Physical Vapor Deposition (PVD) is a coating process that typically operates at relatively low temperatures, making it suitable for a wide range of substrates, including temperature-sensitive materials. The process temperature for PVD generally ranges between 200°C and 600°C, depending on the specific method, equipment, and substrate material. This is significantly lower than Chemical Vapor Deposition (CVD), which often requires temperatures above 600°C, sometimes up to 1100°C. PVD's lower temperature range is advantageous for applications where high temperatures could damage the substrate or alter its properties.
Key Points Explained:
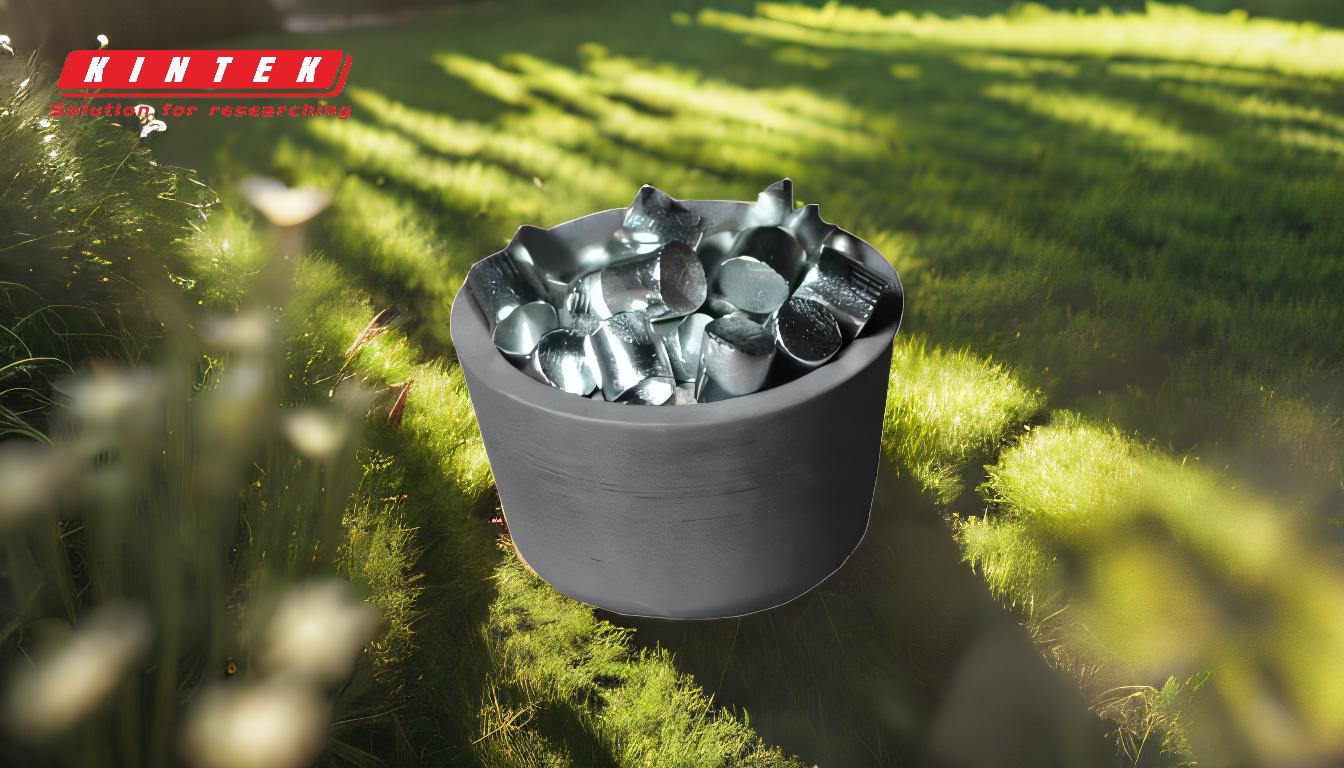
-
Typical Temperature Range for PVD:
- PVD processes generally operate at temperatures between 200°C and 600°C.
- The substrate temperature during PVD is typically maintained in the range of 200-400°C, which is lower than CVD processes.
- This lower temperature range is a key advantage of PVD, as it minimizes the risk of thermal damage to the substrate.
-
Comparison with CVD:
- Chemical Vapor Deposition (CVD) requires much higher temperatures, typically ranging from 600°C to 1100°C.
- The high temperatures in CVD are necessary to facilitate chemical reactions between the gas phase and the substrate.
- PVD, on the other hand, relies on physical processes (e.g., sputtering or evaporation) to deposit material, which do not require such high temperatures.
-
Substrate-Specific Temperature Control:
- The temperature during PVD can be adjusted based on the substrate material. For example:
- Plastic substrates: Temperatures as low as 50°F (10°C) may be used to prevent melting or deformation.
- Metallic substrates (e.g., steel, brass, zinc): Temperatures can range from 200°C to 400°C.
- This flexibility makes PVD suitable for a wide variety of materials, including those that are sensitive to heat.
- The temperature during PVD can be adjusted based on the substrate material. For example:
-
Plasma-Enhanced PVD (PECVD):
- Plasma-enhanced PVD processes can operate at even lower temperatures, sometimes near room temperature (RT), with optional heating up to 350°C.
- This is particularly beneficial for temperature-sensitive substrates, such as polymers or certain electronic components.
-
Advantages of Lower Temperatures:
- Reduced thermal stress: Lower temperatures minimize the risk of warping, cracking, or other thermal damage to the substrate.
- Broader material compatibility: PVD can be used on materials that cannot withstand the high temperatures required for CVD.
- Energy efficiency: Operating at lower temperatures reduces energy consumption compared to high-temperature processes like CVD.
-
Applications of PVD:
- PVD is widely used in industries such as:
- Electronics: For depositing thin films on semiconductors and other components.
- Automotive: For coating engine parts and decorative finishes.
- Medical devices: For biocompatible coatings on implants.
- Optics: For anti-reflective and protective coatings on lenses.
- PVD is widely used in industries such as:
In summary, the temperature range for Physical Vapor Deposition (PVD) is generally between 200°C and 600°C, with substrate temperatures typically maintained at 200-400°C. This lower temperature range, compared to CVD, makes PVD a versatile and energy-efficient process suitable for a wide variety of materials and applications.
Summary Table:
Aspect | Details |
---|---|
Typical PVD Temperature | 200°C to 600°C (substrate: 200-400°C) |
Comparison with CVD | CVD requires 600°C to 1100°C; PVD is lower and safer for sensitive materials |
Substrate Flexibility | Adjustable for plastics (as low as 10°C) and metals (200°C-400°C) |
Plasma-Enhanced PVD | Operates near room temperature, ideal for polymers and electronics |
Advantages | Reduced thermal stress, broader material compatibility, energy efficiency |
Applications | Electronics, automotive, medical devices, optics |
Interested in how PVD can benefit your project? Contact our experts today to learn more!