Porcelain, a type of ceramic material, requires specific temperature ranges during its firing process to achieve the desired strength, durability, and aesthetic qualities. The firing temperature for porcelain typically ranges between 1200°C and 1400°C (2192°F to 2552°F), depending on the type of porcelain and the desired outcome. This high-temperature process ensures that the clay body vitrifies, becoming non-porous and glass-like. The exact temperature depends on factors such as the composition of the clay, the type of kiln used, and the intended use of the final product. Understanding these temperature requirements is crucial for achieving the best results in porcelain production.
Key Points Explained:
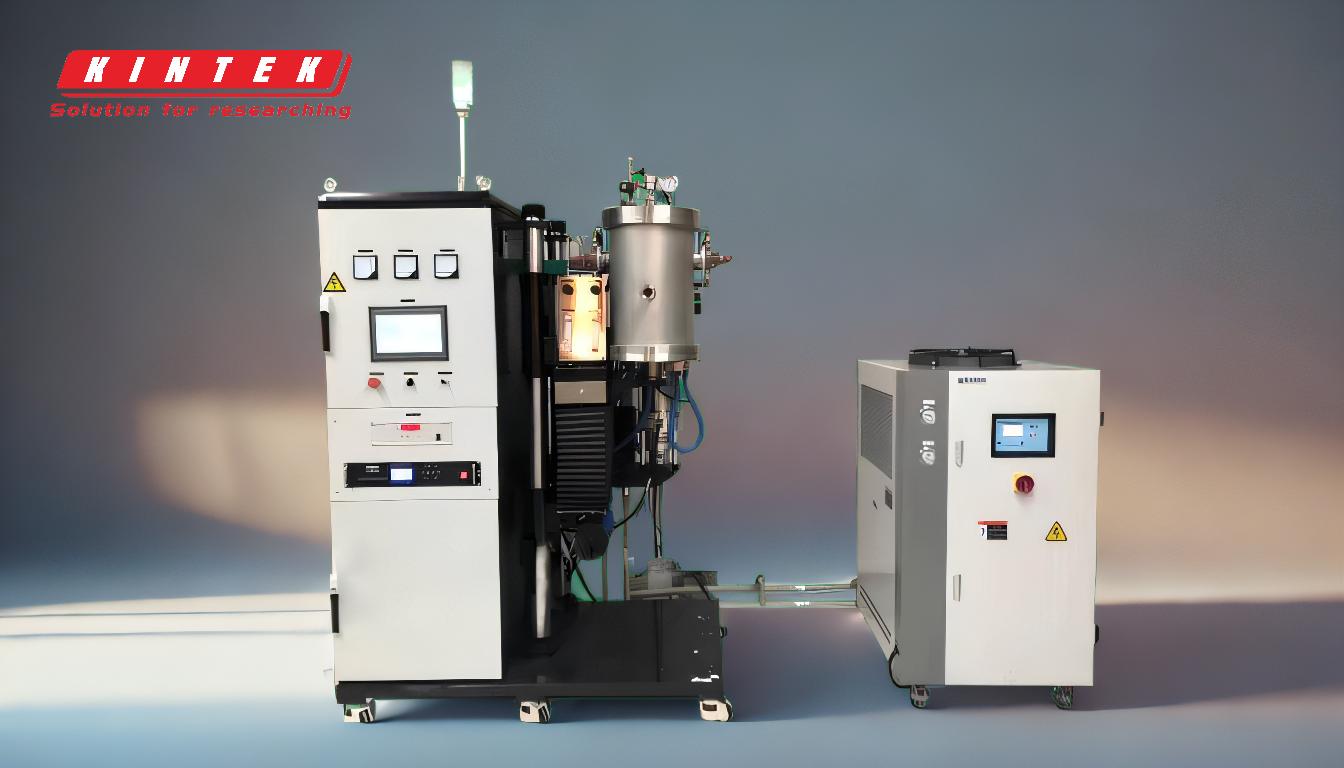
-
Temperature Range for Porcelain Firing:
- Porcelain is typically fired at temperatures between 1200°C and 1400°C (2192°F to 2552°F). This range ensures that the clay body vitrifies, becoming dense and non-porous. Vitrification is the process where the clay particles fuse together, creating a glass-like structure that gives porcelain its characteristic strength and translucency.
-
Types of Porcelain and Their Firing Temperatures:
- Hard-Paste Porcelain: This type of porcelain is fired at the higher end of the temperature range, around 1400°C (2552°F). It is known for its strength and durability, making it ideal for fine china and high-quality tableware.
- Soft-Paste Porcelain: Fired at slightly lower temperatures, around 1200°C to 1300°C (2192°F to 2372°F), soft-paste porcelain is less dense and more porous. It is often used for decorative items and art pieces.
- Bone China: A type of porcelain that includes bone ash in its composition, bone china is fired at around 1200°C to 1250°C (2192°F to 2282°F). It is known for its whiteness and translucency.
-
Factors Influencing Firing Temperature:
- Clay Composition: The specific minerals and additives in the clay can affect the firing temperature. For example, kaolin, a key component of porcelain, requires high temperatures to vitrify.
- Kiln Type: The type of kiln used (electric, gas, or wood-fired) can influence the firing temperature and atmosphere, affecting the final properties of the porcelain.
- Desired Outcome: The intended use of the porcelain (e.g., tableware, decorative items, or industrial applications) may require different firing temperatures to achieve the desired strength, color, and finish.
-
Importance of Temperature Control:
- Precise temperature control is crucial during the firing process. Over-firing can cause the porcelain to warp or bloat, while under-firing may result in a weak, porous product. Modern kilns are equipped with digital controllers to ensure accurate temperature regulation.
-
Cooling and Annealing:
- After reaching the peak temperature, the porcelain must be cooled slowly to prevent cracking or thermal shock. This process, known as annealing, allows the material to stabilize and reduces internal stresses.
Understanding the temperature requirements for porcelain firing is essential for producing high-quality ceramic products. By carefully controlling the firing process, manufacturers can achieve the desired properties and ensure the longevity and beauty of their porcelain items.
Summary Table:
Type of Porcelain | Firing Temperature | Key Characteristics |
---|---|---|
Hard-Paste Porcelain | ~1400°C (2552°F) | Strong, durable, ideal for fine china |
Soft-Paste Porcelain | 1200°C–1300°C (2192°F–2372°F) | Less dense, porous, used for decorative items |
Bone China | 1200°C–1250°C (2192°F–2282°F) | Whiteness, translucency, lightweight |
Need help achieving the perfect firing temperature for your porcelain? Contact our experts today for personalized advice!