Hydraulic systems are essential in various industries, from construction to manufacturing, due to their ability to transmit power efficiently. However, hydraulic failure can occur due to several mechanisms, leading to system inefficiency, downtime, and costly repairs. Understanding the root causes of hydraulic failure is crucial for maintenance and prevention. Common mechanisms include contamination, overheating, cavitation, aeration, component wear, and improper maintenance. Each of these factors can compromise the system's performance and lead to catastrophic failure if not addressed promptly. By identifying and mitigating these risks, hydraulic systems can operate reliably and efficiently.
Key Points Explained:
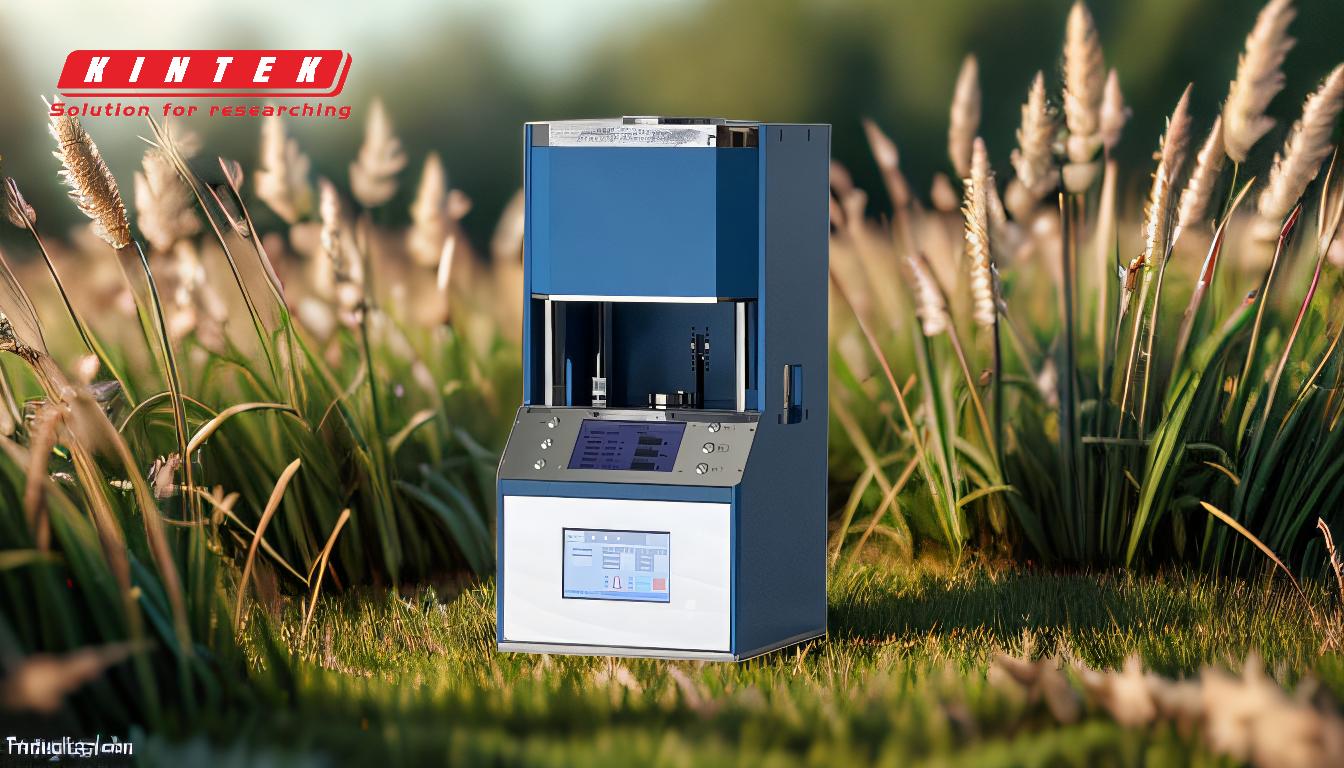
-
Contamination:
- Contamination is one of the most common causes of hydraulic failure. It occurs when foreign particles, such as dirt, metal shavings, or water, enter the hydraulic fluid.
- These contaminants can damage critical components like pumps, valves, and cylinders by causing abrasion, corrosion, or blockages.
- To prevent contamination, it is essential to use high-quality filters, maintain a clean working environment, and regularly check and replace hydraulic fluid.
-
Overheating:
- Overheating can cause hydraulic fluid to break down, losing its lubricating properties and leading to increased friction and wear.
- Common causes of overheating include excessive load, inadequate cooling, or prolonged operation at high temperatures.
- To mitigate overheating, ensure proper system design, use appropriate cooling mechanisms, and monitor temperature levels regularly.
-
Cavitation:
- Cavitation occurs when vapor bubbles form in the hydraulic fluid due to a drop in pressure, typically at the pump inlet. When these bubbles collapse, they create shock waves that can damage pump components.
- Causes of cavitation include restricted fluid flow, clogged filters, or incorrect pump sizing.
- Preventing cavitation involves ensuring adequate fluid supply, maintaining clean filters, and selecting the right pump for the system's requirements.
-
Aeration:
- Aeration happens when air enters the hydraulic fluid, leading to reduced system efficiency and potential damage to components.
- Air can enter the system through leaks, improper fluid levels, or poor system design.
- To prevent aeration, regularly check for leaks, maintain proper fluid levels, and ensure the system is properly designed and sealed.
-
Component Wear:
- Over time, hydraulic components such as seals, hoses, and pistons can wear out due to normal operation or improper maintenance.
- Wear can lead to leaks, reduced efficiency, and eventual system failure.
- Regular maintenance, timely replacement of worn components, and using high-quality parts can help minimize wear and extend the system's lifespan.
-
Improper Maintenance:
- Neglecting regular maintenance is a significant cause of hydraulic failure. This includes failing to replace filters, not checking fluid levels, and ignoring signs of wear or damage.
- Proper maintenance schedules, adherence to manufacturer guidelines, and regular inspections are essential to prevent hydraulic failure.
By understanding these mechanisms and implementing preventive measures, hydraulic systems can operate efficiently and reliably, minimizing the risk of failure and ensuring long-term performance.
Summary Table:
Mechanism | Causes | Prevention Tips |
---|---|---|
Contamination | Dirt, metal shavings, water in hydraulic fluid | Use high-quality filters, maintain a clean environment, and replace fluid regularly. |
Overheating | Excessive load, inadequate cooling, high temperatures | Ensure proper system design, use cooling mechanisms, and monitor temperature. |
Cavitation | Restricted fluid flow, clogged filters, incorrect pump sizing | Ensure adequate fluid supply, maintain clean filters, and select the right pump. |
Aeration | Air leaks, improper fluid levels, poor system design | Check for leaks, maintain proper fluid levels, and ensure proper sealing. |
Component Wear | Normal operation, improper maintenance | Regular maintenance, timely replacement of worn parts, and use high-quality parts. |
Improper Maintenance | Neglecting filters, fluid levels, and signs of wear | Follow maintenance schedules, adhere to guidelines, and conduct regular inspections. |
Ensure your hydraulic systems run smoothly—contact our experts today for tailored solutions!