The VAR (Vacuum Arc Remelting) process is a specialized industrial refining technique used to produce high-quality metals and alloys. It operates under inert conditions, ensuring minimal contamination. The process involves remelting a consumable electrode with a predefined composition using a direct current electric arc within a water-cooled copper crucible. The refining occurs in the arc zone between the electrode tip and the molten metal pool, with controlled solidification of the ingot from the bottom upwards. This method is particularly effective for producing materials with enhanced purity, uniformity, and mechanical properties.
Key Points Explained:
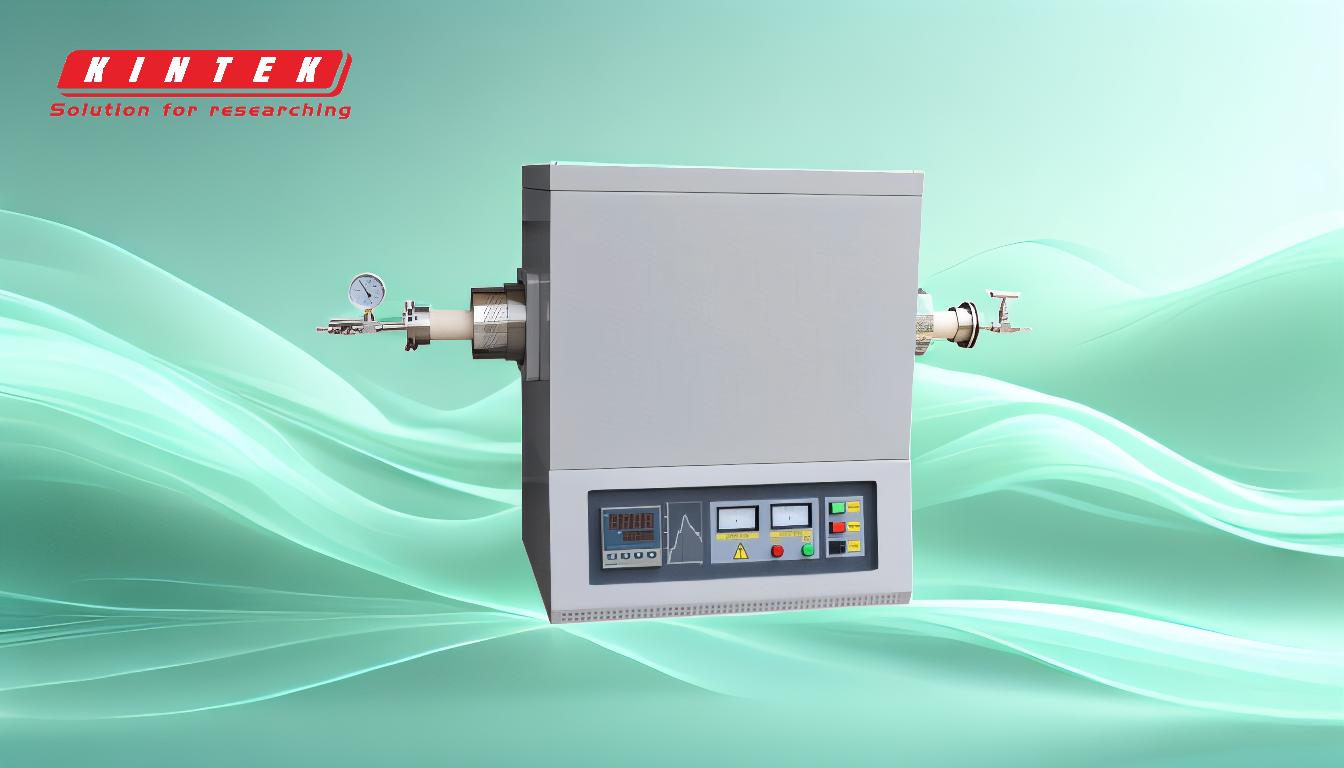
-
Inert Conditions:
- The VAR process is conducted under inert conditions, typically in a vacuum or an inert gas atmosphere. This prevents oxidation and contamination from atmospheric gases, ensuring the purity of the final product.
-
Consumable Electrode:
- A consumable electrode with a predefined composition is used in the VAR process. This electrode is made from the material that needs to be refined, ensuring that the final ingot has the desired chemical composition.
-
Direct Current Electric Arc:
- The remelting process is driven by a direct current electric arc. This arc generates the high temperatures necessary to melt the electrode, allowing for the refining of the material.
-
Water-Cooled Copper Crucible:
- The process takes place in a water-cooled copper crucible. The cooling system helps to control the temperature and ensures the solidification of the ingot from the bottom upwards, promoting a uniform structure.
-
Arc Zone Refining:
- The refining occurs in the arc zone between the electrode tip and the molten metal pool. This zone is where impurities are removed, and the material is homogenized, leading to improved mechanical properties.
-
Controlled Solidification:
- The ingot solidifies in a controlled manner from the bottom upwards. This controlled solidification process helps to minimize defects such as segregation and porosity, resulting in a high-quality final product.
-
Enhanced Purity and Uniformity:
- The VAR process significantly enhances the purity and uniformity of the material. By removing impurities and ensuring a consistent composition, the process produces materials with superior mechanical properties and performance characteristics.
-
Applications:
- The VAR process is widely used in industries that require high-performance materials, such as aerospace, medical, and energy sectors. It is particularly valuable for producing superalloys, titanium alloys, and other advanced materials that demand exceptional purity and strength.
By understanding these key points, one can appreciate the sophistication and effectiveness of the VAR process in producing high-quality materials for demanding applications.
Summary Table:
Key Aspect | Description |
---|---|
Inert Conditions | Conducted under vacuum or inert gas to prevent contamination. |
Consumable Electrode | Made from the material to be refined for precise chemical composition. |
Direct Current Electric Arc | Generates high heat to melt the electrode for refining. |
Water-Cooled Crucible | Ensures controlled solidification from the bottom up for uniform structure. |
Arc Zone Refining | Removes impurities and homogenizes the material for improved properties. |
Controlled Solidification | Minimizes defects like segregation and porosity for high-quality output. |
Enhanced Purity & Uniformity | Produces materials with superior mechanical properties and consistency. |
Applications | Used in aerospace, medical, and energy sectors for advanced materials. |
Interested in high-quality metal refining? Contact us today to learn more about the VAR process!