An induction furnace is a versatile and efficient tool for melting a wide range of metals, including ferrous and non-ferrous metals. It is particularly effective for melting cast iron, steel alloys, and non-ferrous metals such as copper, bronze, brass, and aluminum. The furnace's ability to achieve high temperatures also makes it suitable for processing refractory metals. Key factors influencing the melting process include temperature, pressure, and the presence of impurities or oxidants. Induction furnaces, especially those using IGBT technology, minimize metal loss and contamination due to their efficient design, which includes automatic stirring and the absence of carbon rods. This ensures high-purity metal output and energy efficiency.
Key Points Explained:
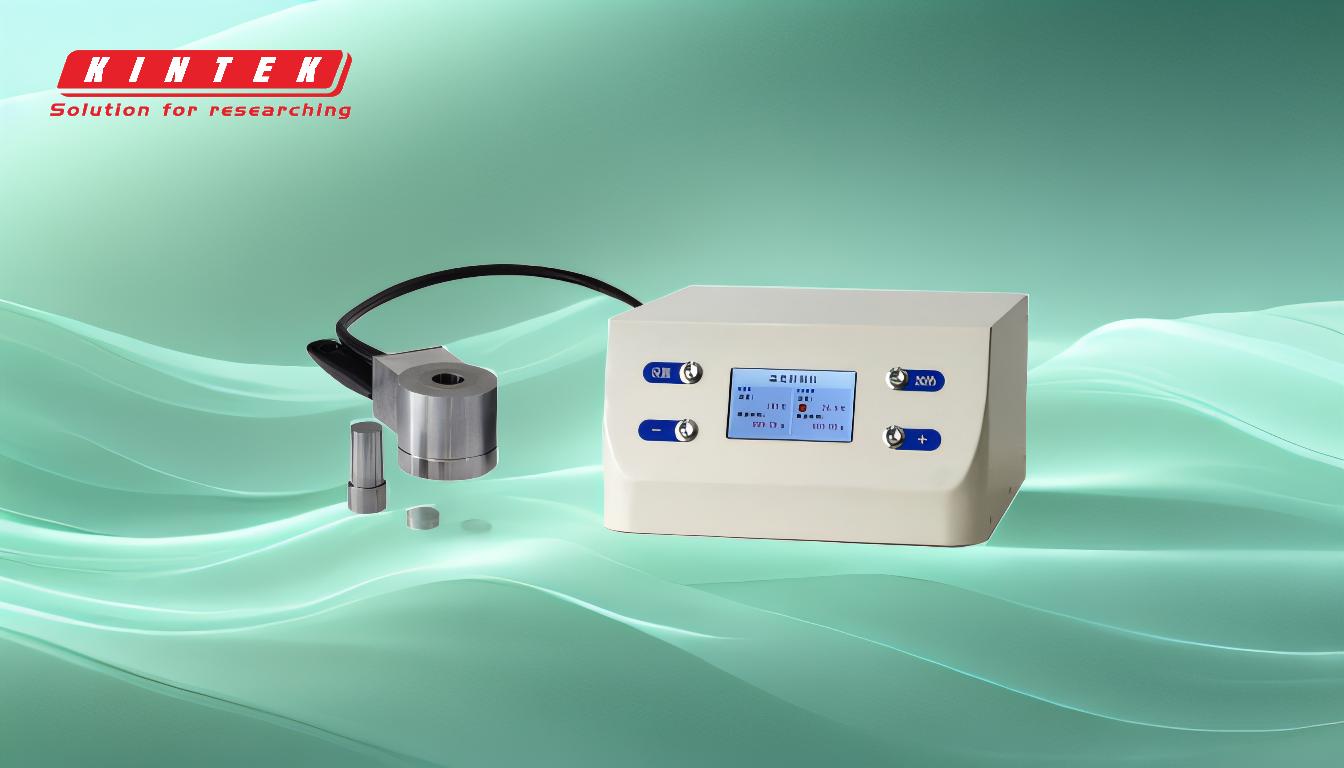
-
Metals Suitable for Melting in an Induction Furnace:
-
Ferrous Metals:
- Cast iron and various steel alloys, including carbon steel, alloy steel, and special steel, can be melted efficiently in an induction furnace.
-
Non-Ferrous Metals:
- Copper, bronze, brass, and aluminum are commonly melted due to their lower melting points and the furnace's ability to maintain precise temperature control.
-
Refractory Metals:
- The high temperatures achievable in an induction furnace make it suitable for processing refractory metals, which require extreme heat to melt.
-
Ferrous Metals:
-
Advantages of Induction Furnaces:
-
Efficiency:
- Induction furnaces, particularly those using IGBT technology, heat metals quickly and efficiently, minimizing heat and metal loss.
-
Purity:
- Automatic stirring ensures uniform heating and prevents contamination, resulting in high-purity metal output.
-
Energy Savings:
- The design of the furnace, including the use of a heavy-gauge hollow copper pipe coil with cold water circulation, ensures long-lasting performance and energy efficiency.
-
Efficiency:
-
Factors Influencing the Melting Process:
-
Temperature:
- The furnace must reach and maintain the specific melting point of the metal being processed.
-
Pressure:
- While typically operated at atmospheric pressure, some processes may require controlled pressure environments.
-
Impurities and Oxidants:
- The presence of impurities or oxidants can affect the quality of the melted metal, but induction furnaces are designed to minimize these effects through efficient heating and stirring.
-
Temperature:
-
Applications of Induction Furnaces:
-
Industrial Use:
- Widely used in foundries and metalworking industries for melting and casting a variety of metals.
-
Specialized Applications:
- Suitable for producing high-quality alloys and specialized metals, including those used in aerospace and electronics industries.
-
Industrial Use:
By understanding these key points, a purchaser can make informed decisions about the suitability of an induction furnace for their specific metal melting needs, ensuring optimal performance and cost-effectiveness.
Summary Table:
Metal Type | Examples |
---|---|
Ferrous Metals | Cast iron, carbon steel, alloy steel, special steel |
Non-Ferrous Metals | Copper, bronze, brass, aluminum |
Refractory Metals | Metals requiring extreme heat (e.g., tungsten, molybdenum) |
Advantages | High efficiency, purity, energy savings, and minimal contamination |
Ready to optimize your metal melting process? Contact us today to find the perfect induction furnace for your needs!