Vacuum brazing is a specialized joining process used to create strong, clean, and precise bonds between metal components. It is particularly valuable in industries where high-quality, oxidation-free joints are essential, such as aerospace, automotive, and electronics. The process involves heating assembled workpieces in a vacuum environment to melt a filler metal, which then flows into the joint and solidifies upon cooling. This method eliminates the need for flux, prevents oxidation, and ensures high joint integrity. Vacuum brazing is widely used for manufacturing heat exchangers, turbine components, and other critical parts requiring exceptional strength and reliability.
Key Points Explained:
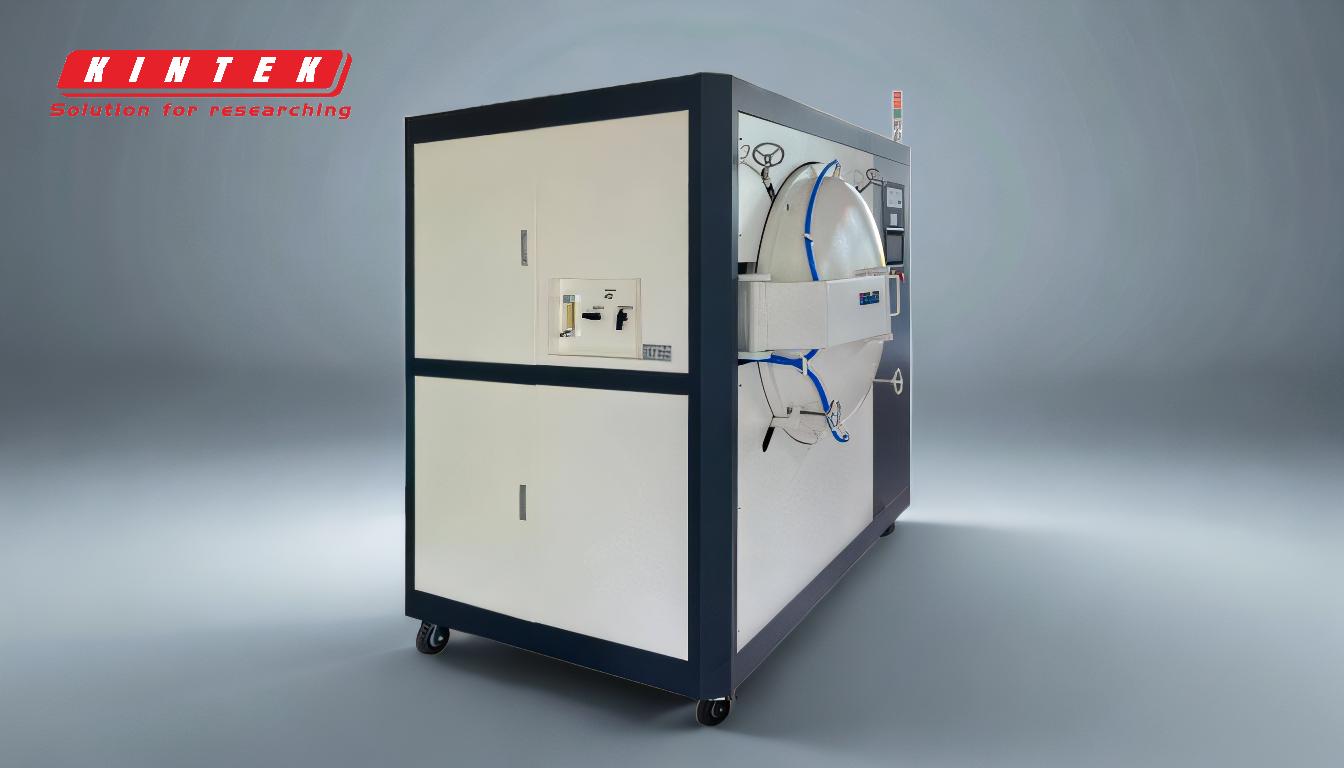
-
What is Vacuum Brazing?
