When selecting a brazing rod for aluminum, it is essential to consider the compatibility of the brazing material with the aluminum base material. The brazing rod should have a melting point lower than that of the aluminum to ensure proper bonding without melting the base material. Additionally, the chemical composition of the brazing material should closely match that of the aluminum to ensure good corrosion resistance and chemical stability. The brazing material should also have a small difference between its solidus and liquidus temperatures to facilitate precise temperature control during the brazing process.
Key Points Explained:
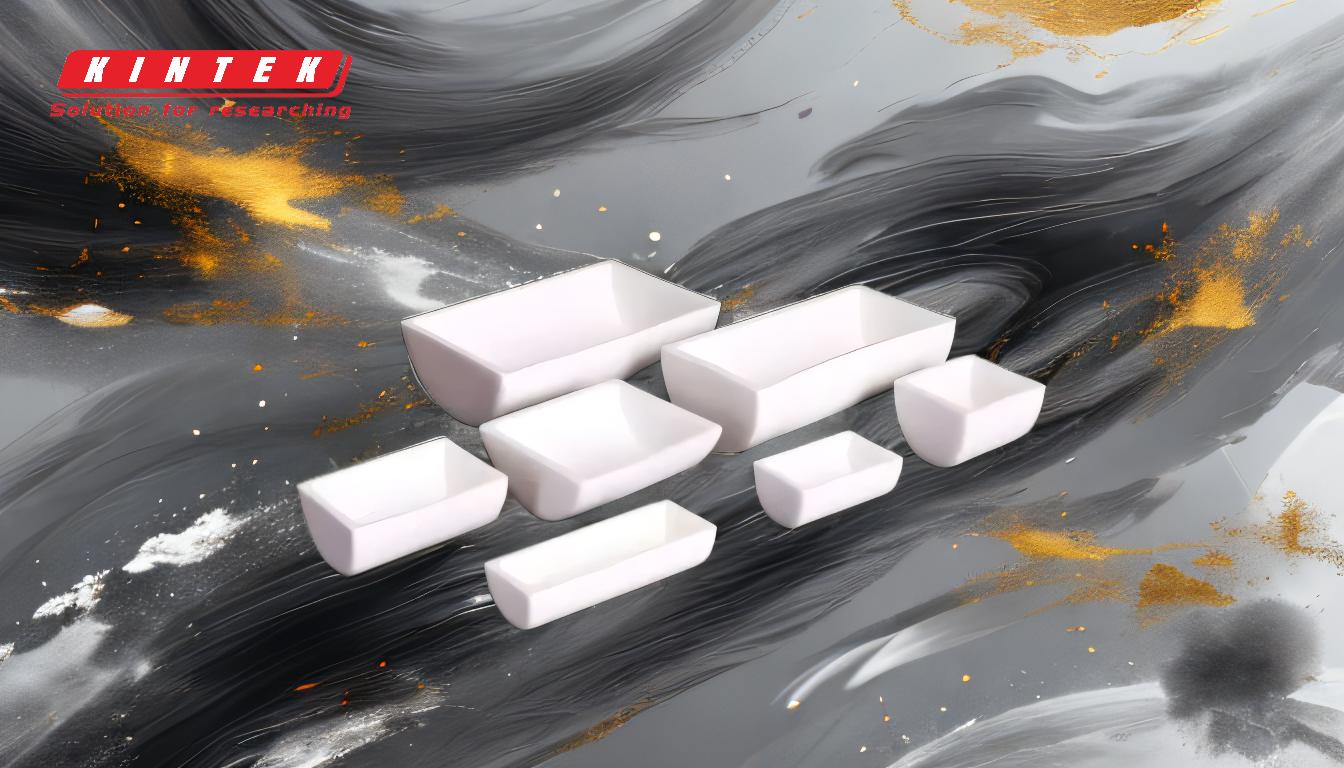
-
Compatibility with Aluminum Base Material:
- The brazing rod must be compatible with the aluminum base material. This means that the chemical composition of the brazing material should be as close as possible to that of the aluminum to ensure a strong bond and good corrosion resistance.
-
Melting Point Considerations:
- The melting point of the brazing rod should be at least 30°C lower than the solidus temperature of the aluminum base material. This ensures that the brazing material melts and flows properly without melting the base material, which could compromise the structural integrity of the joint.
-
Temperature Control and Uniformity:
- A smaller temperature difference between the solidus and liquidus temperatures of the brazing material requires higher precision in furnace temperature control and uniformity. This is crucial to achieve a consistent and high-quality brazed joint.
-
Chemical Stability:
- At the brazing temperature, the brazing material should exhibit high chemical stability, including low oxidation properties and low vapor pressure. This ensures that the brazing material does not degrade or react adversely with the aluminum base material during the brazing process.
-
Corrosion Resistance:
- The main components of the brazing material should be as close as possible to those of the aluminum base material in the periodic table. This similarity in chemical composition helps ensure that the brazed seams have good corrosion resistance, which is particularly important in environments where the joint may be exposed to corrosive elements.
By carefully considering these factors, you can select the appropriate brazing rod for aluminum that will result in a strong, durable, and corrosion-resistant joint.
Summary Table:
Key Factor | Description |
---|---|
Compatibility | The brazing rod's chemical composition should closely match the aluminum base material. |
Melting Point | Must be at least 30°C lower than the aluminum's solidus temperature. |
Temperature Control | Smaller solidus-liquidus gap ensures precise temperature control. |
Chemical Stability | High stability, low oxidation, and low vapor pressure at brazing temperatures. |
Corrosion Resistance | Similar chemical composition to aluminum for durable, corrosion-resistant seams. |
Need help selecting the perfect brazing rod for your aluminum projects? Contact our experts today for personalized advice!