Vapor deposition of polymers is a process used to create thin polymer films or coatings on substrates by transforming polymer materials into a vapor state and then depositing them onto a surface. This method is widely used in industries such as electronics, automotive, and medical devices due to its ability to produce uniform, high-quality coatings. The process typically involves heating the polymer material to create a vapor, which is then transported to the substrate under vacuum conditions. Once the vapor reaches the substrate, it condenses and forms a solid coating. This technique is particularly useful for applications requiring precise control over film thickness, uniformity, and material properties.
Key Points Explained:
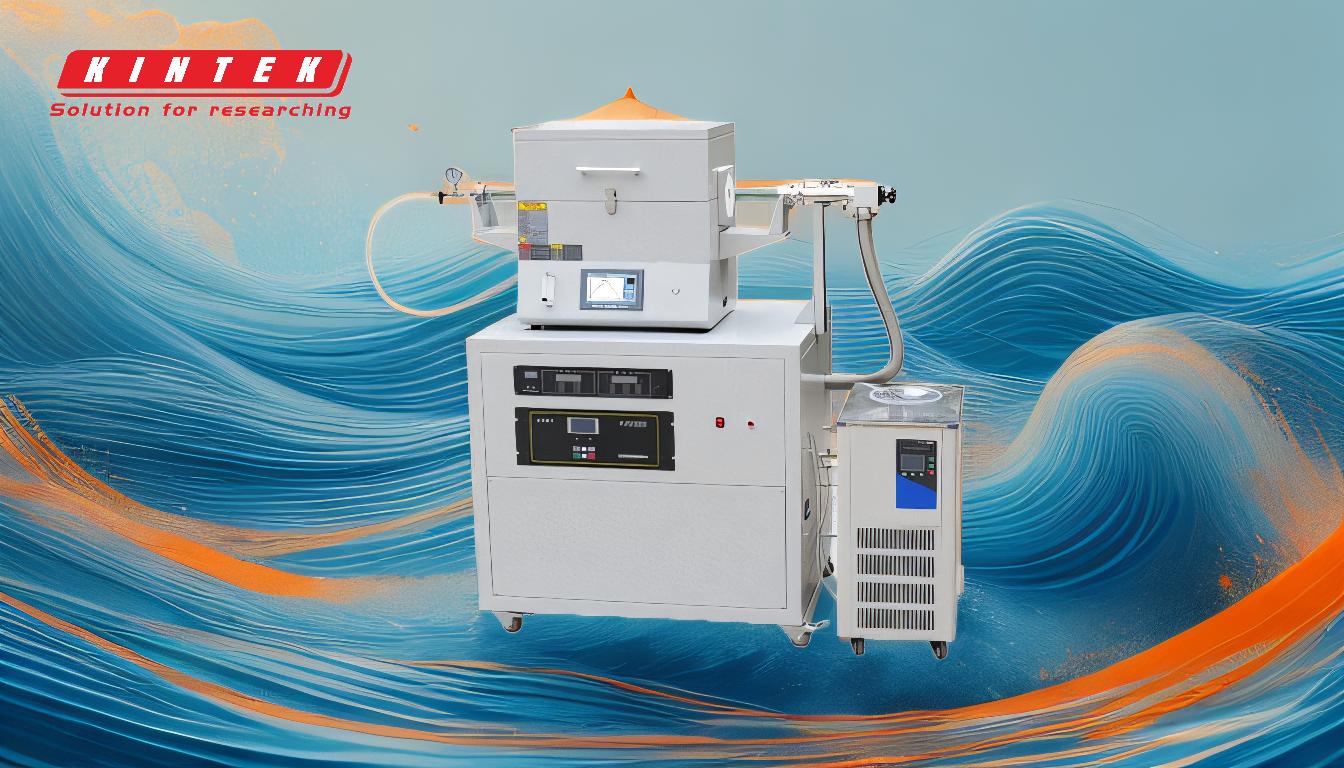
-
Definition and Overview of Vapor Deposition of Polymers:
- Vapor deposition of polymers involves converting polymer materials into a vapor state and then depositing them onto a substrate to form a thin film or coating.
- This process is part of a broader category of vapor deposition technologies, which also includes methods like chemical vapor deposition (CVD) and physical vapor deposition (PVD).
- The technique is particularly valued for its ability to produce uniform, high-quality coatings with precise control over thickness and material properties.
-
Process of Vapor Deposition:
- Heating and Vaporization: The polymer material is heated to a temperature where it vaporizes. This can be done using various heat sources, depending on the specific requirements of the material and the application.
- Transportation of Vapor: The vaporized polymer is then transported to the substrate. This is typically done under vacuum conditions to prevent contamination and to ensure a controlled environment.
- Deposition and Condensation: Once the vapor reaches the substrate, it condenses and forms a solid coating. The substrate may be cooled to facilitate this process.
- Control of Film Properties: The thickness, uniformity, and other properties of the film can be controlled by adjusting parameters such as temperature, pressure, and the rate of vapor deposition.
-
Applications of Vapor Deposition of Polymers:
- Electronics: Vapor-deposited polymer films are used in electronic packaging, transistors, and other components where thin, uniform coatings are required.
- Automotive: The technique is used to apply protective coatings to automotive parts, enhancing their durability and resistance to corrosion.
- Medical Devices: Polymer coatings applied via vapor deposition are used in medical devices to improve biocompatibility and to provide protective barriers.
- Holographic Displays: Vapor deposition is used to create thin films for holographic displays, where precise control over film properties is essential.
-
Advantages of Vapor Deposition of Polymers:
- Uniformity: The process allows for the creation of highly uniform coatings, which is critical for many applications.
- Precision: Vapor deposition offers precise control over film thickness and other properties, making it suitable for applications requiring high accuracy.
- Versatility: A wide range of polymer materials can be deposited using this technique, making it versatile for various industrial applications.
- Quality: The high-quality coatings produced by vapor deposition are often superior to those produced by other methods, particularly in terms of purity and performance.
-
Comparison with Other Deposition Techniques:
- Chemical Vapor Deposition (CVD): While CVD is primarily used for depositing inorganic materials, vapor deposition of polymers is specifically tailored for organic materials. CVD involves chemical reactions on the substrate surface, whereas polymer vapor deposition typically relies on physical processes like condensation.
- Physical Vapor Deposition (PVD): PVD involves the physical transfer of material from a source to a substrate, often using techniques like sputtering or evaporation. Polymer vapor deposition can be considered a subset of PVD, but it specifically deals with polymer materials.
-
Challenges and Considerations:
- Material Compatibility: Not all polymers are suitable for vapor deposition. The material must be able to vaporize without decomposing, which can limit the range of polymers that can be used.
- Process Control: Achieving the desired film properties requires careful control of process parameters, which can be complex and may require specialized equipment.
- Cost: Vapor deposition systems can be expensive, and the process may not be cost-effective for all applications, particularly those requiring large-scale production.
In summary, vapor deposition of polymers is a sophisticated technique that offers significant advantages in terms of film quality, uniformity, and precision. It is widely used across various industries, though it does come with certain challenges that need to be carefully managed.
Summary Table:
Aspect | Details |
---|---|
Process | Heating, vaporization, transportation, deposition, and condensation of polymers. |
Applications | Electronics, automotive, medical devices, holographic displays. |
Advantages | Uniformity, precision, versatility, high-quality coatings. |
Challenges | Material compatibility, process control, cost. |
Comparison with CVD/PVD | Tailored for organic materials; relies on physical processes like condensation. |
Discover how vapor deposition of polymers can elevate your projects—contact us today for expert guidance!