Sintering steel typically requires temperatures in the range of 1100°C to 1400°C, depending on the specific type of steel and the desired properties. The process involves heating the steel powder to a temperature below its melting point, allowing the particles to bond and form a solid structure. The exact temperature and duration of sintering can vary based on factors such as the composition of the steel, the particle size, and the desired density and strength of the final product. A zirconia sintering furnace is often used for such high-temperature processes due to its ability to maintain precise temperature control and uniform heating.
Key Points Explained:
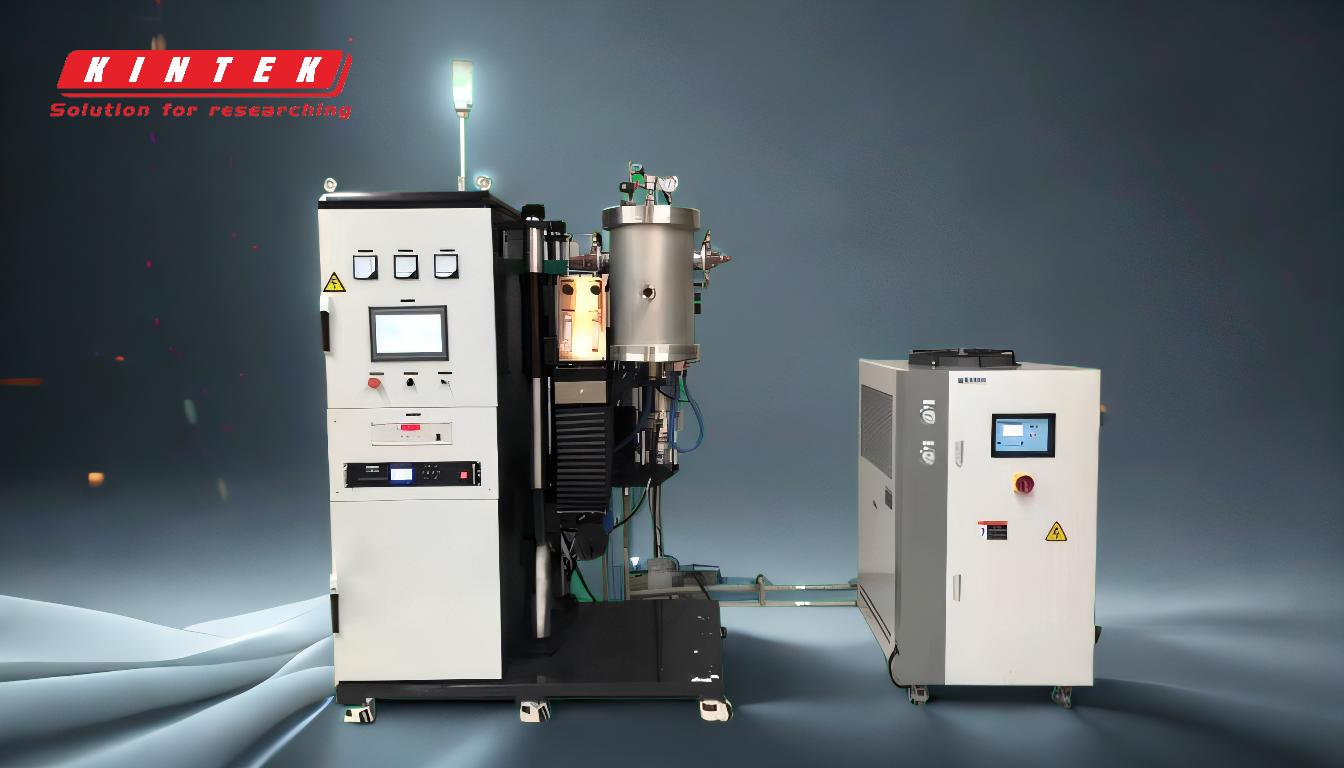
-
Temperature Range for Sintering Steel:
- Sintering steel generally requires temperatures between 1100°C and 1400°C. This range is chosen because it is high enough to allow the particles to bond without melting the steel, which would compromise the structural integrity of the final product.
- The specific temperature within this range depends on the type of steel and the desired properties, such as density and strength.
-
Importance of Temperature Control:
- Precise temperature control is crucial during the sintering process. Inconsistent temperatures can lead to uneven sintering, resulting in weak spots or defects in the final product.
- A zirconia sintering furnace is equipped with advanced temperature control systems, such as PID controllers, which ensure accurate temperature regulation with minimal deviation (±1℃).
-
Heating and Cooling Rates:
- The rate at which the steel is heated and cooled can significantly affect the sintering outcome. Rapid heating or cooling can cause thermal stress, leading to cracks or other defects.
- The furnace should allow for controlled ramp rates, especially during critical phases such as the transition from 900°C to the top sintering temperature and the subsequent cooling phase.
-
Density and Strength:
- The goal of sintering is to achieve maximum density and strength. For steel, this typically means reaching close to 99% of the theoretical maximum density.
- Higher sintering temperatures, closer to the upper end of the 1100°C to 1400°C range, are often used to achieve this level of density.
-
Use of Zirconia Sintering Furnaces:
- Zirconia sintering furnaces are well-suited for sintering steel due to their ability to reach and maintain high temperatures with precision.
- These furnaces often feature advanced heating elements, efficient air circulation systems, and environmental insulation materials, which contribute to stable and uniform heating.
-
Programmability and Automation:
- Modern sintering furnaces, including those used for zirconia, offer programmable settings that allow users to store multiple sintering profiles. This is particularly useful for sintering different types of steel or achieving specific material properties.
- Features like memory functions ensure that the sintering process can resume from the point of interruption in case of a power outage, maintaining process consistency.
In summary, sintering steel requires careful control of temperature, heating, and cooling rates to achieve the desired density and strength. A zirconia sintering furnace is an excellent choice for this process due to its precision, programmability, and advanced features that ensure consistent and high-quality results.
Summary Table:
Aspect | Details |
---|---|
Temperature Range | 1100°C to 1400°C, depending on steel type and desired properties. |
Temperature Control | ±1℃ precision using PID controllers in zirconia sintering furnaces. |
Heating/Cooling Rates | Controlled ramp rates to prevent thermal stress and defects. |
Density & Strength | Achieve ~99% theoretical density with higher sintering temperatures. |
Furnace Features | Advanced heating elements, air circulation, and programmable settings. |
Ready to optimize your steel sintering process? Contact us today to learn more about zirconia sintering furnaces!