- Vacuum brazing is a process that joins two or more metal components using a filler metal that melts at a temperature below the base metals' melting points. The process occurs in a vacuum environment, which prevents oxidation and contamination, ensuring clean and high-quality joints.
- The filler metal flows into the joint by capillary action, creating a strong, seamless bond upon cooling. This method is ideal for materials that are sensitive to oxidation or require precise, repeatable results.
-
Applications of Vacuum Brazing
- Aerospace Industry: Used for manufacturing turbine blades, heat exchangers, and other high-performance components where strength, reliability, and resistance to extreme conditions are critical.
- Automotive Industry: Applied in the production of fuel cells, radiators, and exhaust systems, where durability and precision are essential.
- Electronics: Utilized for creating hermetic seals in electronic components and connectors, ensuring long-term reliability.
- Medical Devices: Used in the fabrication of surgical instruments and implants, where cleanliness and biocompatibility are paramount.
-
Advantages of Vacuum Brazing
- Oxidation-Free Joints: The vacuum environment eliminates the need for flux and prevents oxidation, resulting in clean, high-quality joints.
- Precision and Repeatability: The controlled environment and automated temperature regulation ensure consistent and repeatable results.
- Strong and Reliable Joints: The process creates joints with excellent mechanical properties, including high strength and fatigue resistance.
- Versatility: Suitable for a wide range of materials, including stainless steel, titanium, and nickel-based alloys.
-
The Role of a Vacuum Brazing Furnace
- A vacuum brazing furnace is the core equipment used in this process. It consists of a vacuum system and a heating system.
- Vacuum System: Ensures the required vacuum level by using components like mechanical pumps, diffusion pumps, and Roots pumps. The highest achievable vacuum degree is typically around 7 × 10^-3 Pa.
- Heating System: Heats the workpiece to the brazing temperature, melting the filler metal without exceeding the base metals' melting points.
- The furnace operates automatically, with temperature control instruments ensuring precise heating and cooling cycles.
- A vacuum brazing furnace is the core equipment used in this process. It consists of a vacuum system and a heating system.
-
Process Steps in Vacuum Brazing
- Workpiece Preparation: Assemble the components and place them in the vacuum chamber.
- Vacuum Creation: Start the mechanical vacuum pump and, if necessary, connect the diffusion pump to achieve the desired vacuum level.
- Heating: Heat the workpiece to the brazing temperature, allowing the filler metal to melt and flow into the joint.
- Cooling: Gradually cool the workpiece in the vacuum environment to prevent oxidation and ensure joint integrity.
- Removal: Once the workpiece reaches a safe temperature, remove it from the furnace.
-
Comparison with Other Brazing Methods
- Unlike traditional brazing methods that use flux to prevent oxidation, vacuum brazing eliminates the need for flux, reducing the risk of contamination and improving joint quality.
- Compared to furnace brazing in atmospheric conditions, vacuum brazing provides cleaner joints and is better suited for sensitive materials and high-precision applications.
-
Importance in High-Tech Industries
- Vacuum brazing is critical in industries like aerospace and automotive, where components must withstand extreme conditions and meet stringent quality standards.
- The process ensures that critical parts, such as turbine blades and heat exchangers, have the necessary strength, durability, and reliability to perform in demanding environments.
By leveraging the capabilities of a vacuum brazing furnace, manufacturers can achieve superior joint quality, meet industry standards, and produce components that excel in performance and longevity.
Summary Table:
Industry | Applications |
---|---|
Aerospace | Turbine blades, heat exchangers, high-performance components |
Automotive | Fuel cells, radiators, exhaust systems |
Electronics | Hermetic seals in electronic components and connectors |
Medical Devices | Surgical instruments, implants requiring cleanliness and biocompatibility |
Learn how vacuum brazing can enhance your manufacturing process—contact us today!