Physical Vapor Deposition (PVD) is a versatile and widely used thin-film coating technique, but it requires careful handling and adherence to specific guidelines to ensure safety, efficiency, and the quality of the coatings. Missteps in using PVD can lead to equipment damage, safety hazards, or subpar coating results. Below is a detailed explanation of what you should avoid when working with PVD.
Key Points Explained:
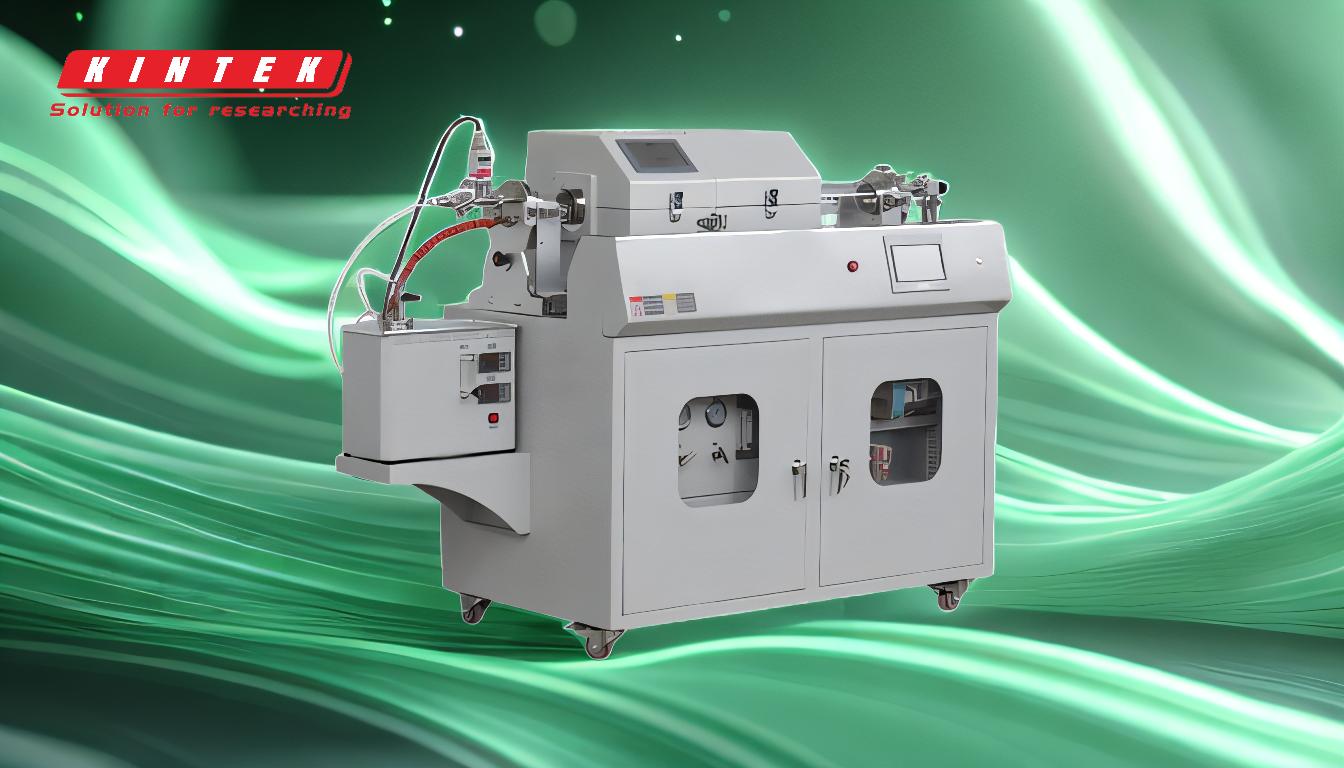
-
Do Not Operate Without Proper Training
- PVD systems are complex and involve high-energy processes such as sputtering or evaporation. Operating the equipment without adequate training can lead to accidents, equipment damage, or inconsistent coating quality.
- Always ensure that operators are trained in both the technical aspects of the process and safety protocols. This includes understanding vacuum systems, power supplies, and the handling of hazardous materials.
-
Avoid Ignoring Vacuum System Requirements
- PVD processes require a high vacuum environment (typically 10^-6 to 10^-3 Torr) to function effectively. Ignoring vacuum system maintenance or failing to achieve the required vacuum levels can result in contamination, poor adhesion, or uneven coatings.
