Rotary evaporators are versatile tools used to separate solvents from various materials by leveraging reduced pressure to lower boiling points, increasing the effective surface area through rotation, and condensing the evaporated solvent. They are suitable for use with a wide range of solvents, including water and alcohol, and can handle organic, inorganic, and polymeric materials. The process is efficient, preventing overheating and violent boiling, and is widely used in industries such as pharmaceuticals, food, and chemical manufacturing. When selecting a rotary vacuum evaporator, factors like size, output, and the inclusion of chillers or vacuum pumps should be considered to match the scale and requirements of the experiments.
Key Points Explained:
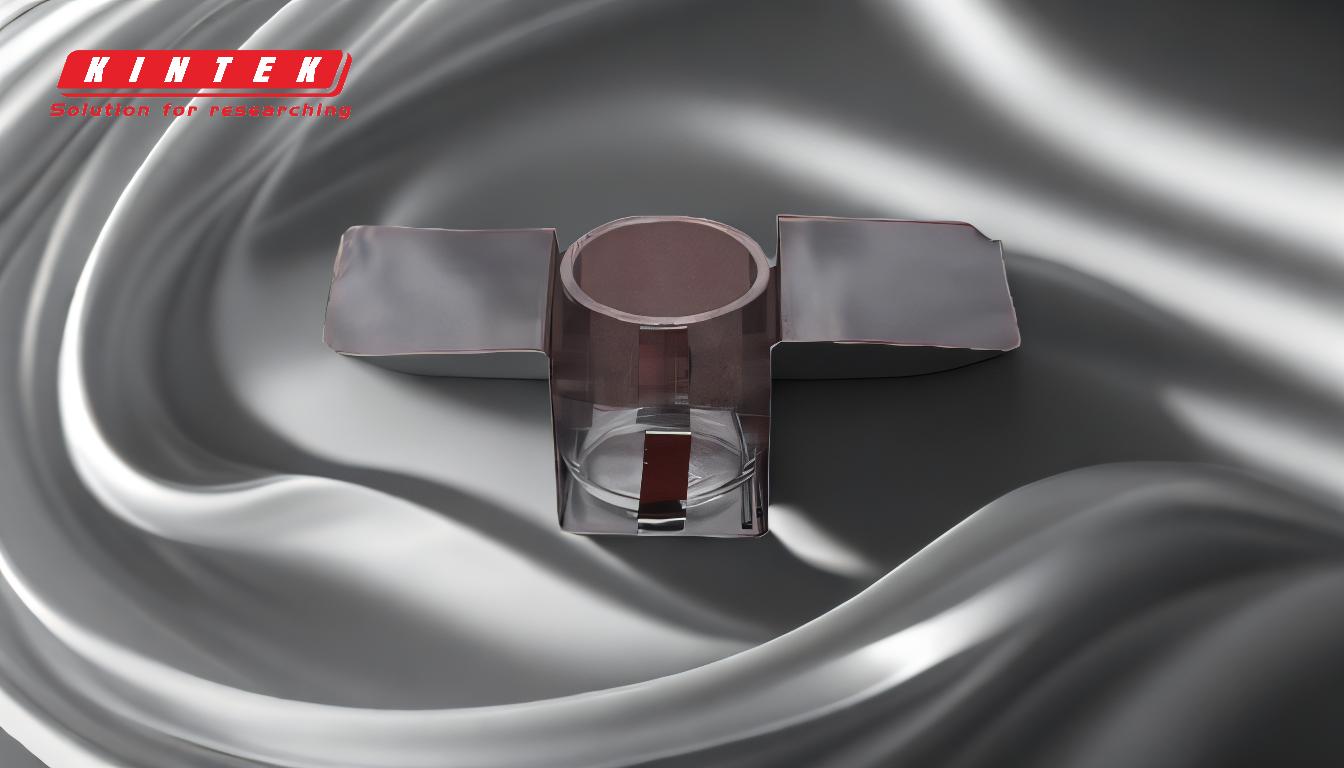
-
Working Principle of Rotary Evaporators:
- Rotary evaporators operate by reducing the pressure inside the system, which lowers the boiling point of the solvent. This allows solvents to evaporate at lower temperatures, minimizing the risk of thermal degradation.
- A vacuum pump is used to create this reduced pressure, enhancing the efficiency of the evaporation process.
- The rotation of the flask increases the surface area of the solvent, promoting faster evaporation.
-
Materials Suitable for Evaporation:
- Rotary evaporators can be used to separate solvents from a wide range of materials, including:
- Organic compounds: Such as alcohols, ethers, and hydrocarbons.
- Inorganic compounds: Including water and other solvents used in chemical synthesis.
- Polymeric materials: Provided the desired compound has a lower boiling point than the solvent and does not form an azeotrope.
- Examples of end products include tinctures, oils, edibles, and vaporized concentrates.
- Rotary evaporators can be used to separate solvents from a wide range of materials, including:
-
Advantages of Using a Rotary Evaporator:
- Efficiency: The process is faster than traditional evaporation methods due to the reduced boiling point under vacuum.
- Safety: Reduced pressure minimizes the risk of violent boiling or "bumping," which can occur with rapid overheating.
- Precision: Built-in PC controllers can regulate the system and detect errors, ensuring consistent results.
-
Applications in Various Industries:
- Pharmaceuticals: For purifying and concentrating active pharmaceutical ingredients (APIs).
- Food and Beverage: To extract flavors, essences, and oils.
- Chemical Manufacturing: For solvent recovery and purification of chemical compounds.
-
Considerations When Choosing a Rotary Evaporator:
- Size and Scale: Select a model that matches the scale of your experiments, ranging from benchtop units (5 L) to industrial models (20-50 L).
- Vacuum System: Ensure the vacuum pump is suitable for the required pressure range.
- Cooling System: Full systems with chillers can replace cold tap water, improving efficiency and consistency.
- Control Features: Look for models with advanced controls for temperature, rotation speed, and vacuum pressure.
-
Practical Use with Common Solvents:
- Rotary evaporators are compatible with both water and alcohol, making them ideal for a wide range of applications.
- The ability to work with these solvents at lower temperatures helps preserve the integrity of heat-sensitive compounds.
By understanding these key points, you can effectively utilize a rotary vacuum evaporator to evaporate solvents from various materials, ensuring efficient and safe separation processes tailored to your specific needs.
Summary Table:
Material Type | Examples |
---|---|
Organic Compounds | Alcohols, ethers, hydrocarbons |
Inorganic Compounds | Water, chemical synthesis solvents |
Polymeric Materials | Provided no azeotrope formation |
Need help selecting the right rotary evaporator for your materials? Contact us today for expert advice!