Thin film deposition in semiconductors is a critical process used to create ultra-thin layers of material, typically less than 1000 nanometers thick, on a substrate. This technique is essential for manufacturing semiconductor devices, integrated circuits, and micro/nano devices. The process involves depositing materials in a vacuum chamber using methods such as thermal evaporation, sputtering, ion beam deposition, or chemical vapor deposition. Thin film deposition enables precise control over material properties, making it indispensable for applications in electronics, solar panels, optical devices, and nanotechnology. Its role in sustainable technologies and modern electronics underscores its importance in advancing technological innovation.
Key Points Explained:
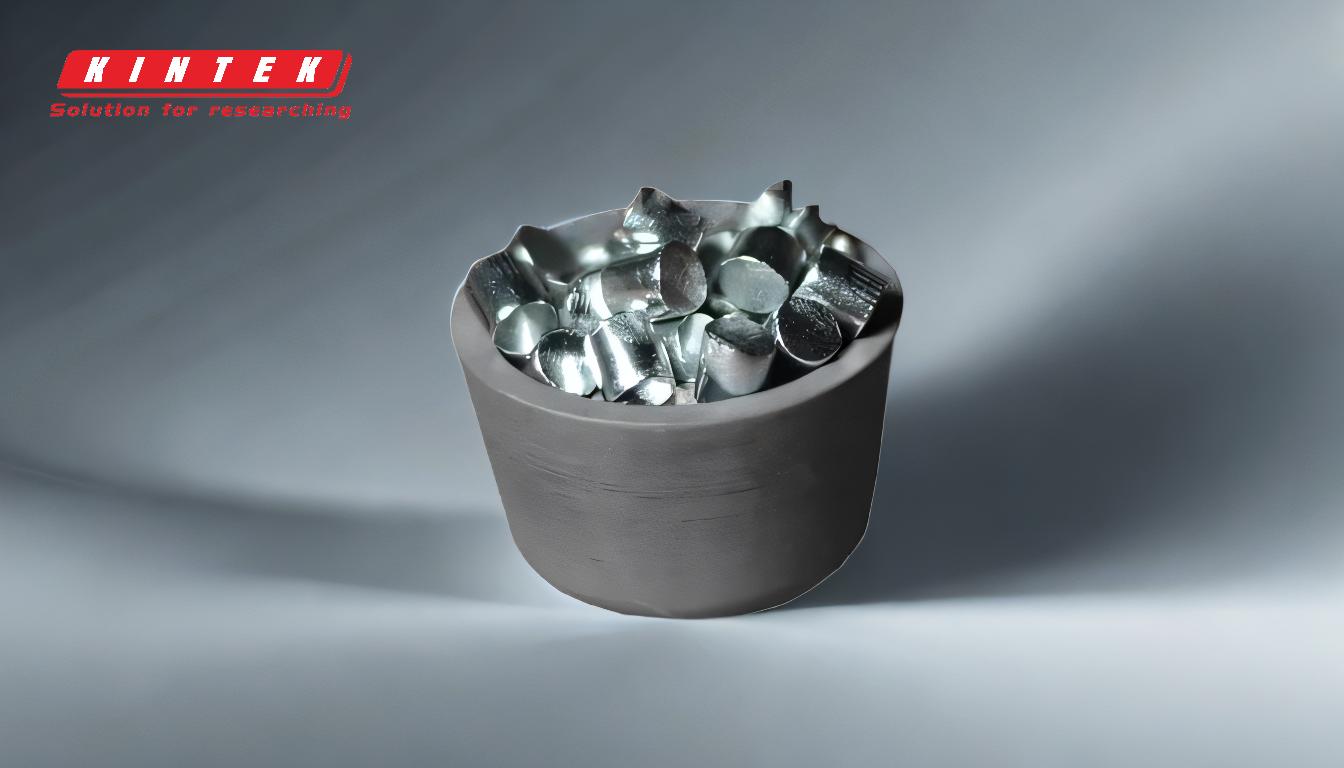
-
Definition and Purpose of Thin Film Deposition
- Thin film deposition is the process of creating extremely thin layers of material (often less than 1000 nanometers) on a substrate.
- It is a foundational technique in semiconductor manufacturing, enabling the production of integrated circuits, micro/nano devices, and other advanced technologies.
- The process is critical for achieving precise material properties, such as conductivity, insulation, or optical characteristics, which are essential for modern electronics.
-
Applications in Semiconductors and Beyond
- Thin film deposition is integral to semiconductor device fabrication, including transistors, memory chips, and sensors.
- It is also used in optical devices (e.g., lenses and mirrors), solar panels, disk drives, and CDs.
- The technique is becoming a cornerstone of nanotechnology, enabling the development of nanoscale devices and materials.
-
Process Overview
- The process occurs in a vacuum chamber to minimize contamination and ensure precise control.
- Materials are deposited onto a substrate by converting them from a solid, liquid, or gaseous state into a thin film.
- Common methods include:
- Thermal Evaporation: Heating a material until it vaporizes and condenses on the substrate.
- Sputtering: Bombarding a target material with ions to eject atoms, which then deposit onto the substrate.
- Chemical Vapor Deposition (CVD): Using chemical reactions to deposit a thin film from a gas phase.
- Ion Beam Deposition: Directing a focused ion beam to deposit material onto the substrate.
-
Importance in Sustainable Technologies
- Thin film deposition supports the development of renewable energy technologies, such as solar panels and energy storage systems.
- By enabling the production of high-efficiency materials, it helps reduce carbon emissions and minimize waste.
- Its role in sustainable technology highlights its relevance to addressing global environmental challenges.
-
Benefits and Advantages
- Precision: Allows for the creation of ultra-thin, uniform layers with controlled properties.
- Versatility: Applicable to a wide range of materials, including metals, semiconductors, and insulators.
- Scalability: Suitable for both small-scale research and large-scale industrial production.
- Innovation: Facilitates advancements in nanotechnology and next-generation electronics.
-
Challenges and Considerations
- The process requires specialized equipment and controlled environments, making it costly and complex.
- Achieving consistent film quality and adhesion can be challenging, especially for nanoscale applications.
- Material selection and process optimization are critical to ensure desired performance and reliability.
-
Future Prospects
- Thin film deposition is expected to play a key role in the development of advanced semiconductors, quantum computing, and flexible electronics.
- Ongoing research aims to improve deposition techniques, reduce costs, and expand the range of materials that can be used.
- Its integration with emerging technologies will continue to drive innovation across multiple industries.
By understanding the principles, applications, and significance of thin film deposition, stakeholders in the semiconductor industry can make informed decisions about equipment and consumables, ensuring optimal performance and cost-effectiveness in their processes.
Summary Table:
Aspect | Details |
---|---|
Definition | Creation of ultra-thin material layers (<1000 nm) on a substrate. |
Applications | Semiconductors, solar panels, optical devices, nanotechnology. |
Methods | Thermal evaporation, sputtering, CVD, ion beam deposition. |
Benefits | Precision, versatility, scalability, innovation. |
Challenges | High cost, complexity, and material selection challenges. |
Future Prospects | Quantum computing, flexible electronics, sustainable technologies. |
Discover how thin film deposition can revolutionize your processes—contact our experts today!