- Regularly check and maintain vacuum pumps, seals, and gauges. Ensure that the chamber is clean and free of leaks before starting the process.
-
Do Not Use Incompatible Materials
- PVD is suitable for a wide range of materials, but not all materials are compatible with the process. For example, materials with low melting points or high vapor pressures may not deposit properly or could damage the equipment.
- Always verify the compatibility of the target material and substrate with the PVD process. Consult material datasheets or conduct preliminary tests if necessary.
-
Avoid Poor Substrate Preparation
- The quality of the coating depends heavily on the condition of the substrate. Skipping or inadequately performing substrate cleaning and surface preparation can lead to poor adhesion, defects, or contamination.
- Thoroughly clean the substrate using appropriate methods (e.g., ultrasonic cleaning, solvent cleaning) and ensure it is free of oils, oxides, or other contaminants before loading it into the chamber.
-
Do Not Overload the Chamber
- Overloading the chamber with too many substrates or improperly arranging them can obstruct the deposition process. This can result in uneven coatings, shadowing effects, or damage to the equipment.
- Follow the manufacturer's guidelines for chamber capacity and substrate arrangement. Use fixtures or holders designed for the specific PVD system.
-
Avoid Incorrect Process Parameters
- PVD processes rely on precise control of parameters such as power, pressure, temperature, and deposition time. Using incorrect settings can lead to poor coating quality, delamination, or excessive stress in the film.
- Calibrate and monitor the equipment regularly. Use process recipes that have been validated for the specific material and application.
-
Do Not Neglect Safety Precautions
- PVD involves high voltages, high temperatures, and potentially hazardous materials (e.g., toxic gases, reactive metals). Ignoring safety precautions can result in serious injuries or equipment damage.
- Always wear appropriate personal protective equipment (PPE), such as gloves, goggles, and lab coats. Ensure proper ventilation and follow guidelines for handling and disposing of hazardous materials.
-
Avoid Skipping Equipment Maintenance
- PVD systems require regular maintenance to function optimally. Neglecting maintenance can lead to equipment failure, reduced coating quality, or safety hazards.
- Establish a maintenance schedule that includes cleaning the chamber, replacing worn components (e.g., targets, filaments), and checking for leaks or other issues.
-
Do Not Use Contaminated Targets
- Targets used in PVD must be clean and free of contaminants. Using contaminated targets can introduce impurities into the coating, affecting its properties and performance.
- Store targets properly and clean them before use. Replace targets that are worn or damaged.
-
Avoid Rushing the Process
- PVD is a precision process that requires time for proper setup, deposition, and cooling. Rushing the process can lead to errors, defects, or equipment damage.
- Allocate sufficient time for each step, including chamber evacuation, deposition, and post-deposition cooling. Follow the recommended process timeline.
By avoiding these common mistakes, you can ensure the safe and effective use of PVD technology, achieving high-quality coatings and maximizing the lifespan of your equipment.
Summary Table:
Mistake | Consequence | Prevention |
---|---|---|
Operating without proper training | Accidents, equipment damage, inconsistent coating quality | Ensure operators are trained in technical and safety protocols. |
Ignoring vacuum system requirements | Contamination, poor adhesion, uneven coatings | Regularly maintain vacuum pumps, seals, and gauges. |
Using incompatible materials | Improper deposition, equipment damage | Verify material compatibility and conduct tests if necessary. |
Poor substrate preparation | Poor adhesion, defects, contamination | Clean substrates thoroughly before loading into the chamber. |
Overloading the chamber | Uneven coatings, shadowing effects, equipment damage | Follow manufacturer guidelines for capacity and arrangement. |
Incorrect process parameters | Poor coating quality, delamination, excessive stress | Calibrate and monitor equipment regularly. Use validated process recipes. |
Neglecting safety precautions | Injuries, equipment damage | Wear PPE, ensure ventilation, and handle hazardous materials safely. |
Skipping equipment maintenance | Equipment failure, reduced coating quality, safety hazards | Establish a regular maintenance schedule. |
Using contaminated targets | Impurities in coatings, reduced performance | Clean and store targets properly. Replace worn or damaged targets. |
Rushing the process | Errors, defects, equipment damage | Allocate sufficient time for each step and follow the recommended timeline. |
Ensure your PVD processes are safe and efficient—contact our experts today for personalized guidance!