The working principle of a vacuum brazing furnace revolves around creating a controlled environment where metals can be joined without oxidation or contamination. The process involves heating the workpiece in a vacuum chamber, using a filler material with a lower melting point than the base material, and achieving a solid-solid connection without melting the base material. The vacuum environment removes oxygen, preventing oxide formation and ensuring clean, high-quality brazed joints. This method is widely used in industries like aerospace, particle physics, and metallurgical research due to its precision, repeatability, and ability to handle complex geometries.
Key Points Explained:
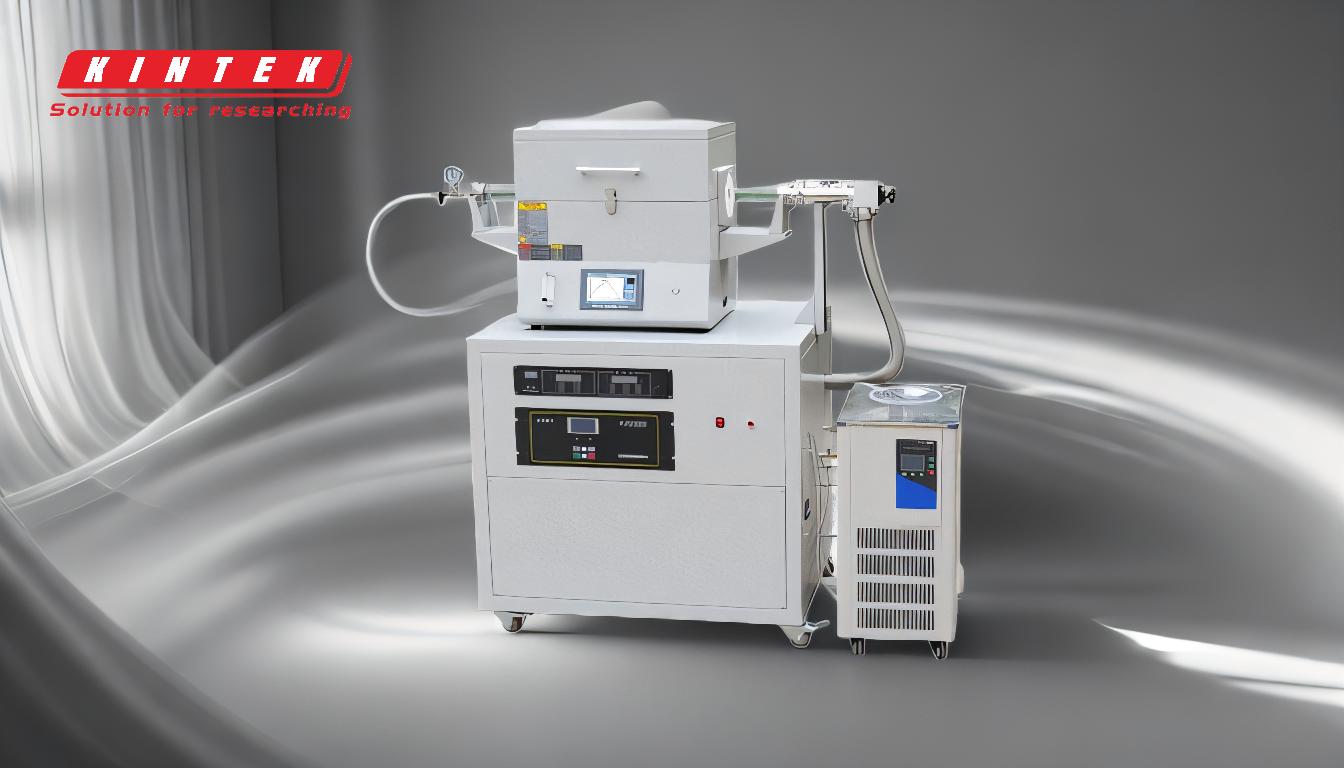
-
Vacuum Environment Creation:
- The vacuum brazing furnace operates by removing oxygen from the heating chamber, which prevents oxidation of the metals during the heating process. This ensures that the metals remain uncontaminated and free from oxide layers, which could otherwise interfere with the brazing process.
- The vacuum system typically includes a mechanical vacuum pump and a diffusion pump. The mechanical pump initially lowers the pressure, and the diffusion pump further reduces it to the required vacuum level for brazing.
-
Heating System:
- The heating system in a vacuum brazing furnace is designed to provide uniform and precise heating to the workpiece. It heats the parts and melts the brazing filler material, which has a lower melting point than the base material.
- The furnace operates at temperatures higher than the oxide formation temperature, allowing any oxidized pieces to lose their oxide layer before brazing. This ensures a clean and strong joint.
-
Process Steps:
- Workpiece Placement: The assembled workpiece is placed into the vacuum chamber.
- Vacuum Creation: The mechanical vacuum pump is started to lower the pressure, followed by the diffusion pump to achieve the required vacuum level.
- Heating: The workpiece is heated while maintaining the vacuum. The temperature is controlled automatically by a temperature control instrument.
- Brazing: The filler material melts and flows into the joint, creating a solid-solid connection without melting the base material.
- Cooling: The workpiece is cooled to a safe temperature before removal to avoid oxidation.
-
Advantages of Vacuum Brazing:
- No Flux Usage: The absence of flux eliminates the risk of corrosion and contamination.
- Design Flexibility: Fewer structural design restrictions allow for better product performance and complex geometries.
- High-Quality Joints: The process results in smooth, dense brazing seams with excellent quality.
- Efficiency: Short production cycles, low cost, and pollution-free operation make it an environmentally friendly and economical choice.
-
Applications:
- Vacuum brazing furnaces are used in high-precision industries such as aerospace, particle physics, and metallurgical research. They meet stringent requirements like NADCAP certification and offer sophisticated cycle programming for precision.
-
Safety and Maintenance:
- Operators must be trained and certified, wear necessary protective equipment, and maintain a clean and unobstructed workplace.
- Regular maintenance includes checking water, power, and gas supplies, ensuring proper vacuum levels, and adhering to maintenance schedules to ensure safe and efficient operation.
By understanding these key points, one can appreciate the precision, efficiency, and versatility of vacuum brazing furnaces in modern manufacturing and research applications.
Summary Table:
Key Aspect | Description |
---|---|
Vacuum Environment | Removes oxygen to prevent oxidation, ensuring uncontaminated metal surfaces. |
Heating System | Provides uniform and precise heating, melting filler material for strong joints. |
Process Steps | Workpiece placement, vacuum creation, heating, brazing, and controlled cooling. |
Advantages | No flux usage, design flexibility, high-quality joints, and eco-friendly operation. |
Applications | Aerospace, particle physics, metallurgical research, and high-precision industries. |
Safety & Maintenance | Requires trained operators, protective equipment, and regular maintenance. |
Discover how vacuum brazing furnaces can enhance your manufacturing process—contact our experts today!