Vacuum heat treatment is a specialized process used to harden metals in a vacuum environment, ensuring no oxidation or contamination occurs. This method involves removing air from a sealed chamber using a vacuum pump, creating a controlled atmosphere that allows for precise temperature management and uniform heating. The process is widely used for applications like annealing, brazing, sintering, and quenching, offering benefits such as higher purity, no scaling or discoloration, and reduced need for post-treatment cleaning. The main classifications of vacuum heat treatment include vacuum sintering, brazing, quenching, tempering, and annealing, among others.
Key Points Explained:
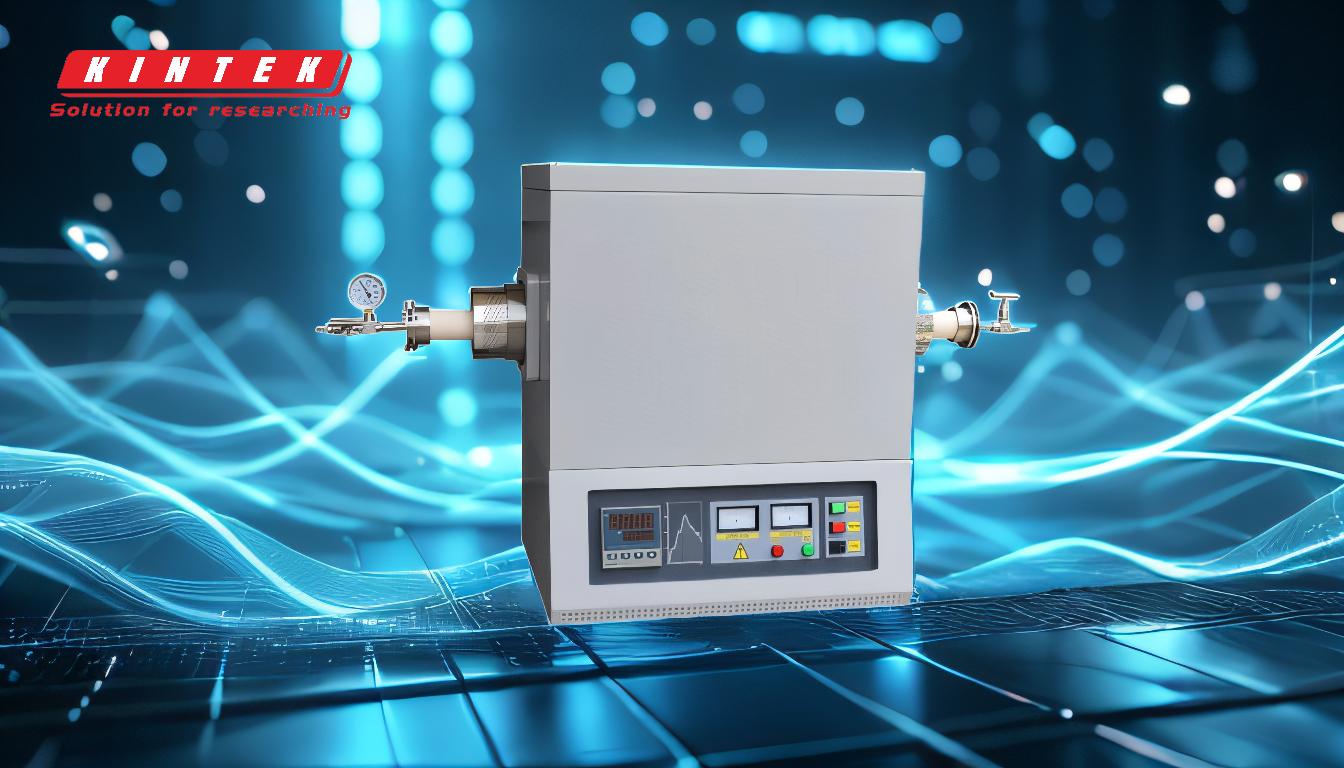
-
Definition and Process of Vacuum Heat Treatment
- Vacuum heat treatment involves heating metals in a vacuum environment, where air is removed using a vacuum pump. This ensures no oxidation or contamination occurs during the process.
- The controlled atmosphere allows for precise temperature management and uniform heating, making it ideal for processes like vacuum heat treatment, annealing, brazing, and sintering.
-
Key Benefits of Vacuum Heat Treatment
- Prevention of Oxidation: The absence of air in the chamber prevents oxidation, resulting in a higher purity end product free of contaminants and defects.
- No Scaling or Discoloration: Parts emerge from the process without scaling or discoloration, reducing the need for further cleaning or finishing.
- Ready for Further Processing: Treated parts are immediately ready for additional forming or machining, saving time and resources.
-
Main Classifications of Vacuum Heat Treatment
- Vacuum Sintering: Used for powder metallurgy to bond metal particles without melting.
- Vacuum Brazing: Involves heating under vacuum conditions to join metals using a filler material with a lower melting point.
- Vacuum Quenching and Tempering: Processes used to harden and strengthen metals while maintaining their structural integrity.
- Vacuum Annealing: Softens metals to improve their ductility and reduce internal stresses.
- Other Processes: Includes vacuum solution treatment, aging, normalizing, degassing, and magnetic annealing.
-
Applications of Vacuum Heat Treatment
- Aerospace and Automotive Industries: Used for critical components requiring high strength and durability.
- Medical Devices: Ensures high purity and precision for implants and surgical tools.
- Tool and Die Manufacturing: Enhances the hardness and wear resistance of cutting tools and molds.
-
Vacuum Brazing as a Subcategory
- Vacuum brazing is a specialized form of vacuum heat treatment where two metal pieces are joined using a filler metal. The process occurs just below the melting points of the base metals, ensuring a strong, flawless joint.
- This method is particularly useful for creating complex assemblies in industries like aerospace and electronics.
-
Vacuum Technology and Equipment
- Vacuum heat treatment relies on advanced vacuum pumping systems to achieve varying degrees of vacuum levels. High vacuum levels (low pressure) are essential for preventing contamination and ensuring consistent results.
- Modern vacuum furnaces are equipped with precise temperature controls and uniform heating mechanisms, making them indispensable for high-quality metal treatment.
By leveraging the advantages of vacuum heat treatment, industries can achieve superior metal properties, reduce post-processing steps, and enhance the overall quality of their products.
Summary Table:
Aspect | Details |
---|---|
Definition | Heating metals in a vacuum to prevent oxidation and contamination. |
Key Benefits | No scaling, higher purity, reduced post-treatment cleaning. |
Main Processes | Sintering, brazing, quenching, tempering, annealing. |
Applications | Aerospace, automotive, medical devices, tool and die manufacturing. |
Equipment | Advanced vacuum furnaces with precise temperature control. |
Learn how vacuum heat treatment can improve your metal products—contact our experts today!