When selecting a melting furnace, it’s essential to consider factors such as production requirements, material type, and desired output. The size of the furnace is determined by its melting capacity, measured in kilograms per hour (kg/h), which depends on the furnace's power rating, size, and the material being melted. Additionally, the type of scrap metal and the end product influence the choice of furnace. Foundries should also consider transformer capacity and investment quotas to ensure the furnace aligns with their operational and financial goals.
Key Points Explained:
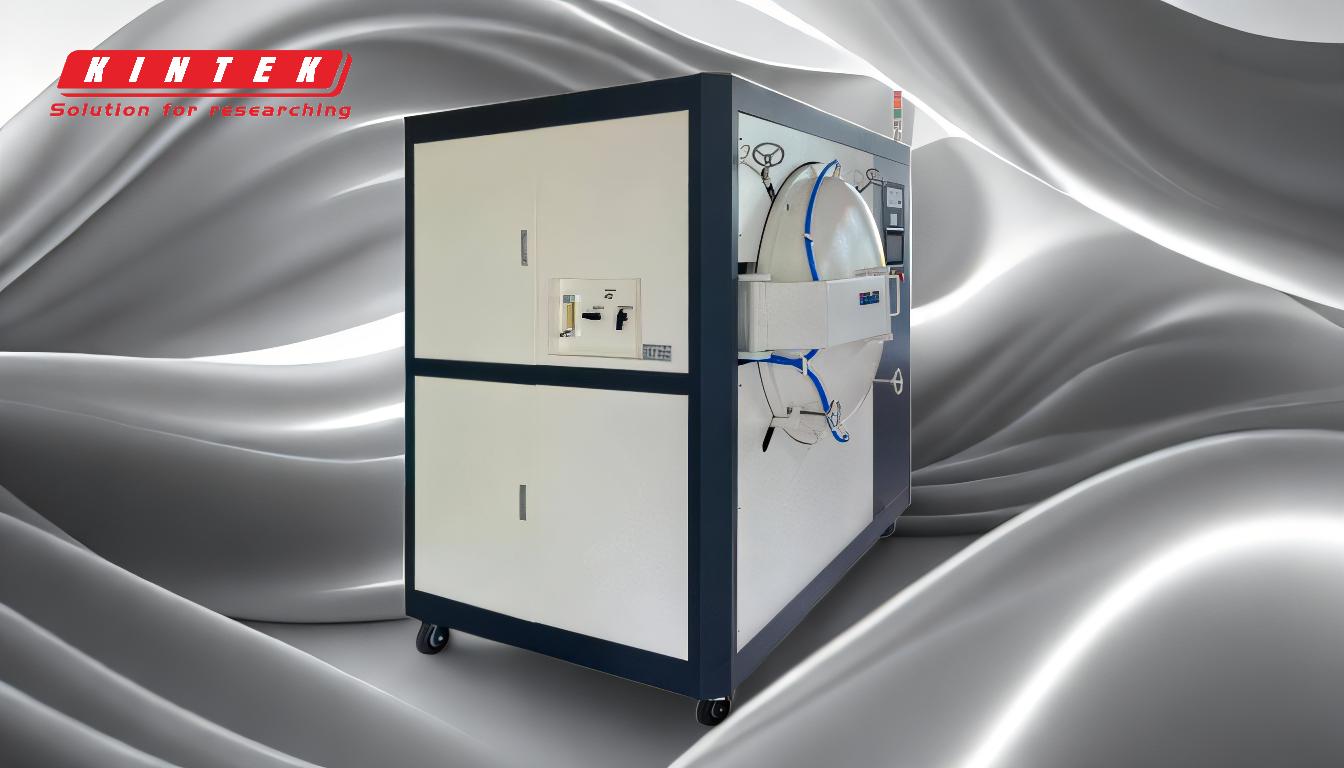
-
Melting Capacity (kg/h):
- The melting capacity of a furnace is a critical factor in determining its size. It is measured in kilograms per hour (kg/h) and indicates how much material the furnace can melt within a specific time frame.
- This capacity depends on:
- Furnace Size: Larger furnaces generally have higher melting capacities.
- Power Rating: Higher power ratings enable faster melting rates.
- Material Type: Different materials have varying melting points and energy requirements, affecting the furnace's efficiency.
- Understanding the melting capacity helps in planning production schedules and ensuring the furnace meets the required productivity levels.
-
Material Type and End Product:
- The type of material being melted (e.g., copper, bronze, brass) plays a significant role in furnace selection. Each material has unique properties, such as melting points and thermal conductivity, which influence the furnace's design and operation.
- The desired end product (e.g., copper rods, ingots, bars, electronic components) also dictates the type of furnace needed. For example, a furnace designed for producing copper rods may differ from one used for electronic components due to variations in temperature control and melting precision.
-
Production Requirements:
- Foundries must align the furnace size with their production needs. This includes:
- Volume of Material: Higher production volumes require furnaces with greater melting capacities.
- Production Schedule: Continuous or batch production processes may necessitate different furnace types and sizes.
- Matching the furnace size to production requirements ensures efficiency and avoids bottlenecks in the manufacturing process.
- Foundries must align the furnace size with their production needs. This includes:
-
Transformer Capacity and Investment Quotas:
- The transformer capacity is a crucial consideration, as it determines the power supply available for the furnace. A furnace with a higher power rating may require a more robust transformer, which could involve additional investment.
- Investment quotas also play a role in furnace selection. Foundries must balance their budget with the need for a furnace that meets their production and operational goals. This includes considering the initial purchase cost, operational expenses, and potential return on investment.
By carefully evaluating these factors, foundries can select a melting furnace that aligns with their specific needs, ensuring optimal performance and efficiency in their operations.
Summary Table:
Factor | Details |
---|---|
Melting Capacity (kg/h) | Determined by furnace size, power rating, and material type. |
Material Type | Influences furnace design and operation (e.g., copper, bronze, brass). |
Production Requirements | Align furnace size with material volume and production schedule. |
Transformer Capacity | Ensure power supply matches furnace power rating. |
Investment Quotas | Balance budget with operational and production goals. |
Need help selecting the right melting furnace? Contact our experts today for personalized guidance!