Vacuum casting is a versatile manufacturing process used to produce high-quality prototypes and small batches of parts with intricate details and excellent surface finishes. The materials used in vacuum casting primarily include silicone molds and various casting resins. Silicone molds are created from a master model, which can be made using 3D printing or CNC machining. These molds are then used to cast parts using polyurethane (PU) resins, which can mimic the properties of a wide range of engineering plastics and even metals. The process is ideal for producing parts with complex geometries, fine details, and high dimensional accuracy.
Key Points Explained:
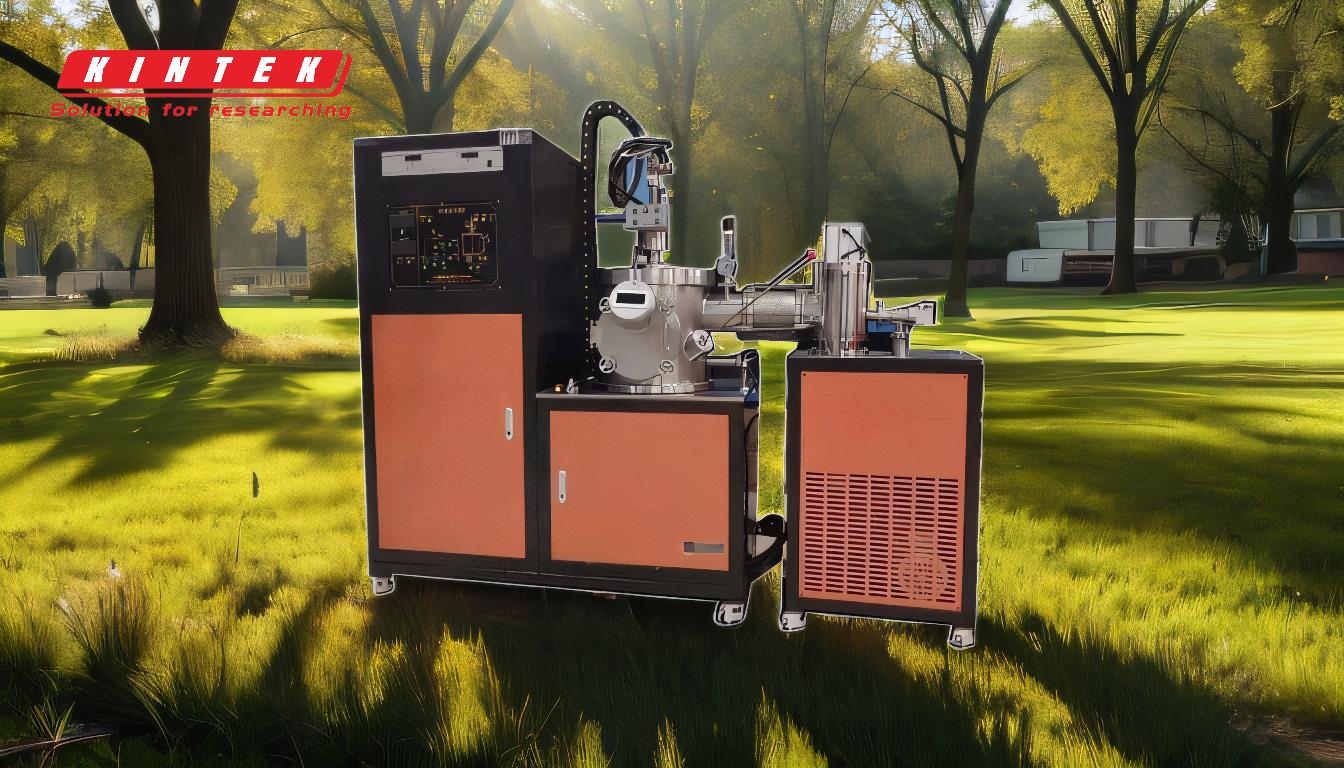
-
Silicone Molds:
- Material: Silicone rubber is the primary material used for creating molds in vacuum casting. It is chosen for its flexibility, durability, and ability to capture fine details.
- Properties: Silicone molds can withstand the high temperatures involved in the casting process and can be reused multiple times, making them cost-effective for small-batch production.
- Creation: The mold is created by pouring liquid silicone around a master model, which is typically made using 3D printing or CNC machining. Once the silicone cures, the master model is removed, leaving a precise negative cavity.
-
Casting Resins:
- Polyurethane (PU) Resins: These are the most commonly used materials in vacuum casting. PU resins are versatile and can be formulated to mimic a wide range of engineering plastics, such as ABS, PP, PC, and even metals.
- Properties: PU resins offer excellent mechanical properties, including high strength, flexibility, and resistance to wear and tear. They can also be colored or transparent, depending on the application.
- Types: There are various types of PU resins available, each tailored to specific requirements, such as high-temperature resistance, flexibility, or transparency.
-
Additives and Fillers:
- Reinforcements: Additives like glass fibers or carbon fibers can be mixed with PU resins to enhance their mechanical properties, such as tensile strength and stiffness.
- Colorants: Pigments or dyes can be added to the resin to achieve the desired color for the final part.
- Surface Finishes: Additives can also be used to modify the surface finish of the cast parts, such as making them glossy, matte, or textured.
-
Master Model Materials:
- 3D Printing: Materials like photopolymers (used in SLA or DLP printing) or thermoplastics (used in FDM or SLS printing) are commonly used to create the master model.
- CNC Machining: Materials such as ABS, PMMA, or aluminum can be used to machine the master model, depending on the required precision and surface finish.
-
Release Agents:
- Purpose: Release agents are applied to the silicone mold before casting to ensure that the cured part can be easily removed without damaging the mold.
- Types: Common release agents include silicone-based sprays or wax-based compounds, which provide a non-stick surface.
-
Post-Processing Materials:
- Paints and Coatings: After casting, parts may be painted or coated to achieve the desired aesthetic or functional properties.
- Polishing Compounds: These are used to enhance the surface finish of the cast parts, making them smoother or more reflective.
-
Environmental Considerations:
- Sustainability: Some PU resins are formulated to be more environmentally friendly, with lower VOC emissions and reduced environmental impact.
- Recycling: Silicone molds can be recycled or reused, and some PU resins can be ground down and reused in other applications.
In summary, vacuum casting relies on a combination of silicone molds and polyurethane resins to produce high-quality parts. The choice of materials can be tailored to meet specific requirements, making vacuum casting a highly flexible and efficient manufacturing process for prototypes and small-batch production.
Summary Table:
Material | Description |
---|---|
Silicone Molds | Flexible, durable, and reusable molds created from master models. |
PU Resins | Versatile resins mimicking engineering plastics and metals for casting. |
Additives/Fillers | Enhance mechanical properties, color, and surface finish of cast parts. |
Master Model | Created via 3D printing or CNC machining using materials like ABS or aluminum. |
Release Agents | Ensure easy removal of cast parts without damaging the mold. |
Post-Processing | Includes paints, coatings, and polishing for improved aesthetics and function. |
Environmental | Focus on sustainability and recyclability of materials. |
Ready to elevate your prototyping process? Contact us today to learn more about vacuum casting solutions!