Deposition is a critical process in materials science and thin-film technology, where a material is deposited onto a substrate to form a thin film. The temperature at which deposition occurs can vary widely depending on the specific deposition technique, the material being deposited, and the desired properties of the resulting film. This answer explores the factors influencing deposition temperature and how it impacts the film's characteristics.
Key Points Explained:
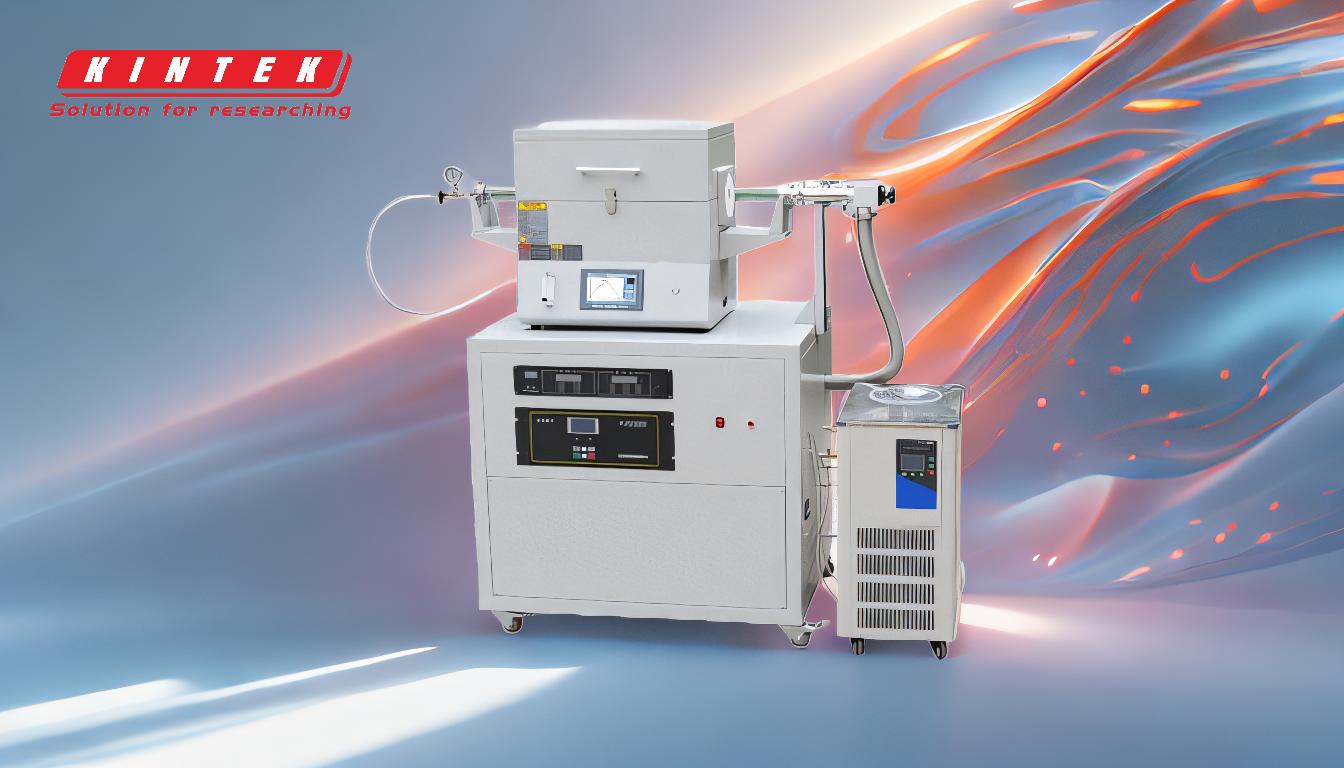
-
Deposition Techniques and Temperature Ranges:
- Physical Vapor Deposition (PVD): Techniques like sputtering and evaporation typically occur at temperatures ranging from room temperature to several hundred degrees Celsius. For example, sputtering of metals like aluminum or titanium often occurs at temperatures between 50°C to 300°C.
