Thin film deposition is a critical process in various industries, including electronics, optics, and coatings. The methods used to deposit thin films can be broadly categorized into Physical Vapor Deposition (PVD) and Chemical Vapor Deposition (CVD), each encompassing several specific techniques. PVD includes methods like evaporation, sputtering, and pulsed laser deposition, while CVD involves chemical reactions to form thin films, with variants like plasma-enhanced CVD and atomic layer deposition. Additionally, other methods such as spray pyrolysis, sol-gel, and electroplating are also used depending on the application requirements. These techniques vary in complexity, cost, and suitability for different materials and substrates.
Key Points Explained:
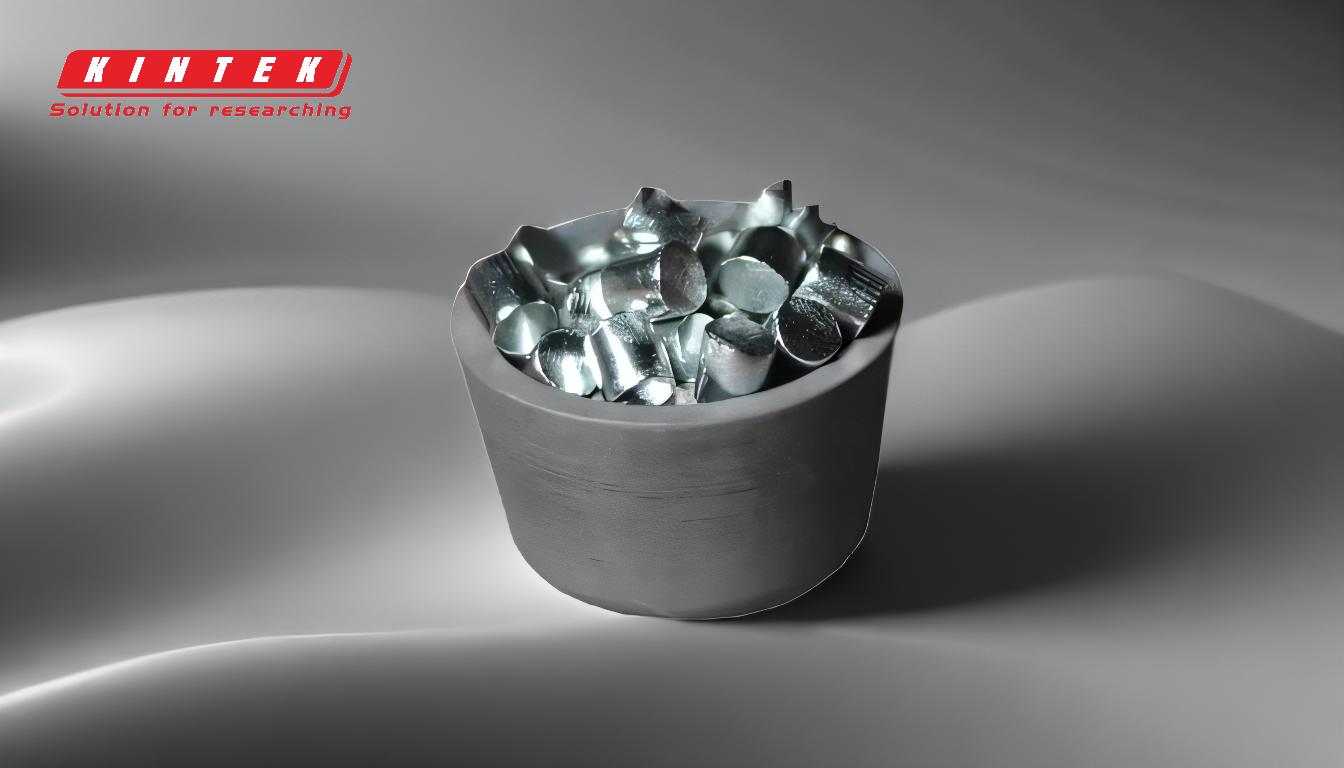
-
Physical Vapor Deposition (PVD):
- Definition: PVD involves the physical transfer of material from a source to a substrate, typically in a vacuum environment.
