The optimal temperature range for brazing copper in a hydrogen atmosphere is typically between 1,100 and 1,500℉. This range ensures proper bonding of the copper components while minimizing the risk of overheating or damaging the material. Below is a detailed explanation of the key factors and considerations related to this temperature range.
Key Points Explained:
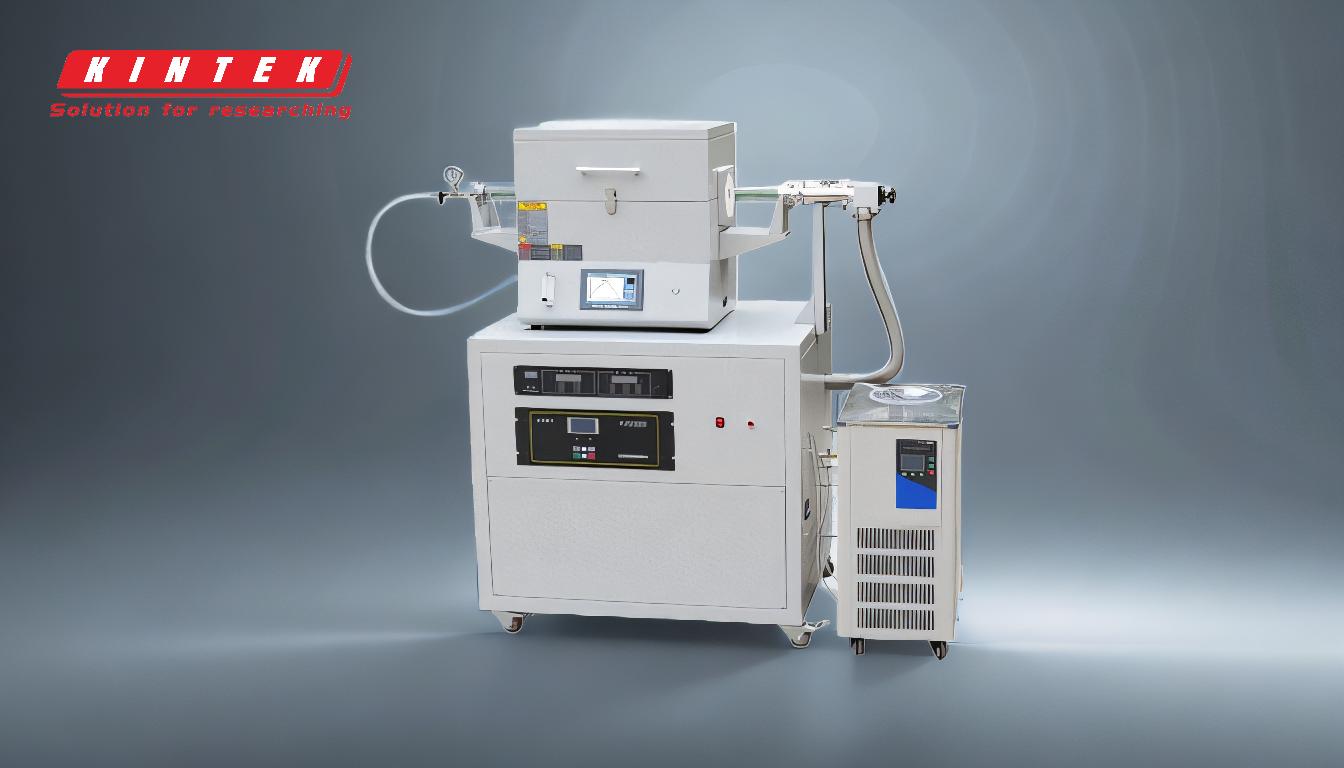
-
Optimal Temperature Range:
- The recommended temperature range for copper brazing in a hydrogen atmosphere is 1,100 to 1,500℉. This range is ideal because it allows the filler material to melt and flow properly, creating a strong joint without compromising the integrity of the copper.
-
Importance of Temperature Control:
- Maintaining the correct temperature is critical for successful brazing. If the temperature is too low, the filler material may not melt sufficiently, leading to weak joints. Conversely, if the temperature is too high, the copper may become overheated, resulting in warping or other damage.
-
Role of Hydrogen Atmosphere:
- A hydrogen atmosphere is commonly used in copper brazing because it helps reduce oxidation and ensures a clean surface for bonding. The temperature range of 1,100 to 1,500℉ is particularly effective in this environment, as it promotes the reduction of oxides and enhances the flow of the filler material.
-
Filler Material Considerations:
- The choice of filler material can influence the optimal brazing temperature. For copper brazing, silver-based or copper-phosphorus alloys are often used. These materials have melting points that align well with the 1,100 to 1,500℉ range, ensuring proper bonding.
-
Equipment Requirements:
- To achieve the desired temperature range, a high-quality brazing furnace with precise temperature control is essential. The furnace should be capable of maintaining a consistent temperature throughout the brazing process to ensure uniform heating and reliable results.
-
Safety and Process Optimization:
- Operating within the 1,100 to 1,500℉ range also enhances safety by reducing the risk of overheating and potential hazards. Additionally, this range optimizes the brazing process, leading to stronger joints and better overall performance of the finished product.
By adhering to the recommended temperature range and considering the factors outlined above, you can achieve high-quality copper brazing results in a hydrogen atmosphere.
Summary Table:
Key Factor | Details |
---|---|
Optimal Temperature Range | 1,100–1,500℉ ensures proper filler flow and strong joints. |
Temperature Control | Critical to avoid weak joints or overheating. |
Hydrogen Atmosphere | Reduces oxidation and enhances filler flow. |
Filler Material | Silver-based or copper-phosphorus alloys work best in this range. |
Equipment Requirements | High-quality furnace with precise temperature control is essential. |
Safety & Optimization | Reduces overheating risks and improves joint strength. |
Need a furnace for precise copper brazing? Contact our experts today to find the perfect solution!