Brazing ovens, also known as brazing furnaces, are specialized equipment used to join metal parts by heating them to a specific temperature below the melting point of the base metals but above the melting point of the filler metal. The temperature range for brazing typically falls between 500°C (932°F) and 1200°C (2192°F), depending on the materials being joined and the type of filler metal used. The exact temperature is determined by factors such as the composition of the base metals, the filler metal, and the desired joint strength. Brazing ovens are designed to provide precise temperature control, uniform heating, and often operate in controlled atmospheres to prevent oxidation and ensure high-quality joints.
Key Points Explained:
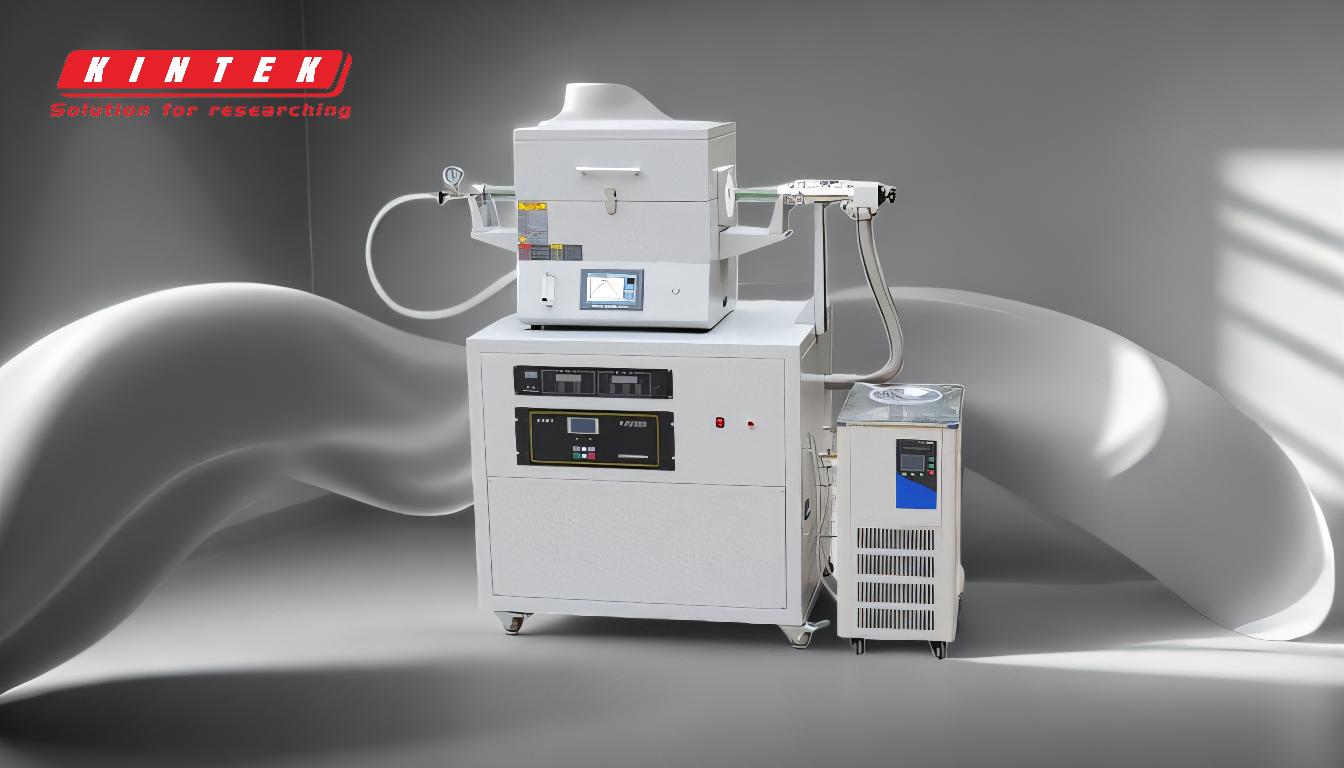
-
Definition and Purpose of Brazing Ovens:
- Brazing ovens are used to join metal parts using a filler metal that melts at a temperature lower than the base metals. This process creates strong, leak-proof, and corrosion-resistant joints.
- The oven provides controlled heating to ensure the filler metal flows evenly into the joint without melting the base metals.
-
Typical Temperature Range for Brazing:
- The temperature for brazing generally ranges from 500°C (932°F) to 1200°C (2192°F).
- The exact temperature depends on the filler metal and the base materials. For example:
- Aluminum brazing typically occurs at 580°C to 620°C (1076°F to 1148°F).
- Copper brazing often requires temperatures around 700°C to 900°C (1292°F to 1652°F).
- Stainless steel brazing may need temperatures up to 1200°C (2192°F).
-
Factors Influencing Brazing Temperature:
- Base Metal Composition: Different metals have varying melting points and thermal properties, which influence the required brazing temperature.
- Filler Metal Type: The filler metal must melt at a temperature lower than the base metals but high enough to create a strong bond. Common filler metals include silver, copper, and aluminum alloys.
- Joint Design and Application: The complexity of the joint and the intended use of the brazed component can affect the temperature selection.
-
Importance of Temperature Control in Brazing Ovens:
- Precise temperature control ensures the filler metal melts and flows properly without overheating the base metals.
- Uniform heating prevents warping or distortion of the components.
- Controlled atmospheres (e.g., inert gases like nitrogen or argon) are often used to prevent oxidation and contamination during the brazing process.
-
Types of Brazing Ovens and Their Temperature Capabilities:
- Batch Furnaces: Suitable for small to medium-sized parts, these ovens can reach temperatures up to 1200°C (2192°F) and are often used for high-temperature brazing.
- Continuous Furnaces: Designed for high-volume production, these ovens maintain consistent temperatures and are ideal for processes requiring precise thermal profiles.
- Vacuum Brazing Furnaces: Used for high-purity applications, these ovens operate at high temperatures (up to 1200°C or 2192°F) in a vacuum to prevent oxidation.
-
Applications of Brazing Ovens:
- Brazing is widely used in industries such as automotive, aerospace, HVAC, and electronics.
- Common applications include joining heat exchangers, radiators, piping systems, and electrical components.
-
Safety and Maintenance Considerations:
- Operators must ensure proper ventilation and use protective equipment when working with high-temperature brazing ovens.
- Regular maintenance, including calibration of temperature controls and inspection of heating elements, is essential to maintain performance and safety.
By understanding the temperature requirements and operational principles of brazing ovens, purchasers can select the right equipment for their specific applications, ensuring high-quality results and efficient production processes.
Summary Table:
Aspect | Details |
---|---|
Typical Temperature Range | 500°C (932°F) to 1200°C (2192°F) |
Aluminum Brazing | 580°C to 620°C (1076°F to 1148°F) |
Copper Brazing | 700°C to 900°C (1292°F to 1652°F) |
Stainless Steel Brazing | Up to 1200°C (2192°F) |
Key Influencing Factors | Base metal composition, filler metal type, joint design, and application |
Oven Types | Batch, Continuous, and Vacuum furnaces |
Applications | Automotive, aerospace, HVAC, and electronics industries |
Need a brazing oven tailored to your needs? Contact our experts today for personalized guidance!