Thin-film technology in semiconductors refers to the process of creating extremely thin layers of materials, often just a few micrometers thick, to form functional components like transistors, solar cells, or sensors. These thin layers are deposited onto substrates such as silicon wafers or flexible materials, enabling the production of compact, lightweight, and highly efficient semiconductor devices. This technology is widely used in applications ranging from consumer electronics (e.g., smartphones, OLED displays) to renewable energy (e.g., solar panels) and advanced systems like MEMS and biomedical devices. Its ability to reduce space, weight, and wiring errors makes it a cornerstone of modern electronics and semiconductor innovation.
Key Points Explained:
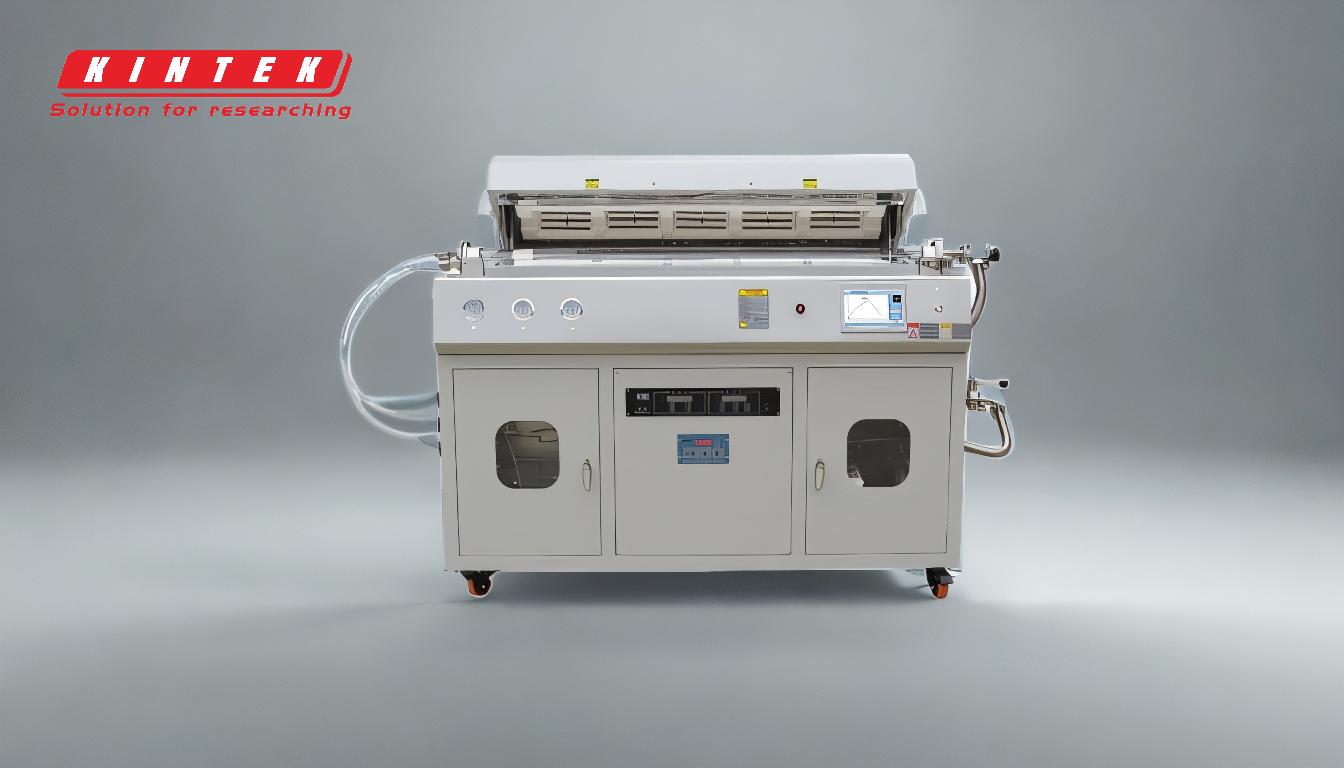
-
Definition of Thin-Film Technology in Semiconductors
- Thin-film technology involves depositing layers of materials, often just a few micrometers thick, onto substrates to create semiconductor devices.
- The "thin" aspect refers to the nanometer or micrometer thickness of these layers, while the "film" refers to the layered construction method.
- This technology is critical for producing compact, lightweight, and high-performance semiconductor components.
-
Applications in Semiconductors
- Consumer Electronics: Used in foldable smartphones, OLED displays, smartwatches, and computers.
- Renewable Energy: Essential for photovoltaic solar cells and thin-film batteries.
- Advanced Systems: Applied in micro-electromechanical systems (MEMS), LED displays, and biomedical devices.
- Industrial and Aerospace: Utilized in automotive systems, communication devices, and aerospace equipment due to its flexibility and space-saving properties.
-
Key Advantages of Thin-Film Technology
- Flexibility: Thin films can be deposited on flexible substrates, enabling dynamic and bendable devices.
- Reduced Size and Weight: Thin layers minimize the overall size and weight of semiconductor devices, making them ideal for portable electronics.
- Improved Efficiency: Enhances performance in applications like solar cells and LEDs by optimizing light absorption and energy conversion.
- Cost-Effectiveness: Thin-film processes can reduce material usage and manufacturing costs compared to traditional methods.
-
Materials and Processes
- Materials: Common materials include silicon, gallium arsenide, and organic compounds, chosen based on the desired electrical and optical properties.
- Deposition Techniques: Methods like chemical vapor deposition (CVD), physical vapor deposition (PVD), and atomic layer deposition (ALD) are used to create precise, uniform thin films.
- Substrates: Thin films are deposited on substrates such as silicon wafers, glass, or flexible polymers, depending on the application.
-
Role in Semiconductor Innovation
- Thin-film technology enables the development of next-generation devices, such as flexible displays, wearable electronics, and high-efficiency solar panels.
- It supports advancements in miniaturization, energy efficiency, and integration of multiple functions into a single device.
- The quality and type of thin-film coatings directly impact the performance and application of semiconductor devices, making it a key area of research and development.
-
Future Trends and Challenges
- Emerging Applications: Thin-film technology is expanding into areas like quantum computing, advanced sensors, and biodegradable electronics.
- Sustainability: Efforts are underway to develop eco-friendly materials and processes for thin-film production.
- Challenges: Issues like material degradation, scalability, and cost remain areas of focus for researchers and manufacturers.
By leveraging thin-film technology, the semiconductor industry continues to push the boundaries of innovation, enabling smaller, faster, and more efficient devices that power modern technology.
Summary Table:
Aspect | Details |
---|---|
Definition | Depositing micrometer-thin layers onto substrates to create semiconductor devices. |
Applications | Consumer electronics, renewable energy, advanced systems, industrial/aerospace. |
Key Advantages | Flexibility, reduced size/weight, improved efficiency, cost-effectiveness. |
Materials/Processes | Silicon, gallium arsenide, organic compounds; CVD, PVD, ALD deposition. |
Role in Innovation | Enables next-gen devices like flexible displays, wearables, and solar panels. |
Future Trends | Quantum computing, biodegradable electronics, eco-friendly production. |
Ready to explore how thin-film technology can transform your applications? Contact our experts today!