- Chemical Vapor Deposition (CVD): CVD processes, such as thermal CVD or plasma-enhanced CVD, generally require higher temperatures, often between 500°C to 1200°C, depending on the material and the desired film properties. For instance, silicon dioxide deposition via CVD can occur at temperatures around 700°C to 900°C.
- Atomic Layer Deposition (ALD): ALD is a low-temperature process, typically operating between 100°C to 400°C, making it suitable for temperature-sensitive substrates.
-
Impact of Temperature on Film Properties:
- Crystallinity: Higher deposition temperatures often lead to better crystallinity in the deposited film. For example, in PVD, elevated temperatures can enhance the mobility of adatoms, leading to more ordered crystalline structures.
- Stress and Adhesion: Temperature can influence the stress and adhesion of the film. Higher temperatures may reduce intrinsic stress but could also increase thermal stress due to differences in thermal expansion coefficients between the film and substrate.
- Density and Uniformity: Elevated temperatures can improve film density and uniformity by promoting better surface diffusion of deposited atoms. However, excessively high temperatures might lead to non-uniformities due to increased desorption or re-evaporation rates.
-
Trade-offs in Deposition Conditions:
- Deposition Rate vs. Temperature: As mentioned in the reference, faster deposition rates often require higher temperatures or power, which can affect film properties. For example, increasing the temperature in CVD can accelerate the reaction kinetics, leading to higher deposition rates but potentially compromising film quality.
- Material-Specific Considerations: Different materials have unique temperature dependencies. For instance, depositing organic materials via PVD might require lower temperatures to prevent decomposition, whereas depositing refractory metals like tungsten via CVD often necessitates high temperatures to achieve the desired film properties.
-
Substrate Considerations:
- Thermal Stability: The substrate's thermal stability is a critical factor in determining the deposition temperature. For example, polymer substrates may degrade at high temperatures, limiting the deposition process to lower temperatures.
- Thermal Expansion Mismatch: Mismatched thermal expansion coefficients between the film and substrate can lead to stress and delamination, especially at high deposition temperatures.
-
Process Optimization:
- Balancing Act: Achieving the desired film properties often involves a trade-off between deposition temperature, rate, and other process parameters. For instance, in ALD, lower temperatures might be used to ensure conformal coverage on complex geometries, even if it means sacrificing some film density.
- Advanced Techniques: Techniques like plasma-enhanced CVD or pulsed laser deposition can allow for lower deposition temperatures while still achieving high-quality films, offering a way to mitigate some of the trade-offs associated with temperature.
In summary, the temperature at which deposition occurs is a critical parameter that significantly influences the properties of the deposited film. It varies widely depending on the deposition technique, material, and substrate, and often involves balancing multiple factors to achieve the desired film characteristics. Understanding these relationships is essential for optimizing deposition processes in various applications.
Summary Table:
Deposition Technique | Temperature Range | Key Characteristics |
---|---|---|
Physical Vapor Deposition (PVD) | 50°C to 300°C | Suitable for metals like aluminum and titanium |
Chemical Vapor Deposition (CVD) | 500°C to 1200°C | Ideal for high-quality films like silicon dioxide |
Atomic Layer Deposition (ALD) | 100°C to 400°C | Perfect for temperature-sensitive substrates |
Impact of Temperature | Effect on Film Properties | |
Higher Temperatures | Improved crystallinity, reduced intrinsic stress, better density | |
Lower Temperatures | Prevents substrate degradation, suitable for organic materials | |
Substrate Considerations | Key Factors | |
Thermal Stability | Limits deposition temperature for sensitive substrates | |
Thermal Expansion Mismatch | Can cause stress or delamination at high temperatures |
Need help optimizing your deposition process? Contact our experts today for tailored solutions!