Vacuum retorting is a specialized process used in various industries, particularly in metallurgy and materials science, to remove impurities, gases, and volatile components from materials under a vacuum environment. This process is essential for producing high-purity metals, alloys, and other materials that require precise control over their composition and properties. By operating under a vacuum, the process minimizes contamination from atmospheric gases and ensures a controlled environment for refining and purification.
Key Points Explained:
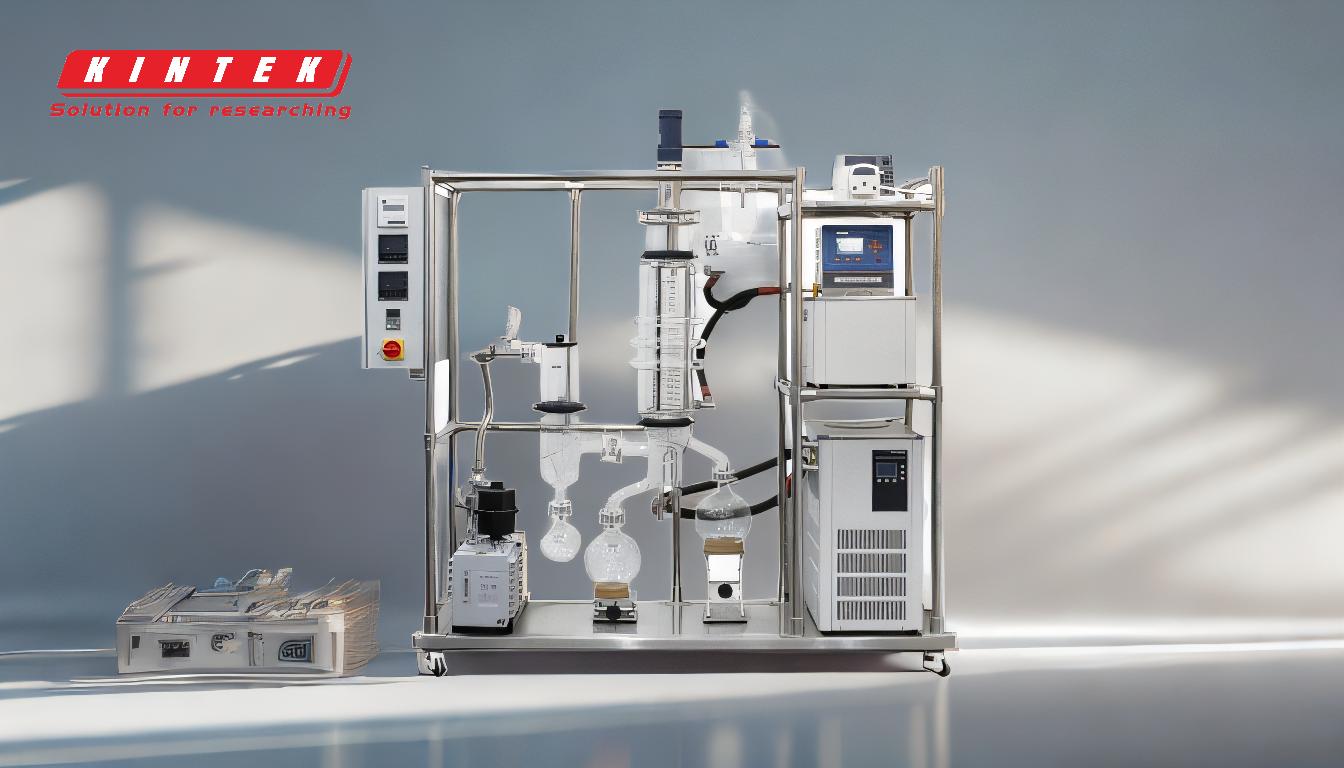
-
Definition of Vacuum Retorting:
- Vacuum retorting involves heating materials in a vacuum environment to remove impurities, gases, and volatile components. This process is crucial for refining metals and alloys, as well as for producing high-purity materials in industries like aerospace, electronics, and energy.
-
Importance of Vacuum Environment:
- The vacuum environment is critical because it prevents contamination from atmospheric gases such as oxygen and nitrogen. These gases can react with certain metals and alloys, leading to undesirable properties like brittleness or oxidation. By operating under a vacuum, the process ensures a clean and controlled environment for refining.
-
Applications in Metallurgy:
- Vacuum retorting is widely used in metallurgical processes, such as vacuum induction melting (VIM) and vacuum arc remelting (VAR). In these processes, metals are melted and refined under vacuum to achieve uniform composition and remove impurities. This is particularly important for producing high-performance alloys used in critical applications like jet engines, medical devices, and nuclear reactors.
-
Comparison to Other Vacuum Processes:
- While vacuum retorting focuses on purification and refining, other vacuum processes like vacuum forming and vacuum induction melting serve different purposes. For example, vacuum forming is used to shape materials by applying force and cooling them to achieve desired designs, whereas vacuum induction melting involves melting metals under vacuum to refine their composition and remove impurities.
-
Advantages of Vacuum Retorting:
- The primary advantage of vacuum retorting is its ability to produce high-purity materials with precise control over their properties. This is essential for industries that require materials with specific mechanical, thermal, or chemical characteristics. Additionally, the process reduces waste and improves the efficiency of material utilization.
-
Equipment and Process Details:
- The equipment used in vacuum retorting typically includes a vacuum chamber, heating elements, and a crucible or container for holding the material. The process involves heating the material to a specific temperature under vacuum, allowing volatile components to evaporate and be removed. The remaining material is then cooled and solidified, resulting in a purified product.
-
Challenges and Considerations:
- One of the challenges of vacuum retorting is maintaining a consistent vacuum environment throughout the process. Any leaks or fluctuations in pressure can compromise the quality of the final product. Additionally, the process requires precise control over temperature and heating rates to ensure effective purification without damaging the material.
-
Future Trends and Innovations:
- As industries demand higher-purity materials with advanced properties, vacuum retorting technology continues to evolve. Innovations in vacuum chamber design, heating methods, and process automation are improving the efficiency and scalability of the process. These advancements are enabling the production of next-generation materials for emerging applications in renewable energy, biotechnology, and advanced manufacturing.
By understanding the principles and applications of vacuum retorting, manufacturers and researchers can leverage this process to develop high-quality materials that meet the stringent requirements of modern industries.
Summary Table:
Key Aspect | Details |
---|---|
Definition | Heating materials in a vacuum to remove impurities and volatile components. |
Importance of Vacuum | Prevents contamination from atmospheric gases like oxygen and nitrogen. |
Applications | Metallurgy (e.g., VIM, VAR), aerospace, electronics, and energy industries. |
Advantages | Produces high-purity materials with precise control over properties. |
Equipment | Vacuum chamber, heating elements, and crucible for material containment. |
Challenges | Maintaining consistent vacuum and precise temperature control. |
Future Trends | Innovations in chamber design, heating methods, and automation. |
Discover how vacuum retorting can enhance your material quality—contact our experts today!