Evaporation techniques are widely used in thin film deposition processes, where materials are heated to their vaporization point in a vacuum environment, allowing them to condense onto a substrate and form a thin film. The materials used in these techniques are diverse and can be categorized into pure metals, compounds, and other specialized materials. These materials are selected based on their properties, such as melting point, vapor pressure, and compatibility with the substrate. Common examples include gold, silver, titanium, silicon dioxide, and tungsten, as well as more complex compounds like antimonides, arsenides, and oxides. The choice of material depends on the specific application, desired film properties, and the evaporation technique employed.
Key Points Explained:
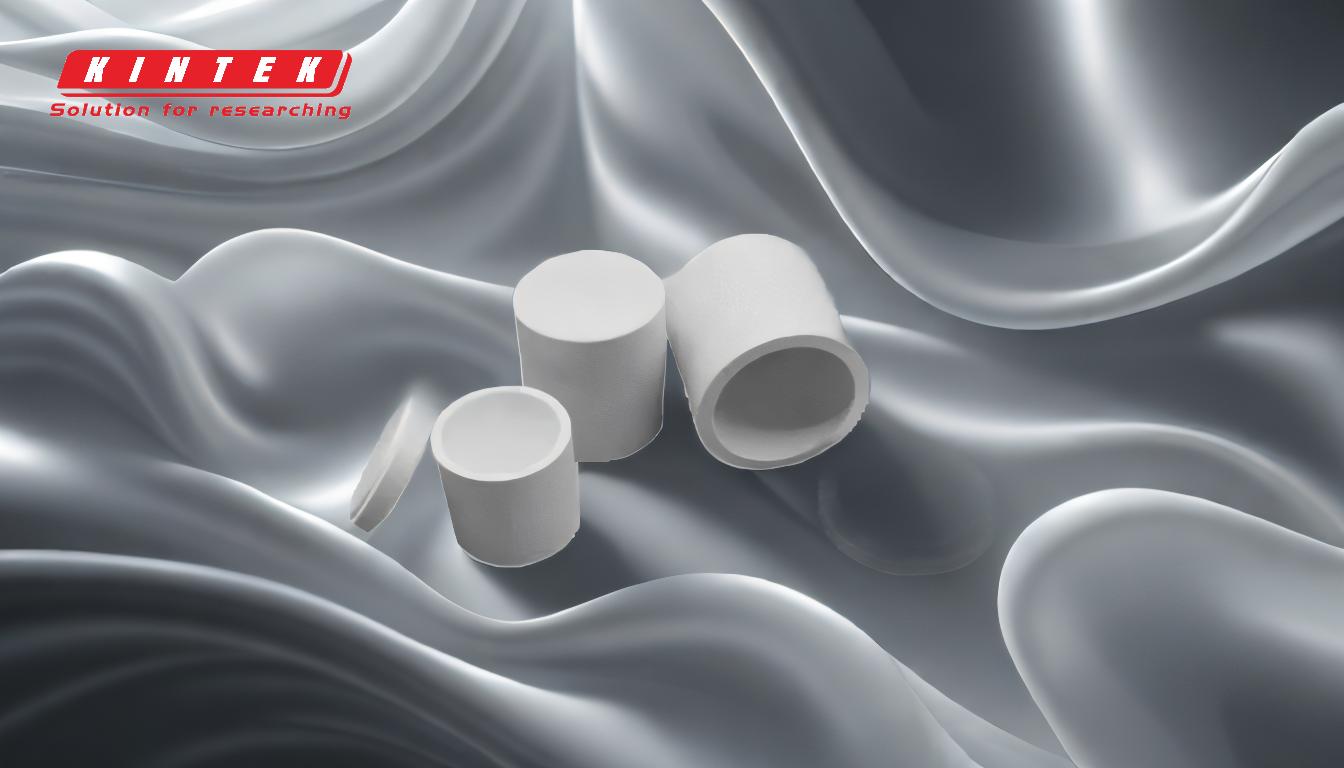
-
Categories of Evaporation Materials:
-
Pure Metals: These are elemental metals used for their specific properties, such as conductivity, reflectivity, or durability. Examples include:
- Gold (Au): Used for its excellent electrical conductivity and resistance to corrosion.
- Silver (Ag): Known for high reflectivity and thermal conductivity.
