Induction furnaces are highly efficient for melting a wide range of metals due to their ability to generate localized heat through electromagnetic induction. The process minimizes metal loss and contamination, making it ideal for melting both ferrous and non-ferrous metals. The use of an IGBT induction furnace further enhances control and energy efficiency, making it suitable for precise melting applications. Metals commonly melted in induction furnaces include steel, iron, copper, aluminum, gold, and silver, among others. The process is influenced by factors like temperature, pressure, and the presence of impurities, but the furnace's design ensures minimal heat and metal loss.
Key Points Explained:
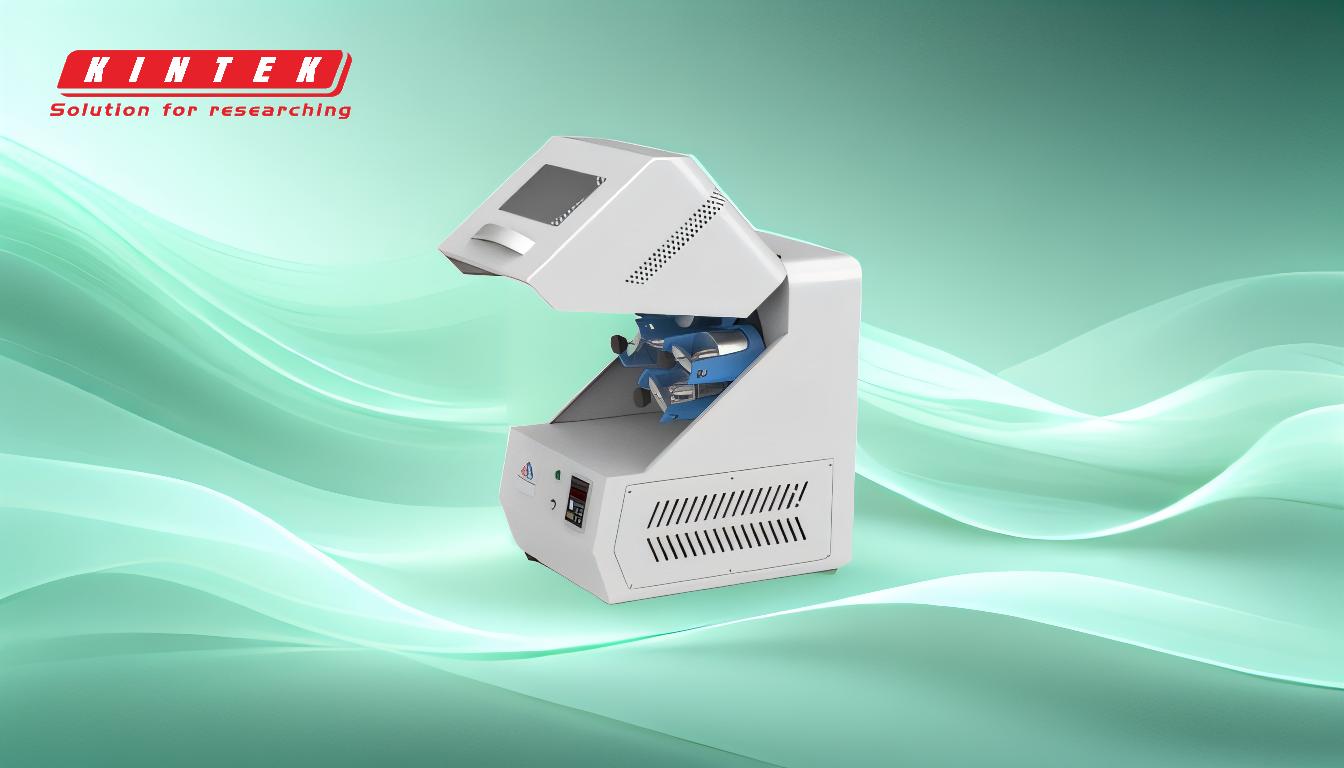
-
Efficiency of Induction Melting:
- Induction furnaces use electromagnetic induction to generate heat directly within the metal, ensuring rapid and efficient heating.
- The hollow copper pipe coil with cold water circulation prevents overheating and extends the furnace's lifespan.
- Automatic stirring ensures uniform melting and purity, eliminating the need for carbon rods that can contaminate the metal.
-
Metals Suitable for Induction Furnaces:
- Ferrous Metals: Steel and iron are commonly melted in induction furnaces due to their high melting points and the furnace's ability to maintain precise temperature control.
- Non-Ferrous Metals: Copper, aluminum, gold, and silver are also melted efficiently, as the process minimizes oxidation and contamination.
- Specialty Alloys: Induction furnaces are ideal for melting alloys that require precise temperature control and minimal impurities.
-
Advantages of IGBT Induction Furnaces:
- IGBT induction furnaces offer superior energy efficiency and precise control over the melting process.
- They are capable of handling a wide range of frequencies, making them versatile for different metals and applications.
- The technology reduces power consumption and operational costs, making it a preferred choice for industrial melting.
-
Factors Influencing the Melting Process:
- Temperature: The furnace must reach and maintain the specific melting point of the metal being processed.
- Pressure: While most induction melting occurs at atmospheric pressure, certain applications may require controlled environments.
- Impurities and Slags: The presence of impurities can affect the quality of the melted metal, but induction furnaces minimize this risk through controlled stirring and heating.
- Oxidants: Induction melting reduces exposure to oxidants, preserving the metal's integrity and reducing waste.
-
Applications of Induction Furnaces:
- Foundries: Used for casting and molding metals into desired shapes.
- Recycling: Efficiently melts scrap metal for reuse, reducing waste and conserving resources.
- Jewelry Making: Ideal for melting precious metals like gold and silver with minimal loss.
- Aerospace and Automotive Industries: Used for producing high-quality alloys with precise composition and properties.
In summary, induction furnaces, particularly those utilizing IGBT technology, are versatile and efficient tools for melting a wide range of metals. Their ability to minimize heat and metal loss, coupled with precise temperature control, makes them indispensable in industries requiring high-quality metal processing.
Summary Table:
Metal Type | Examples | Key Benefits |
---|---|---|
Ferrous Metals | Steel, Iron | High melting points, precise temperature control |
Non-Ferrous Metals | Copper, Aluminum, Gold, Silver | Minimized oxidation and contamination, ideal for precious metals |
Specialty Alloys | Custom alloys | Precise temperature control, minimal impurities, suitable for high-quality alloys |
Ready to melt metals efficiently? Contact us today to find the perfect induction furnace for your needs!