Vapor deposition is a critical process in thin film technology, used to apply thin layers of material onto a substrate within a vacuum chamber. This technique involves vaporizing a target material, which then condenses onto the substrate, forming a thin film. The process is widely used in industries to modify surface properties such as conductivity, wear resistance, corrosion resistance, and optical or electrical characteristics. Vapor deposition can be achieved through various methods, including thermal evaporation, sputtering, and chemical vapor deposition, each with distinct advantages depending on the application. The resulting thin films, ranging from nanometers to micrometers in thickness, are essential for enhancing the performance of materials in electronics, optics, and engineering components.
Key Points Explained:
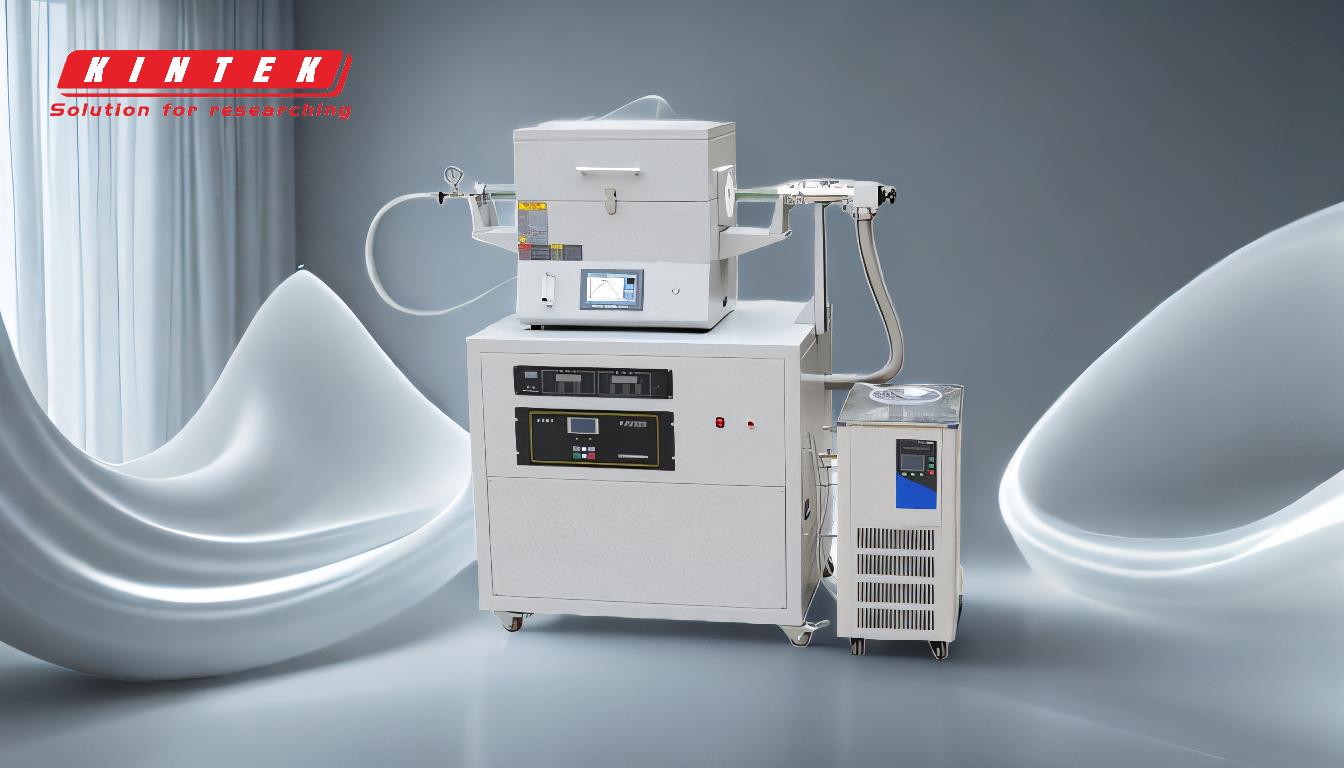
-
Definition of Vapor Deposition:
- Vapor deposition is a process where a material is vaporized and then deposited onto a substrate to form a thin film.
- This process typically occurs in a vacuum chamber to ensure controlled conditions and uniformity in the coating.
-
Purpose and Applications:
- Vapor deposition is used to modify the surface properties of materials, such as improving conductivity, wear resistance, corrosion resistance, or optical/electrical properties.
- Applications include:
- Enhancing the optical properties of glass (e.g., anti-reflective coatings).
- Improving the corrosive resistance of metals.
- Modifying the electrical properties of semiconductors.
-
Types of Vapor Deposition Techniques:
- Thermal Evaporation: A target material is heated until it vaporizes, and the vapor condenses onto the substrate.
- Sputtering: A high-energy ion beam bombards the target material, causing atoms to be ejected and deposited onto the substrate.
- Chemical Vapor Deposition (CVD): A chemical reaction occurs in the gas phase, producing a solid material that deposits onto the substrate.
- Ion Beam Deposition: A focused ion beam is used to sputter material onto the substrate, offering precise control over film properties.
-
Process Characteristics:
- Vacuum Environment: The process occurs in a vacuum chamber to ensure uniform deposition and prevent contamination.
- Material Vaporization: The target material is vaporized using heat, plasma, or chemical reactions, depending on the technique.
- Film Thickness: The resulting thin films range from a few nanometers to about 100 micrometers, depending on the application.
-
Advantages of Vapor Deposition:
- Uniformity: The vacuum environment ensures consistent purity and thickness of the coating.
- Versatility: A wide range of materials, including metals, semiconductors, and ceramics, can be deposited.
- Precision: Techniques like sputtering and ion beam deposition allow for precise control over film properties.
-
Challenges and Considerations:
- Cost: High-energy processes and vacuum equipment can be expensive.
- Complexity: Some techniques, such as CVD, require precise control of chemical reactions and gas flow.
- Material Limitations: Not all materials are suitable for vapor deposition due to differences in vaporization temperatures and reactivity.
-
Industry Use Cases:
- Electronics: Vapor deposition is used to create thin films for semiconductors, transistors, and integrated circuits.
- Optics: Anti-reflective and reflective coatings are applied to lenses and mirrors.
- Engineering Components: Thin films are used to enhance the durability and performance of tools, molds, and mechanical parts.
-
Future Trends:
- Development of new materials and techniques for more efficient and cost-effective deposition.
- Integration of vapor deposition with additive manufacturing (3D printing) for advanced material design.
- Increased use in renewable energy applications, such as solar cells and energy storage devices.
By understanding the principles and applications of vapor deposition, purchasers of equipment and consumables can make informed decisions about the best techniques and materials for their specific needs. This knowledge is essential for optimizing performance, reducing costs, and ensuring the longevity of coated components.
Summary Table:
Aspect | Details |
---|---|
Definition | Process of vaporizing and depositing material onto a substrate in a vacuum. |
Applications | Improves conductivity, wear resistance, corrosion resistance, and more. |
Techniques | Thermal evaporation, sputtering, CVD, ion beam deposition. |
Advantages | Uniform coatings, versatility, and precision. |
Challenges | High cost, complexity, and material limitations. |
Industry Use Cases | Electronics, optics, engineering components. |
Future Trends | Integration with 3D printing, renewable energy applications. |
Discover how vapor deposition can transform your materials—contact our experts today!