Vapor deposition in chemical physics, particularly chemical vapor deposition (CVD), is a sophisticated process used to create thin films and coatings on various substrates such as glass, metals, and ceramics. This technique involves the transport of gaseous reactants to a substrate surface, where they undergo chemical reactions to form a solid deposit. The process is highly versatile and is employed across industries like electronics, cutting tools, and solar cell manufacturing. CVD requires precise control over parameters such as temperature, pressure, and gas flow, making it a skill-intensive process. The resulting thin films are used for applications ranging from corrosion resistance to semiconductor fabrication.
Key Points Explained:
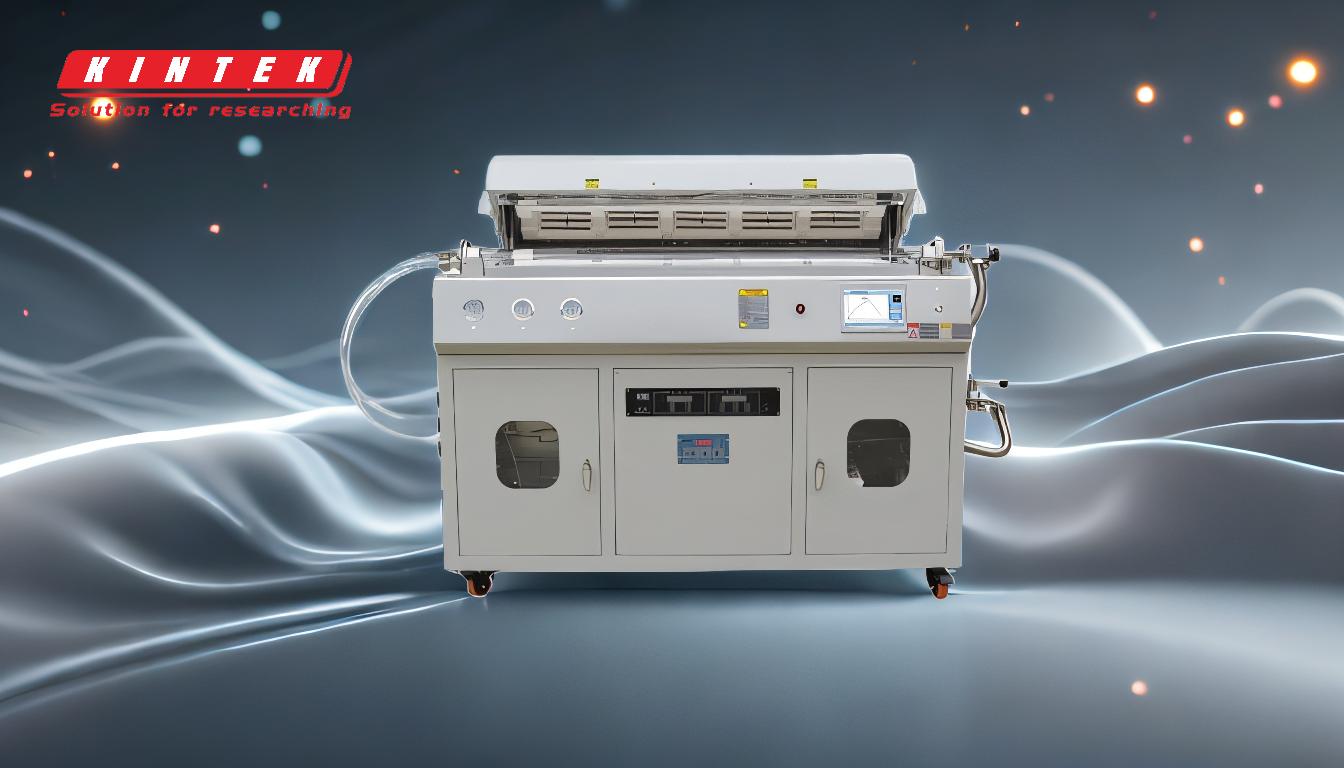
-
Definition and Overview of CVD:
- Chemical vapor deposition (CVD) is a process where gaseous reactants are chemically transformed into a solid material on a substrate. This method is widely used to produce thin films and coatings with high precision and uniformity.
-
Steps Involved in CVD:
- The CVD process consists of several sequential steps:
- Transport of Reacting Gases: The gaseous species are delivered to the substrate surface.
- Adsorption: The gas molecules adhere to the substrate surface.
- Surface-Catalyzed Reactions: Chemical reactions occur on the surface, facilitated by heat or other energy sources.
- Surface Diffusion: The reacted species move to growth sites on the substrate.
- Nucleation and Growth: The thin film begins to form and grow layer by layer.
- Desorption and Transport of Byproducts: Gaseous byproducts are removed from the surface, ensuring clean film growth.
- The CVD process consists of several sequential steps:
-
Applications of CVD:
- CVD is utilized in multiple industries due to its ability to deposit high-quality thin films:
- Electronics: Used for depositing thin films on semiconductors, essential for integrated circuits and microelectronics.
- Cutting Tools: Provides wear-resistant and corrosion-resistant coatings, extending tool life.
- Solar Cells: Enables the deposition of photovoltaic materials on substrates for efficient energy conversion.
- CVD is utilized in multiple industries due to its ability to deposit high-quality thin films:
-
Materials Deposited via CVD:
- CVD can deposit a wide range of materials, including:
- Metals: Such as tungsten and copper.
- Nonmetallic Composites: Including carbon, silicon, carbides, nitrides, and oxides.
- Intermetallics: Used in specialized applications requiring unique material properties.
- CVD can deposit a wide range of materials, including:
-
Energy Sources for CVD Reactions:
- The energy required for the chemical reactions in CVD can be supplied by:
- Heat: Thermal CVD is the most common method.
- Light: Photochemical CVD uses light energy to drive reactions.
- Electric Discharge: Plasma-enhanced CVD (PECVD) uses electrical energy to generate reactive species.
- The energy required for the chemical reactions in CVD can be supplied by:
-
Advantages of CVD:
- High Purity: Produces films with minimal impurities.
- Uniformity: Ensures consistent film thickness across large areas.
- Versatility: Suitable for a wide range of materials and substrates.
- Scalability: Can be adapted for both small-scale and industrial-scale production.
-
Challenges in CVD:
- Complexity: Requires precise control over process parameters.
- Cost: High equipment and operational costs.
- Skill Requirement: Demands a high level of expertise to achieve optimal results.
By understanding these key points, one can appreciate the significance of chemical vapor deposition in modern technology and its role in advancing materials science and engineering.
Summary Table:
Aspect | Details |
---|---|
Definition | CVD transforms gaseous reactants into solid materials on substrates. |
Steps | Transport, adsorption, reactions, diffusion, nucleation, and desorption. |
Applications | Electronics, cutting tools, solar cells. |
Materials Deposited | Metals, nonmetallic composites, intermetallics. |
Energy Sources | Heat, light, electric discharge. |
Advantages | High purity, uniformity, versatility, scalability. |
Challenges | Complexity, cost, skill requirements. |
Interested in leveraging CVD for your applications? Contact us today to learn more!