A vacuum tube furnace is a specialized heating device designed for high-temperature processes in a controlled, vacuum environment. It combines the features of a tube furnace and a vacuum furnace, allowing for precise temperature control and uniformity while minimizing contamination. The furnace typically uses a quartz or alumina tube as the heating chamber, which is sealed to create a vacuum or controlled atmosphere. This setup is ideal for applications such as sintering, annealing, brazing, and degassing, where high temperatures and a contamination-free environment are critical. Vacuum tube furnaces are widely used in materials science, metallurgy, and ceramics for processes like ceramic firing, metal heat treatment, and research experiments requiring precise thermal conditions.
Key Points Explained:
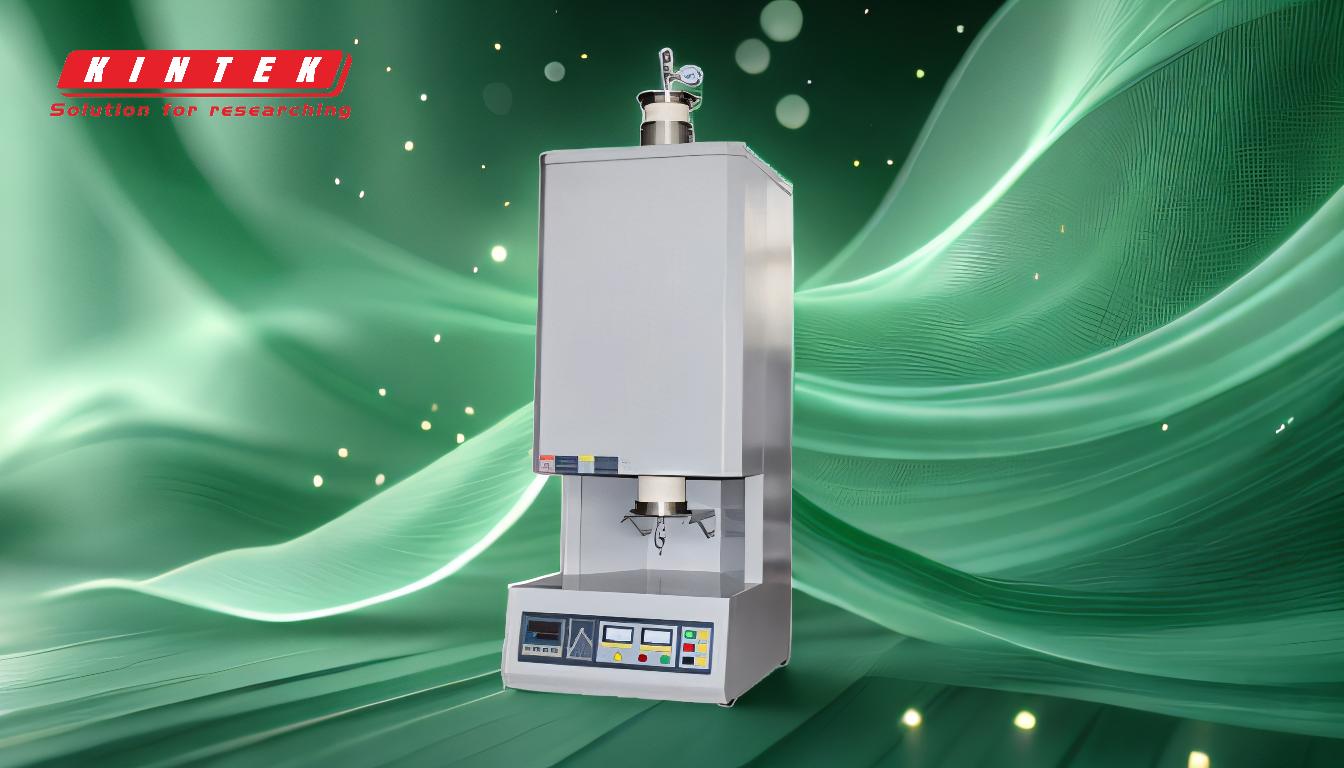
-
Definition and Purpose:
- A vacuum tube furnace is a heating device that integrates the features of a tube furnace and a vacuum furnace. It is designed to heat materials to very high temperatures in a vacuum or controlled atmosphere, ensuring minimal contamination and precise thermal control.
