The growth temperature for CVD graphene typically ranges from 800°C to 1000°C, depending on the specific method, catalyst, and desired graphene properties. The temperature is a critical factor as it influences the reaction kinetics, nucleation rate, and the number of graphene layers formed. Lower temperatures (e.g., 360°C) can produce single-layer graphene, while higher temperatures tend to result in multiple layers. The temperature must be carefully controlled to balance the reaction rate and the quality of the graphene film.
Key Points Explained:
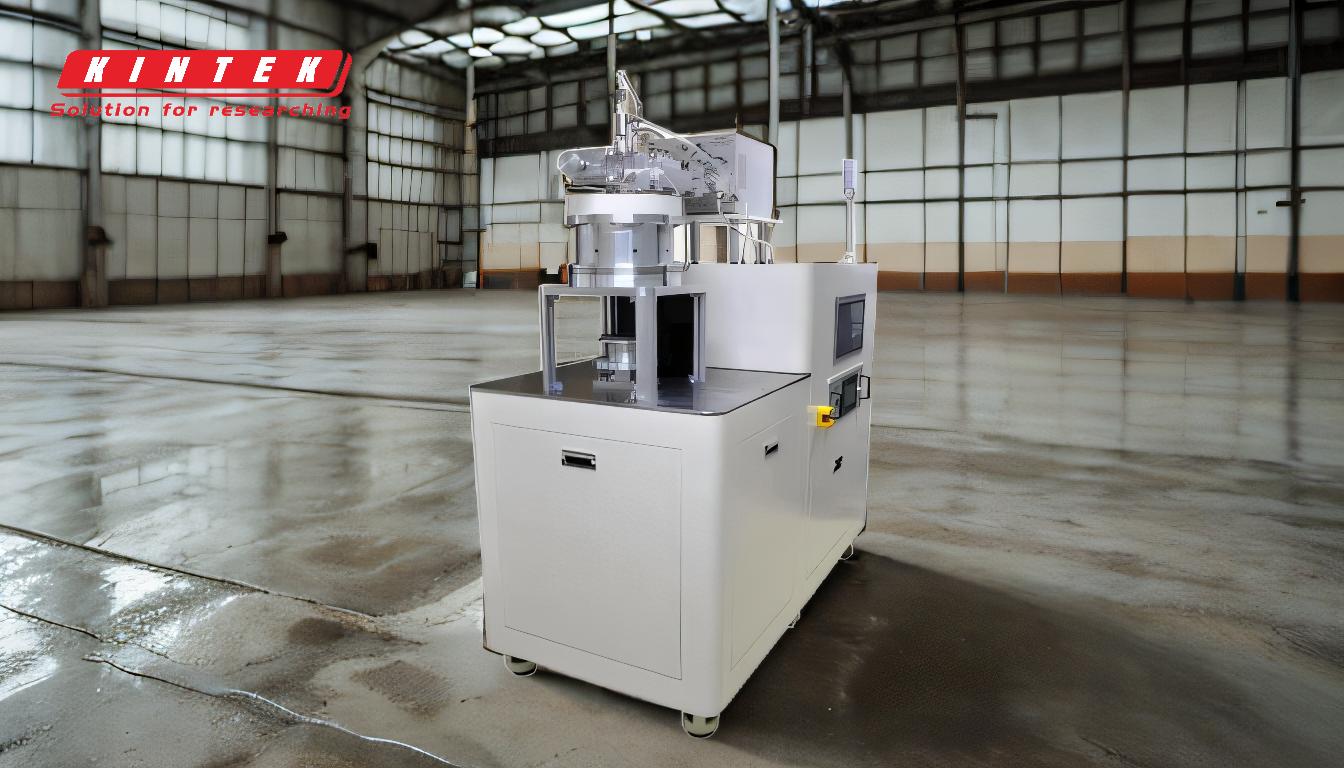
-
Typical Temperature Range for CVD Graphene Growth:
- The standard temperature range for growing graphene using Chemical Vapor Deposition (CVD) is between 800°C and 1000°C. This range is optimal for achieving high-quality, large-area graphene films.
- At these temperatures, carbon precursors decompose effectively on the catalyst surface, enabling the formation of graphene crystals.
-
Temperature Dependence of Reaction Kinetics:
- The reaction rate in CVD is exponentially dependent on temperature. At lower temperatures, the reaction is kinetically controlled, meaning the nucleation rate of graphene is limited by the temperature.
- At higher temperatures, the reaction becomes diffusion-controlled, where the rate is influenced by the flow of feedstock gases rather than temperature alone.
-
Impact of Temperature on Graphene Layer Formation:
- Lower temperatures (e.g., 360°C) can produce single-layer graphene, as seen in experiments with hexachlorobenzene on copper foil.
- Higher temperatures generally lead to the formation of multiple graphene layers. This is because increased thermal energy promotes the nucleation and growth of additional carbon layers.
-
Role of Catalyst and Substrate:
- The choice of catalyst (e.g., copper or nickel) and substrate significantly affects the required growth temperature. Copper is commonly used for single-layer graphene due to its low carbon solubility, while nickel can produce thicker graphene layers at higher temperatures.
-
Importance of Cooling Rate:
- After graphene growth, the cooling rate is critical. A fast cooling rate helps suppress the formation of multiple layers and aids in separating the graphene from the substrate, ensuring high-quality single-layer graphene.
-
Industrial Scalability and Temperature Control:
- CVD is the only method capable of producing graphene on an industrial scale. Precise temperature control is essential to maintain consistency and quality across large-area graphene films.
-
Atmospheric Conditions:
- Graphene growth often occurs under reduced pressure or ultra-high vacuum conditions, which help control the reaction environment and improve the quality of the graphene film.
-
Examples of Temperature-Dependent Growth:
- For instance, heating hexachlorobenzene on copper foil at 360°C yields a single layer of graphene, while higher temperatures (e.g., 1000°C) result in multiple layers. This demonstrates the direct relationship between temperature and graphene layer formation.
By understanding these key points, a purchaser or researcher can make informed decisions about the CVD process parameters to achieve the desired graphene properties for specific applications.
Summary Table:
Aspect | Details |
---|---|
Typical Temperature Range | 800°C–1000°C for high-quality, large-area graphene films. |
Temperature Dependence | Lower temperatures (e.g., 360°C) yield single-layer graphene; higher temperatures produce multiple layers. |
Catalyst Influence | Copper for single-layer; nickel for thicker layers at higher temperatures. |
Cooling Rate | Fast cooling suppresses multiple layers and ensures high-quality graphene. |
Atmospheric Conditions | Reduced pressure or ultra-high vacuum improves graphene quality. |
Industrial Scalability | Precise temperature control is essential for consistent, large-scale production. |
Need help optimizing your CVD graphene process? Contact our experts today for tailored solutions!