Furnace tubes are critical components in high-temperature applications, and their material selection depends on factors such as maximum operating temperature, chemical resistance, durability, and transparency. Common materials include ceramic options like mullite, recrystallized alumina (RCA), and quartz glass, as well as metals such as stainless steel and Inconel. Each material has specific advantages, such as quartz being cost-effective and transparent but less durable, alumina offering higher temperature resistance, and superalloys like Inconel being suitable for extreme conditions. The choice of material ensures the tube can withstand the required thermal and chemical environment while maintaining performance and longevity.
Key Points Explained:
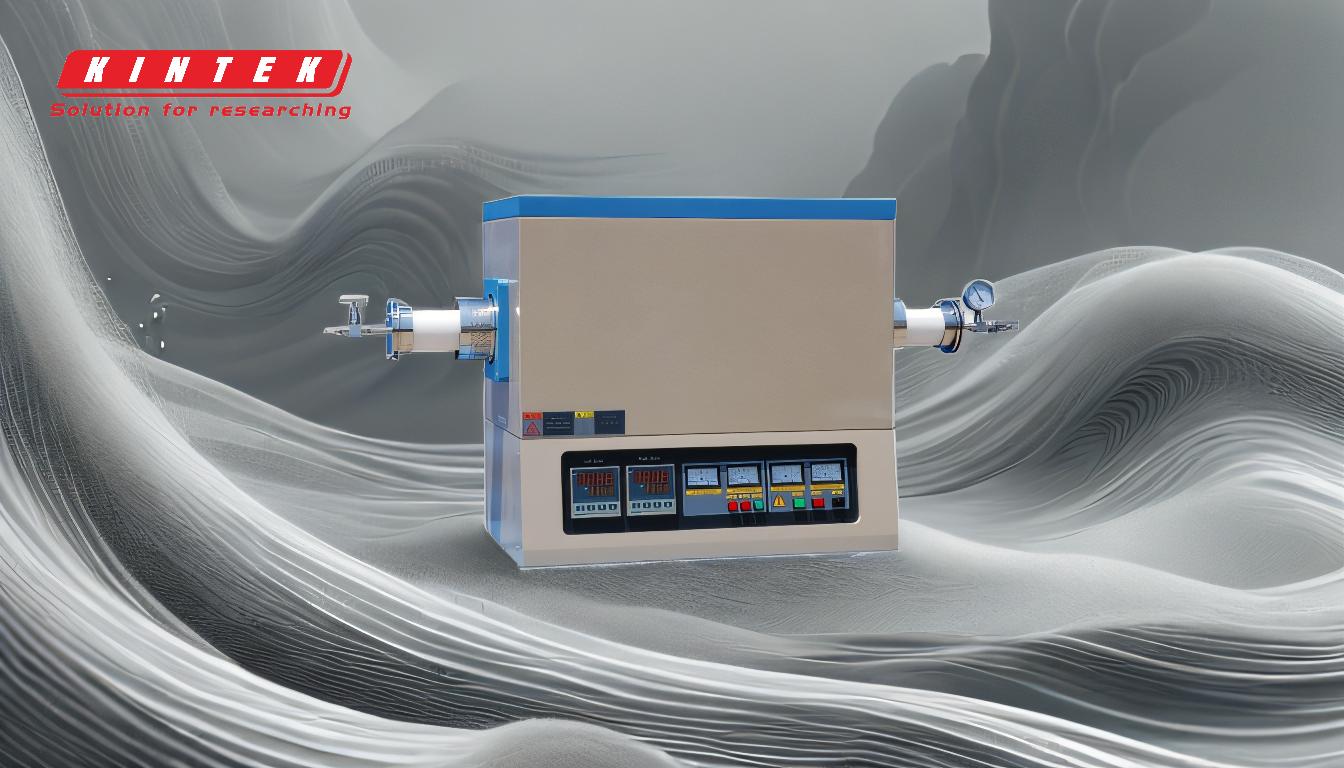
-
Materials Used for Furnace Tubes:
- Furnace tubes are typically made from high-temperature-resistant ceramic or metal materials. These materials are chosen for their thermal insulation properties and chemical stability, ensuring they can operate effectively in demanding environments.
-
Ceramic Materials:
- Mullite and Recrystallized Alumina (RCA): These ceramic materials are highly durable and can withstand high temperatures, making them ideal for applications requiring long-term stability and resistance to thermal stress.
- Alumina Tubes: These are capable of handling temperatures up to 1800°C, making them suitable for high-temperature processes. They are more durable than quartz but lack transparency.
- Quartz Glass: Quartz tubes are cost-effective, transparent, and suitable for temperatures up to 1200°C. However, they are less durable and cannot withstand as many heat-cool cycles as other materials.
-
Metal Materials:
- Stainless Steel: Often used for the outer structure of tube furnaces due to its durability and long-lasting performance. Stainless steel provides a robust framework but may not be suitable for the highest temperature applications.
- Inconel: A superalloy recommended for extreme temperatures, such as those found in jet and rocket engines. Inconel tubes are custom options designed to handle the most demanding thermal and chemical conditions.
-
Specialized Materials:
- Fused Quartz and Pyrex: These materials are commonly used for their transparency and thermal resistance. Fused quartz is suitable for high-temperature applications, while Pyrex is often used for lower-temperature processes.
- Tungsten or Molybdenum Tubes: These materials are used for handling corrosive materials, providing exceptional resistance to chemical reactions and high temperatures.
-
Temperature-Specific Materials:
- Quartz Tubes: Best for applications up to 1200°C, offering transparency and cost-effectiveness but limited durability.
- Alumina Tubes: Suitable for temperatures up to 1800°C, providing greater durability and longevity compared to quartz.
- Superalloy Tubes (e.g., Inconel): Designed for extreme temperatures and harsh environments, making them ideal for specialized applications like aerospace.
-
Considerations for Material Selection:
- Maximum Operating Temperature: The material must withstand the highest temperature required for the application.
- Chemical Resistance: The tube material should resist reactions with sample materials to ensure process integrity.
- Durability and Longevity: Materials like alumina and superalloys offer longer lifespans and better performance under repeated thermal cycling.
- Transparency: For applications requiring visibility, quartz and fused quartz are preferred, while alumina and metals are opaque.
By carefully evaluating these factors, purchasers can select the most appropriate furnace tube material for their specific application, ensuring optimal performance and reliability.
Summary Table:
Material | Max Temp (°C) | Key Features | Best Use Cases |
---|---|---|---|
Quartz Glass | 1200 | Cost-effective, transparent, less durable | Low to medium temp applications |
Alumina Tubes | 1800 | Durable, high temp resistance, opaque | High-temp processes |
Mullite/RCA | 1600-1800 | Durable, thermal stress resistance | Long-term stability applications |
Stainless Steel | 1000-1200 | Durable, robust framework | Outer structure of tube furnaces |
Inconel | 1200+ | Extreme temp resistance, custom options | Aerospace, extreme environments |
Fused Quartz | 1200 | Transparent, thermal resistance | High-temp transparent applications |
Tungsten/Molybdenum | 2000+ | Corrosion resistance, high temp | Handling corrosive materials |
Need help selecting the right furnace tube material? Contact our experts today for personalized advice!