- It is used for processes such as sintering, annealing, brazing, degassing, and ceramic-metal sealing, where high temperatures and a clean environment are essential.
-
Components and Structure:
- The furnace typically consists of:
- A cylindrical heating chamber made of quartz or alumina, which serves as the work tube.
- A vacuum pump and fittings to create and maintain the vacuum environment.
- Heating elements (often made of high-resistance alloys or silicon carbide) positioned around the tube for uniform heat distribution.
- A thermally insulating outer shell to maintain temperature stability.
- A sealing flange (usually stainless steel) to ensure airtight conditions.
- These components work together to provide precise temperature control and a contamination-free environment.
- The furnace typically consists of:
-
Working Principle:
- The furnace operates by sealing the work tube and using a vacuum pump to remove air and gases, creating a vacuum or introducing a specific atmosphere (e.g., inert gas).
- Heating is conducted in this controlled environment, which prevents oxidation, decarburization, and contamination of the materials being processed.
- Temperature is regulated using feedback from thermocouples, ensuring uniformity and accuracy.
-
Applications:
- Ceramic Firing: Used to fire ceramics in a contamination-free environment, ensuring high-quality results.
- Metal Heat Treatment: Ideal for processes like annealing, hardening, and tempering, where precise temperature control is critical.
- Brazing and Soldering: Provides a clean environment for joining metals without oxidation.
- Degassing and Sintering: Removes gases from materials and consolidates powders into solid components.
- Research and Development: Commonly used in laboratories for experiments requiring precise thermal conditions and controlled atmospheres.
-
Advantages:
- Contamination-Free Environment: The vacuum or controlled atmosphere eliminates oxidation and contamination, ensuring high-purity results.
- Precise Temperature Control: Advanced temperature regulation systems provide uniform heating and accurate temperature measurement.
- Versatility: Suitable for a wide range of materials and processes, from ceramics to metals.
- Energy Efficiency: The insulating design minimizes heat loss, making it more energy-efficient than traditional furnaces.
-
Comparison with Other Furnaces:
- Unlike conventional furnaces, a vacuum tube furnace operates in a vacuum or controlled atmosphere, which prevents contamination and oxidation.
- Compared to standard tube furnaces, it offers better temperature uniformity and is more suitable for processes requiring high purity.
- It is smaller and more specialized than industrial vacuum furnaces, making it ideal for laboratory and small-scale production use.
-
Key Considerations for Purchasers:
- Temperature Range: Ensure the furnace meets the required temperature limits for your applications.
- Tube Material: Choose between quartz and alumina tubes based on the maximum temperature and chemical compatibility with your materials.
- Vacuum Level: Consider the vacuum pump's capacity to achieve the desired pressure for your processes.
- Control System: Look for advanced temperature control and monitoring features for precise thermal management.
- Size and Capacity: Select a furnace with an appropriate tube diameter and length to accommodate your samples.
In summary, a vacuum tube furnace is a versatile and precise heating device that combines the benefits of vacuum technology and tube furnace design. It is indispensable for applications requiring high temperatures, contamination-free environments, and accurate thermal control.
Summary Table:
Feature | Description |
---|---|
Purpose | Combines tube furnace and vacuum furnace features for high-temperature processes. |
Key Components | Quartz/alumina tube, vacuum pump, heating elements, insulating shell, sealing flange. |
Applications | Ceramic firing, metal heat treatment, brazing, degassing, and R&D. |
Advantages | Contamination-free, precise temperature control, versatile, energy-efficient. |
Key Considerations | Temperature range, tube material, vacuum level, control system, size & capacity. |
Ready to enhance your lab's capabilities? Contact us today to find the perfect vacuum tube furnace for your needs!