-
Common Techniques:
- Evaporation: Material is heated to its vaporization point, and the vapor condenses on the substrate. Techniques include thermal evaporation and electron beam evaporation.
- Sputtering: A target material is bombarded with ions, causing atoms to be ejected and deposited on the substrate. Methods include magnetron sputtering and ion beam sputtering.
- Pulsed Laser Deposition (PLD): A high-energy laser ablates material from a target, which then deposits onto the substrate.
- Applications: PVD is widely used for depositing metals, alloys, and ceramics in applications like semiconductor devices, optical coatings, and wear-resistant coatings.
-
Chemical Vapor Deposition (CVD):
- Definition: CVD involves chemical reactions of gaseous precursors to form a solid thin film on the substrate.
-
Common Techniques:
- Thermal CVD: Precursors react at elevated temperatures to deposit the film.
- Plasma-Enhanced CVD (PECVD): Plasma is used to lower the reaction temperature, making it suitable for temperature-sensitive substrates.
- Atomic Layer Deposition (ALD): Films are deposited one atomic layer at a time, allowing for precise control over thickness and composition.
- Applications: CVD is used for depositing high-quality films in applications such as microelectronics, solar cells, and protective coatings.
-
Other Deposition Methods:
- Spray Pyrolysis: A solution containing the desired material is sprayed onto a heated substrate, where it decomposes to form a thin film. This method is cost-effective and suitable for large-area coatings.
- Sol-Gel: A colloidal solution (sol) is converted into a gel, which is then dried and sintered to form a thin film. This method is ideal for producing oxide films.
- Electroplating: An electric current is used to reduce metal ions in a solution, depositing them onto a conductive substrate. This method is commonly used for decorative and functional coatings.
-
Factors Influencing Method Selection:
- Material Properties: Different materials require specific deposition techniques. For example, metals are often deposited using PVD, while oxides and nitrides are commonly deposited using CVD.
- Substrate Compatibility: The substrate material and its thermal stability influence the choice of deposition method. For instance, temperature-sensitive substrates may require low-temperature techniques like PECVD or ALD.
- Film Quality Requirements: Applications requiring high-purity films with precise thickness control, such as in semiconductors, often use ALD or CVD.
- Cost and Scalability: Techniques like spray pyrolysis and sol-gel are cost-effective for large-area coatings, while PVD and CVD are more suitable for high-precision applications.
-
Emerging Trends:
- Hybrid Techniques: Combining PVD and CVD methods to leverage the advantages of both, such as improved adhesion and film quality.
- Nanostructured Films: Advanced techniques like ALD and PLD are being used to deposit nanostructured films with unique properties for applications in energy storage and catalysis.
- Green Deposition Methods: Development of environmentally friendly deposition techniques, such as using non-toxic precursors in CVD or reducing energy consumption in PVD processes.
In summary, the choice of thin film deposition method depends on the specific requirements of the application, including the material to be deposited, the substrate, and the desired film properties. Understanding the strengths and limitations of each technique is crucial for selecting the most appropriate method for a given application.
Summary Table:
Method | Key Techniques | Applications |
---|---|---|
Physical Vapor Deposition (PVD) | Evaporation, Sputtering, Pulsed Laser Deposition (PLD) | Semiconductor devices, optical coatings, wear-resistant coatings |
Chemical Vapor Deposition (CVD) | Thermal CVD, Plasma-Enhanced CVD (PECVD), Atomic Layer Deposition (ALD) | Microelectronics, solar cells, protective coatings |
Other Methods | Spray Pyrolysis, Sol-Gel, Electroplating | Large-area coatings, oxide films, decorative and functional coatings |
Need help selecting the right thin film deposition method for your application? Contact our experts today!