Chemical Vapor Deposition (CVD) is a process used to produce high-purity, high-performance solid materials, typically under vacuum conditions. Unlike short path vacuum distillation, which is primarily used for separating and purifying compounds, CVD involves the deposition of a material from a vapor phase onto a substrate. The process is widely used in the semiconductor industry, coatings, and the production of thin films. CVD operates by introducing reactive gases into a chamber, where they react or decompose on a heated substrate to form a solid deposit. This method is particularly useful for creating materials with precise properties, such as graphene, silicon carbide, and diamond-like carbon films.
Key Points Explained:
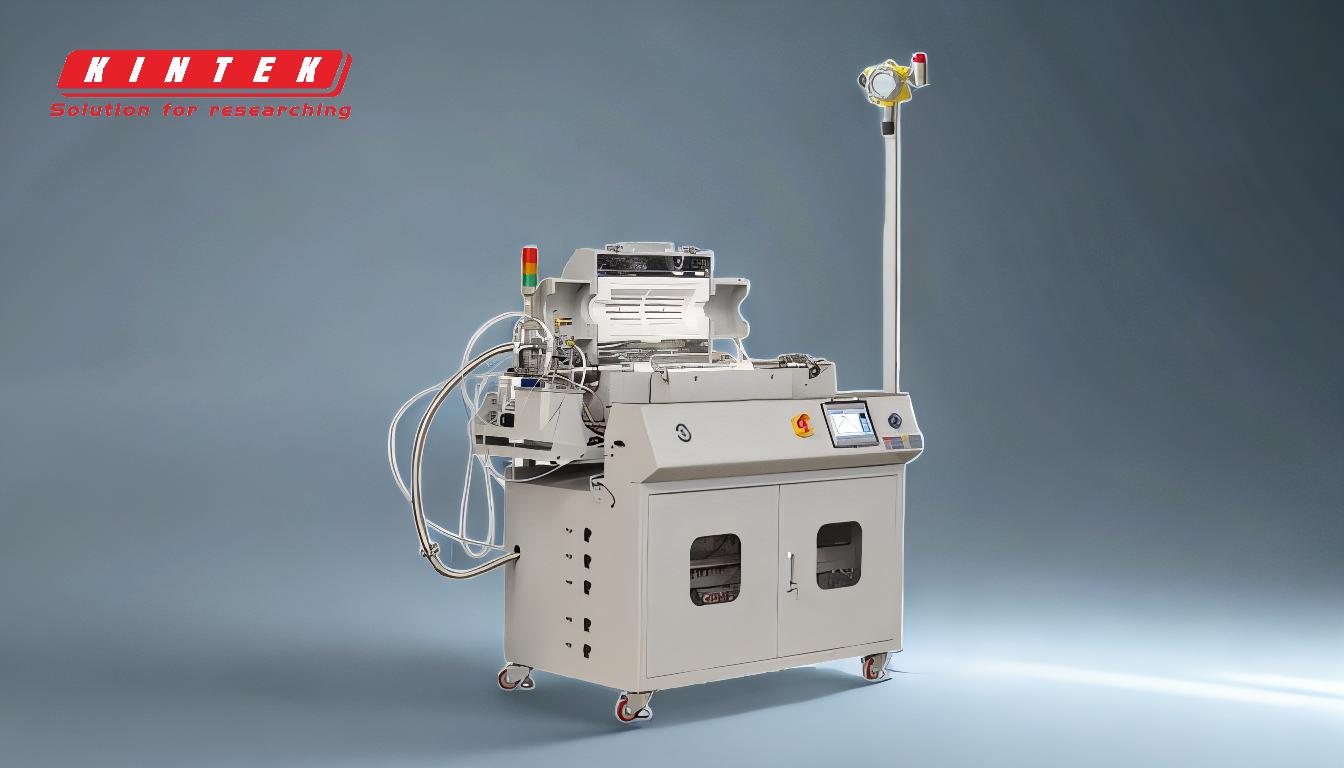
-
Definition and Purpose of CVD:
- CVD is a process where gaseous reactants are introduced into a chamber and react on a heated substrate to form a solid material. This is distinct from short path vacuum distillation, which focuses on separating and purifying compounds. CVD is primarily used for creating high-purity materials and thin films.
-
Key Components of CVD:
- Reactive Gases: Precursor gases are introduced into the chamber, which react or decompose to form the desired material.
- Substrate: The surface on which the material is deposited. The substrate is typically heated to facilitate the reaction.
- Vacuum Environment: Like short path distillation, CVD often operates under vacuum to control pressure and reduce contamination.
-
Types of CVD Processes:
- Atmospheric Pressure CVD (APCVD): Operates at atmospheric pressure, suitable for large-scale production.
- Low-Pressure CVD (LPCVD): Operates under reduced pressure, providing better uniformity and control.
- Plasma-Enhanced CVD (PECVD): Uses plasma to enhance the reaction, allowing for lower temperatures and faster deposition rates.
-
Applications of CVD:
- Semiconductors: CVD is used to deposit silicon, silicon dioxide, and other materials in semiconductor manufacturing.
- Coatings: CVD is used to create protective and functional coatings, such as anti-reflective coatings and wear-resistant layers.
- Thin Films: CVD is essential for producing thin films used in solar cells, LEDs, and optical devices.
-
Advantages of CVD:
- High Purity: CVD can produce materials with extremely high purity, essential for applications like semiconductors.
- Precision: The process allows for precise control over the thickness and composition of the deposited material.
- Versatility: CVD can be used to deposit a wide range of materials, including metals, ceramics, and polymers.
-
Comparison with Short Path Distillation:
- While short path vacuum distillation is used for separating and purifying compounds, CVD is focused on material deposition and synthesis. Both processes operate under vacuum conditions, but their applications and outcomes are fundamentally different.
-
Challenges in CVD:
- Cost: CVD equipment and precursor gases can be expensive.
- Complexity: The process requires precise control over temperature, pressure, and gas flow rates.
- Scalability: Some CVD processes are difficult to scale up for industrial production.
In summary, CVD is a versatile and precise method for depositing high-quality materials, widely used in industries requiring high-performance coatings and thin films. Unlike short path vacuum distillation, which is focused on purification, CVD is about material synthesis and deposition, making it essential in advanced manufacturing and technology sectors.
Summary Table:
Aspect | Details |
---|---|
Types of CVD | Atmospheric Pressure CVD (APCVD), Low-Pressure CVD (LPCVD), Plasma-Enhanced CVD (PECVD) |
Applications | Semiconductors, coatings, thin films (solar cells, LEDs, optical devices) |
Key Advantages | High purity, precision, versatility |
Challenges | High cost, process complexity, scalability issues |
Interested in learning how CVD can benefit your industry? Contact our experts today for more information!