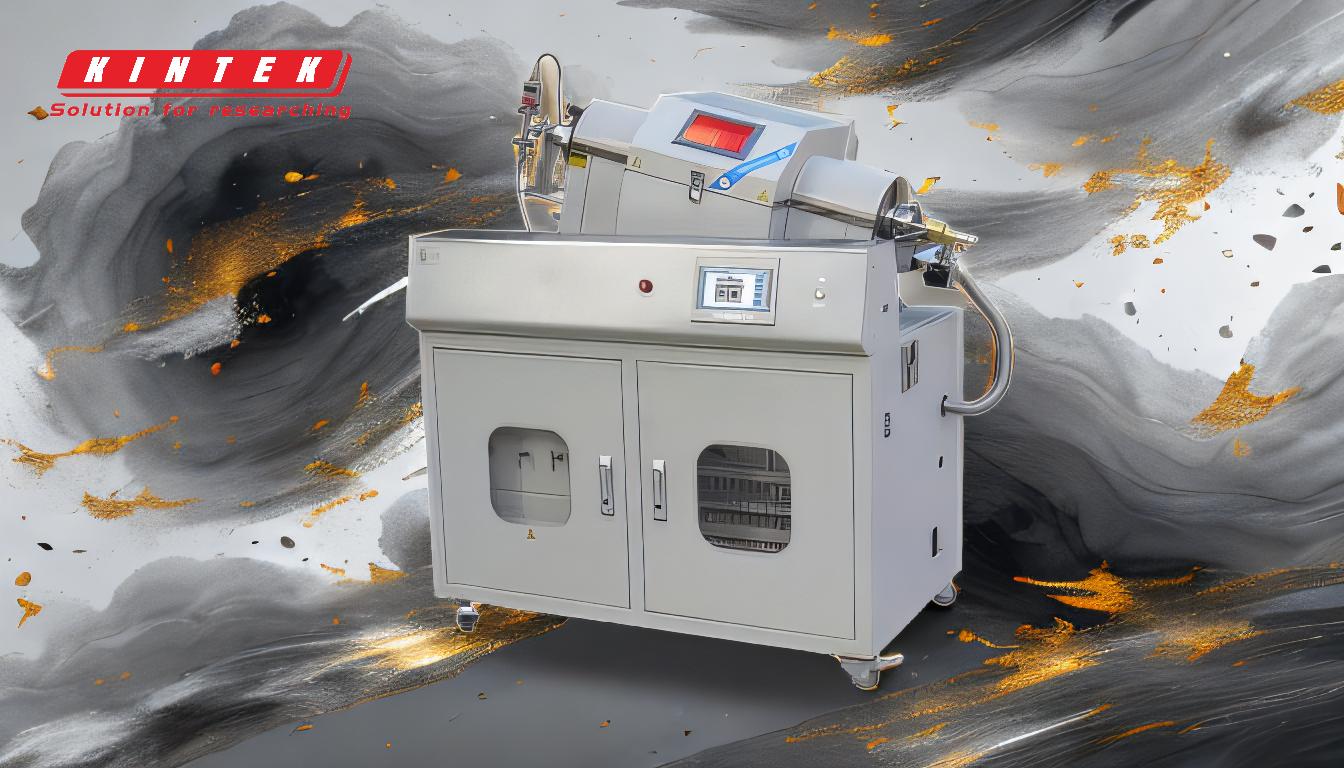
-
Generation of Plasma:
- Inert Gas Introduction: An inert gas, typically argon, is introduced into the vacuum chamber. This gas is ionized to form a plasma.
- Plasma Formation: High voltage is applied to create a gaseous plasma near the target’s magnetic field. This plasma contains argon gas atoms, argon ions, and free electrons.
-
Role of Magnetic Field:
- Electron Confinement: The magnetic field forces electrons to follow a circular trajectory, increasing their residence time in the plasma. This confinement enhances the ionization of gas molecules, leading to a higher density of ions.
- Enhanced Ionization: The increased electron residence time results in more collisions between electrons and argon atoms, generating secondary electrons that further boost plasma density.
-
Sputtering Process:
- Ion Bombardment: A negative voltage (typically around 300 V) is applied to the target, attracting positively charged ions from the plasma. These ions bombard the target surface with high kinetic energy.
- Atom Ejection: When the energy transferred by the ions exceeds the surface binding energy of the target material (about three times the binding energy), atoms are ejected from the target surface.
-
Deposition of Thin Film:
- Atom Transportation: The ejected atoms travel through the vacuum and deposit onto the substrate surface. This process follows the principle of momentum conversion, where the high kinetic energy of the sputtered atoms ensures a uniform and adherent film.
- Film Formation: The deposited atoms form a thin film on the substrate, creating a coating with desired properties.
-
Key Parameters:
- Target Power Density: Influences the rate at which atoms are ejected from the target.
- Gas Pressure: Affects the mean free path of the sputtered atoms and the plasma density.
- Substrate Temperature: Can impact the film’s microstructure and adhesion.
- Deposition Rate: Determines how quickly the film is formed and can affect film quality.
-
Advantages of RF Magnetron Sputtering:
- High-Quality Coatings: The high plasma density and controlled environment result in films with excellent uniformity, adhesion, and purity.
- Versatility: Suitable for a wide range of materials, including metals, alloys, and insulating ceramics.
- Efficiency: Operates at lower voltages and higher currents, allowing for faster deposition rates and reduced energy consumption.
-
Applications:
- Semiconductor Industry: Used for depositing thin films in the fabrication of integrated circuits and other electronic components.
- Optical Coatings: Applied in the production of anti-reflective coatings, mirrors, and other optical devices.
- Decorative and Protective Coatings: Utilized in the automotive and aerospace industries for both aesthetic and functional purposes.
In summary, RF magnetron sputtering is a highly effective method for depositing thin films, leveraging the principles of plasma generation, magnetic confinement, and ion bombardment to achieve high-quality coatings. Its versatility and efficiency make it a preferred choice in various industries, from electronics to optics and beyond.
Summary Table:
Aspect | Details |
---|---|
Plasma Generation | Inert gas (argon) ionized to form plasma; high voltage applied for ionization. |
Magnetic Field Role | Confines electrons, increasing plasma density and ionization efficiency. |
Sputtering Process | Ions bombard target, ejecting atoms for deposition onto the substrate. |
Key Parameters | Target power density, gas pressure, substrate temperature, deposition rate. |
Advantages | High-quality coatings, versatility, efficiency, and faster deposition rates. |
Applications | Semiconductors, optical coatings, decorative and protective coatings. |
Unlock the potential of RF magnetron sputtering for your projects—contact our experts today!