- Titanium (Ti): Often used as an adhesion layer due to its strong bonding properties.
- Tungsten (W): Chosen for its high melting point and durability.
- Copper (Cu): Commonly used in electrical applications due to its high conductivity.
-
Compounds: These include a variety of chemical compounds tailored for specific functionalities. Examples include:
- Oxides: Silicon dioxide (SiO₂) is widely used for its insulating properties.
- Nitrides: Titanium nitride (TiN) is used for its hardness and wear resistance.
- Carbides: Silicon carbide (SiC) is valued for its thermal and electrical conductivity.
- Fluorides: Magnesium fluoride (MgF₂) is used in optical coatings for its anti-reflective properties.
- Sulfides, Selenides, and Tellurides: These are often used in semiconductor and optoelectronic applications.
- Antimonides, Arsenides, and Borides: These materials are used in specialized applications, such as infrared detectors and high-temperature coatings.
- Silicides: Used in semiconductor manufacturing for their conductive properties and compatibility with silicon substrates.
-
Pure Metals: These are elemental metals used for their specific properties, such as conductivity, reflectivity, or durability. Examples include:
-
Common Materials in Thermal Evaporation:
- Thermal evaporation is a widely used technique, and the materials commonly used in this process include:
- Gold (Au): For conductive coatings and reflective surfaces.
- Silver (Ag): For mirrors and optical coatings.
- Titanium (Ti): As an adhesion layer or for biocompatible coatings.
- Silicon Dioxide (SiO₂): For insulating layers in microelectronics.
- Tungsten (W): For high-temperature applications and durable coatings.
- Copper (Cu): For electrical interconnects and conductive layers.
- Thermal evaporation is a widely used technique, and the materials commonly used in this process include:
-
Factors Influencing Material Selection:
- Melting Point: Materials with lower melting points are easier to evaporate, but high-melting-point materials like tungsten are used for specialized applications.
- Vapor Pressure: Materials with higher vapor pressures at lower temperatures are preferred for efficient evaporation.
- Compatibility with Substrate: The material must adhere well to the substrate and not react adversely with it.
- Desired Film Properties: The choice of material depends on the required properties of the film, such as conductivity, reflectivity, or hardness.
- Evaporation Technique: Different techniques (e.g., resistive heating, electron beam evaporation) may require specific material properties.
-
Evaporation Techniques and Material Suitability:
- Resistive Heating Evaporation: Suitable for materials with lower melting points, such as gold and silver.
- Electron Beam Evaporation: Ideal for high-melting-point materials like tungsten and oxides.
- Flash Evaporation: Used for materials that decompose at high temperatures, such as certain fluorides.
- Induction Heating Evaporation: Suitable for conductive materials like metals.
- Knudsen Cell Evaporation: Used for precise control of evaporation rates, often for research applications.
-
Applications of Evaporation Materials:
- Microelectronics: Conductive layers (e.g., gold, copper) and insulating layers (e.g., silicon dioxide).
- Optics: Reflective coatings (e.g., silver) and anti-reflective coatings (e.g., magnesium fluoride).
- Semiconductors: Doping layers and conductive paths (e.g., silicides, nitrides).
- Biomedical: Biocompatible coatings (e.g., titanium) for implants.
- High-Temperature Coatings: Materials like tungsten and carbides for durability in extreme conditions.
By understanding the categories of materials, their properties, and the techniques used for evaporation, one can select the appropriate material for specific applications, ensuring optimal performance of the thin films.
Summary Table:
Category | Examples | Properties | Applications |
---|---|---|---|
Pure Metals | Gold (Au), Silver (Ag), Titanium (Ti), Tungsten (W), Copper (Cu) | Conductivity, reflectivity, durability, adhesion | Microelectronics, optics, biomedical coatings |
Compounds | Oxides (SiO₂), Nitrides (TiN), Carbides (SiC), Fluorides (MgF₂) | Insulation, hardness, thermal conductivity, anti-reflective properties | Optical coatings, semiconductors, high-temperature coatings |
Specialized | Antimonides, Arsenides, Borides, Sulfides, Selenides, Tellurides, Silicides | Semiconductor properties, IR detection, high-temperature resistance | Infrared detectors, semiconductor manufacturing |
Need help selecting the right material for your thin film deposition? Contact our experts today!