Magnetron sputtering is a versatile and widely used technique for depositing thin films across various industries, including microelectronics, optics, and machining. The thickness of coatings produced by magnetron sputtering typically ranges from angstroms to microns, influenced by factors such as sputtering duration, material mass, energy levels of coating particles, and process parameters like target-substrate distance, ion energy, and gas pressure. This method is capable of producing both single-material and multi-layered coatings, making it suitable for applications ranging from semiconductor devices to decorative and functional films.
Key Points Explained:
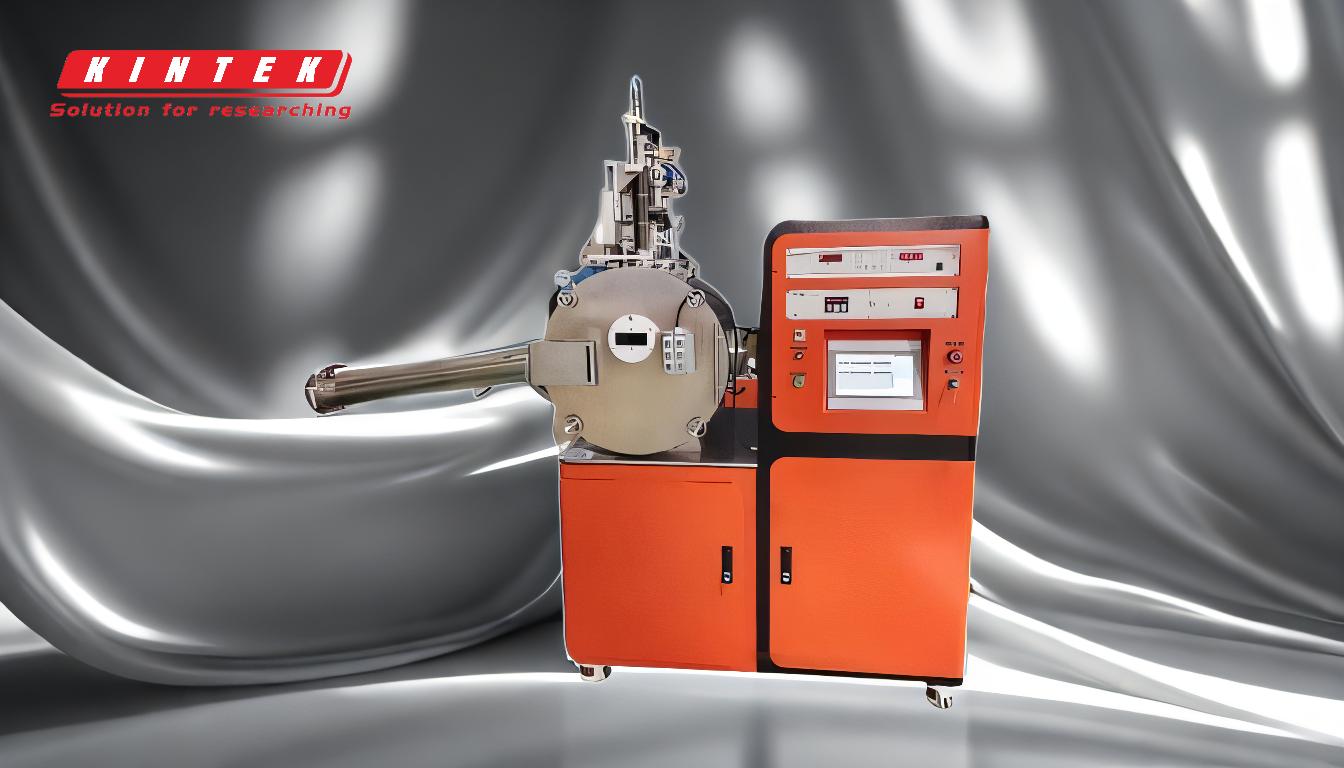
-
Thickness Range of Magnetron Sputtering Coatings:
- Magnetron sputtering produces coatings with thicknesses ranging from angstroms to microns.
- This range allows for precise control over film thickness, making it suitable for applications requiring ultra-thin or thicker functional layers.
-
Factors Influencing Coating Thickness:
- Sputtering Duration: Longer sputtering times generally result in thicker coatings.
- Material Mass: Heavier materials may require more energy to sputter, affecting deposition rates and thickness.
- Energy Levels of Coating Particles: Higher energy levels (ranging from tens to thousands of electron volts) can increase the deposition rate and influence film thickness.
-
Process Parameters:
- Target-Substrate Distance: Closer distances can enhance deposition rates but may affect uniformity.
- Ion Energy: Higher ion energy can improve film density and adhesion but may also impact thickness uniformity.
- Gas Pressure: Optimal gas pressure is critical for achieving consistent film thickness and quality.
-
Applications Requiring Specific Thickness Ranges:
- Semiconductor Industry: Thin films in the range of angstroms to nanometers are used for integrated circuits and hard disk production.
- Optical Films: Coatings with precise thickness control are essential for applications like low-radiation glass and transparent conductive glass.
- Decorative and Functional Films: Thicker coatings (up to microns) are used for high-grade decorations, wear-resistant films, and super-hard films on tools and molds.
-
Uniformity and Control:
- Achieving uniform thickness is critical in magnetron sputtering. Factors like target erosion, temperature, and geometric parameters (e.g., target-substrate alignment) play a significant role in ensuring consistent film quality.
- Advanced systems often incorporate real-time monitoring and feedback mechanisms to maintain thickness uniformity across large substrates.
-
Multi-Layered and Composite Coatings:
- Magnetron sputtering can deposit single-material or multi-layered coatings, enabling the creation of complex structures with tailored properties.
- For example, layered films can combine materials with different refractive indices for optical applications or integrate hard and lubricating layers for wear-resistant coatings.
-
Industry-Specific Examples:
- Microelectronics: Used for depositing thin films in integrated circuits and memory devices.
- Optics: Applied in the production of anti-reflective coatings, mirrors, and optical filters.
- Machining: Utilized for depositing super-hard and self-lubricating films on cutting tools and molds.
- Automotive and Aerospace: Employed for wear-resistant and protective coatings on critical components.
-
Research and Development:
- Magnetron sputtering is instrumental in advancing research areas such as high-temperature superconducting films, ferroelectric films, and solar cell materials.
- Its ability to produce films with precise thickness and composition makes it a key tool for developing next-generation materials.
In summary, magnetron sputtering offers exceptional flexibility in controlling coating thickness, making it indispensable for a wide range of industrial and research applications. By understanding and optimizing the factors influencing thickness, manufacturers and researchers can tailor coatings to meet specific performance requirements.
Summary Table:
Aspect | Details |
---|---|
Thickness Range | Angstroms to microns |
Key Influencing Factors | Sputtering duration, material mass, energy levels, process parameters |
Applications | Microelectronics, optics, machining, decorative films |
Uniformity & Control | Real-time monitoring, target-substrate alignment, gas pressure optimization |
Multi-Layered Coatings | Single-material or composite films for tailored properties |
Industry Examples | Semiconductor devices, optical filters, wear-resistant tools |
Optimize your thin film deposition process with magnetron sputtering—contact our experts today!