Brazing aluminum requires careful consideration of various factors to achieve a strong and reliable joint. The process typically involves heating the aluminum to a temperature range of 570°C to 620°C (1058°F to 1148°F), which is just below its melting point. This temperature range ensures that the filler metal melts and flows into the joint without melting the base aluminum. Key factors such as joint design, part cleanliness, fixturing, and filler metal selection play a crucial role in the success of the brazing process. Additionally, using specialized equipment like a rotating furnace can enhance the uniformity of heating and improve the quality of the brazed joint.
Key Points Explained:
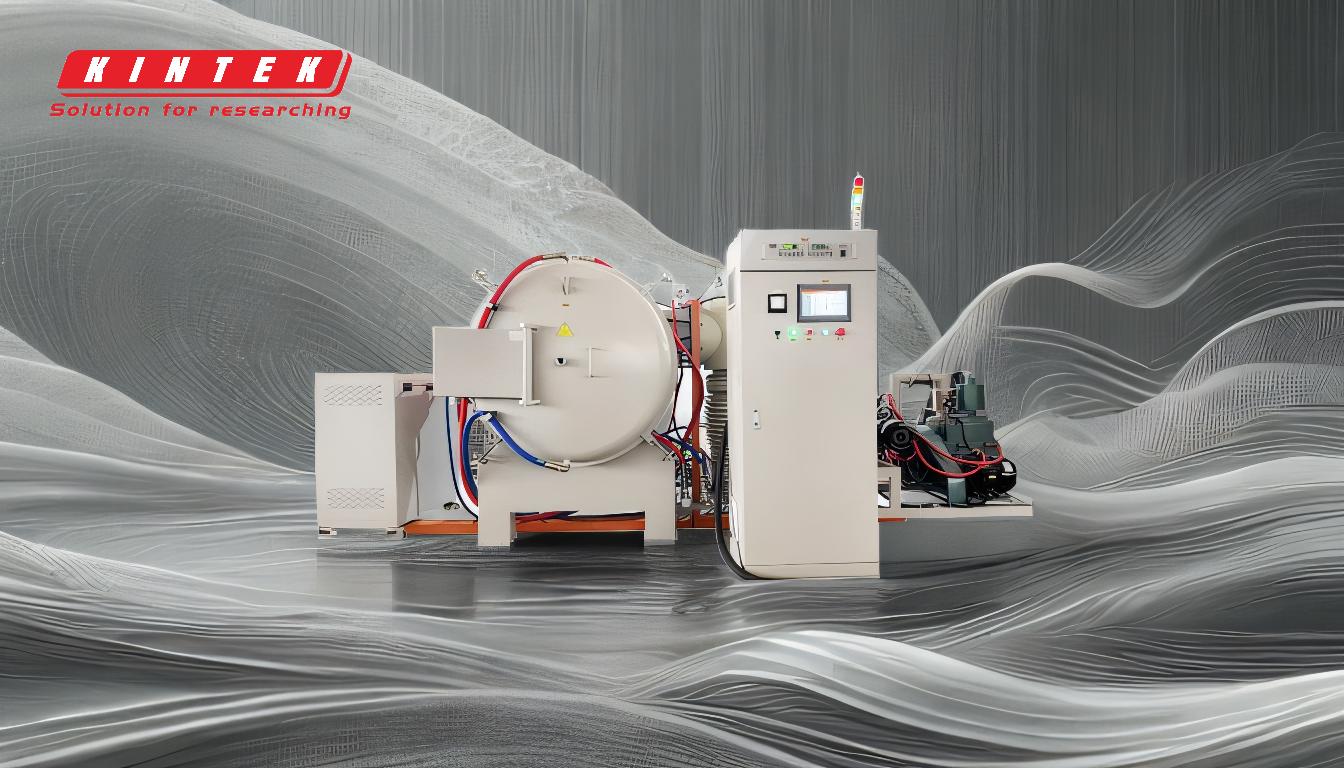
-
Temperature Range for Brazing Aluminum:
- Brazing aluminum typically requires heating the material to a temperature range of 570°C to 620°C (1058°F to 1148°F). This range is critical because it is high enough to melt the filler metal but low enough to prevent the base aluminum from melting. Maintaining this temperature range ensures that the filler metal can effectively flow into the joint, creating a strong bond.
-
Joint Design:
- The design of the joint is crucial for successful brazing. Proper joint design ensures that the filler metal can flow evenly and fill the entire joint area. Common joint designs for aluminum brazing include lap joints, butt joints, and T-joints. The joint must be designed to allow for capillary action, which draws the molten filler metal into the joint.
-
Part Cleanliness:
- Cleanliness is essential in aluminum brazing. Any contaminants, such as oils, oxides, or dirt, can prevent the filler metal from properly bonding to the base metal. Parts must be thoroughly cleaned before brazing, often using chemical cleaning agents or mechanical methods like abrasion. Maintaining a clean surface ensures optimal wetting and flow of the filler metal.
-
Fixturing:
- Fixturing refers to the method of holding the parts in place during the brazing process. Proper fixturing ensures that the parts remain aligned and that the joint is maintained in the correct position while the filler metal flows and solidifies. Fixtures must be designed to withstand the high temperatures of the brazing process without interfering with the joint.
-
Filler Metal Selection:
- The choice of filler metal is critical in aluminum brazing. Common filler metals include aluminum-silicon alloys, which have melting points close to the brazing temperature range. The filler metal must be compatible with the base aluminum and must have good wetting and flow characteristics. The selection of the appropriate filler metal depends on the specific application and the properties required in the final joint.
-
Role of a Rotating Furnace:
- A rotating furnace can be particularly useful in aluminum brazing, especially for complex or large parts. The rotation ensures uniform heating of the parts, which is crucial for achieving consistent brazing results. The even distribution of heat helps prevent hot spots and ensures that the filler metal flows uniformly into the joint. This is particularly important in vacuum brazing, where precise temperature control is essential.
-
Vacuum Brazing Considerations:
- Vacuum brazing is a common method for aluminum, as it prevents oxidation and contamination of the joint. The vacuum environment removes air and moisture, which can interfere with the brazing process. Properly designed vacuum furnaces, combined with the right brazing parameters, can produce high-quality, defect-free joints. The use of a vacuum furnace also allows for precise control of the heating and cooling rates, which is critical for achieving the desired metallurgical properties in the brazed joint.
By carefully considering these factors and using specialized equipment like a rotating furnace, you can achieve successful aluminum brazing with strong, reliable joints.
Summary Table:
Key Factor | Details |
---|---|
Temperature Range | 570°C to 620°C (1058°F to 1148°F) |
Joint Design | Lap joints, butt joints, T-joints; designed for capillary action |
Part Cleanliness | Must be free of oils, oxides, and dirt for proper bonding |
Fixturing | Ensures alignment and stability during heating |
Filler Metal Selection | Aluminum-silicon alloys with compatible melting points |
Rotating Furnace | Ensures uniform heating, ideal for complex or large parts |
Vacuum Brazing | Prevents oxidation and contamination, ensures high-quality joints |
Achieve perfect aluminum brazing results—contact our experts today for tailored solutions!