Alumina, a widely used ceramic material, is typically fired at high temperatures to achieve desirable properties such as density and grain size. Based on the provided reference, pure alumina powder compacts can achieve a density of about 99% of the theoretical value and a grain size of 1.2 μm when fired at 1350 °C for 20 minutes. This temperature is critical for sintering, as it allows the particles to bond and densify without excessive grain growth. The firing temperature and duration are key factors in determining the final properties of the alumina ceramic, making it essential for manufacturers to optimize these parameters for specific applications.
Key Points Explained:
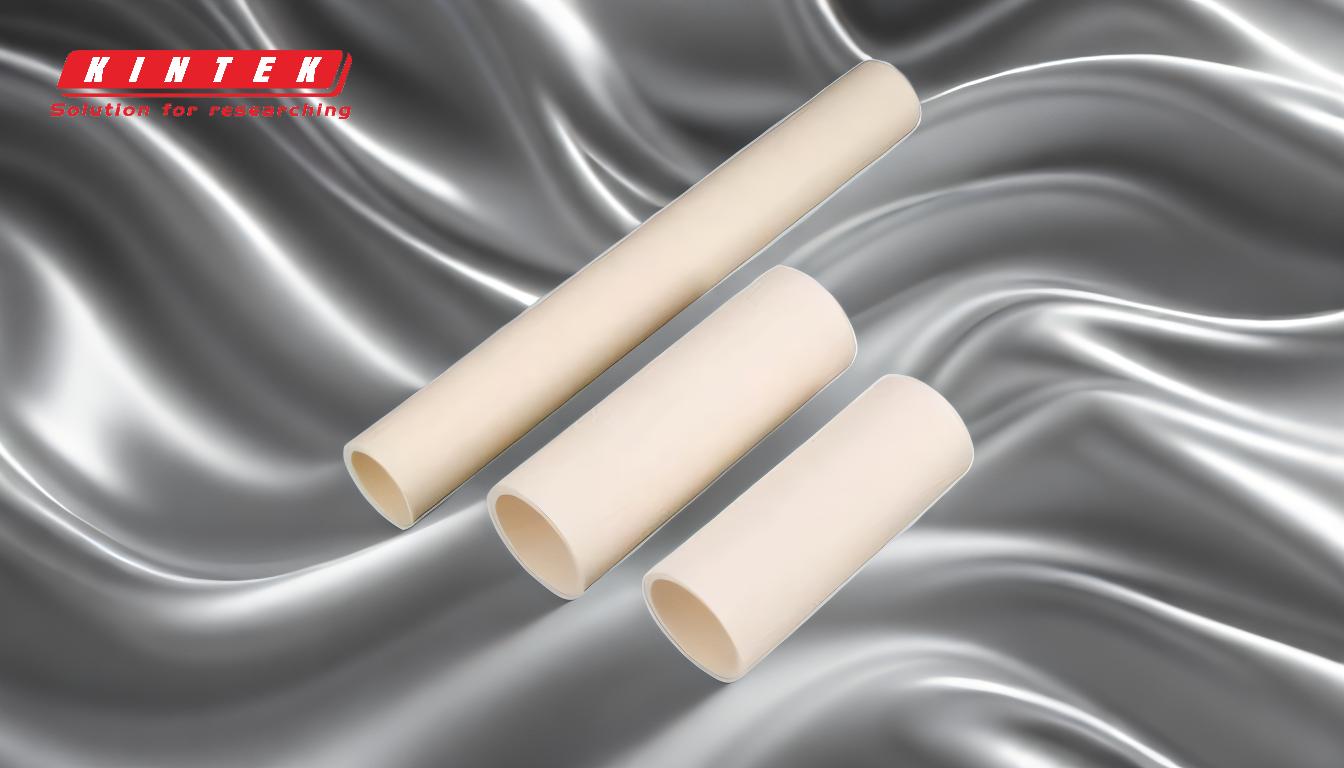
-
Firing Temperature for Alumina:
- The reference states that pure alumina powder compacts are fired at 1350 °C to achieve optimal densification and grain size.
- This temperature is within the typical sintering range for alumina, which generally falls between 1200 °C and 1600 °C, depending on the desired properties and the specific alumina composition.
-
Importance of Temperature in Sintering:
- Sintering is a thermal process where ceramic particles bond together, reducing porosity and increasing density.
- At 1350 °C, the alumina particles undergo sufficient diffusion to achieve a density of 99% of the theoretical value, which is a high level of densification.
- Excessive temperatures can lead to unwanted grain growth, which may compromise mechanical properties, so precise temperature control is crucial.
-
Grain Size and Its Implications:
- The reference mentions a grain size of 1.2 μm after firing at 1350 °C for 20 minutes.
- Grain size is a critical factor in determining the mechanical, thermal, and electrical properties of alumina ceramics.
- Smaller grain sizes, like 1.2 μm, generally result in higher strength and toughness, making the material suitable for demanding applications such as cutting tools, wear-resistant components, and electronic substrates.
-
Firing Duration:
- The firing process described in the reference lasts for 20 minutes.
- The duration of firing influences the extent of densification and grain growth. Shorter times may not achieve full densification, while longer times could lead to excessive grain growth.
- For high-quality alumina ceramics, the combination of temperature and time must be carefully balanced.
-
Theoretical Density:
- Achieving 99% of the theoretical density indicates that the alumina ceramic has minimal porosity, which is essential for applications requiring high mechanical strength and thermal stability.
- Theoretical density is the maximum possible density of a material, assuming no voids or defects. Achieving near-theoretical density is a hallmark of high-quality ceramic processing.
-
Applications of High-Density Alumina:
- High-density alumina with controlled grain size is used in various industries, including:
- Electronics: As substrates for integrated circuits due to its excellent electrical insulation and thermal conductivity.
- Mechanical Engineering: For wear-resistant components and cutting tools.
- Medical Devices: In implants and prosthetics due to its biocompatibility and durability.
- The firing temperature of 1350 °C, as mentioned in the reference, is suitable for producing alumina ceramics for these applications.
- High-density alumina with controlled grain size is used in various industries, including:
-
Optimization of Firing Parameters:
- The firing temperature and duration must be tailored to the specific alumina powder and the intended application.
- Factors such as particle size distribution, purity, and additives can influence the optimal firing conditions.
- Manufacturers often conduct experiments to determine the best combination of temperature and time for their specific requirements.
In summary, firing alumina at 1350 °C for 20 minutes is an effective approach to achieving high-density, fine-grained alumina ceramics. This temperature ensures sufficient densification while minimizing grain growth, making it suitable for a wide range of industrial applications. Understanding and optimizing these parameters is essential for producing high-performance alumina components.
Summary Table:
Parameter | Value |
---|---|
Firing Temperature | 1350°C |
Firing Duration | 20 minutes |
Achieved Density | 99% of theoretical |
Grain Size | 1.2 μm |
Applications | Electronics, Mechanical Engineering, Medical Devices |
Optimize your alumina ceramic production—contact our experts today for tailored solutions!