Laser sintering, a key additive manufacturing technique, is widely used across industries due to its ability to create complex, custom, and high-performance parts with precision. It is particularly valuable in industries like aerospace, healthcare, and prototyping, where the ability to produce intricate designs and durable materials is critical. Laser sintering is also employed in manufacturing electrical components, semiconductors, and optical fibers, as well as in creating structural steel parts, medical devices, and cutting tools. Its versatility in enhancing material properties like strength, conductivity, and translucency makes it a preferred method for producing functional and high-quality components.
Key Points Explained:
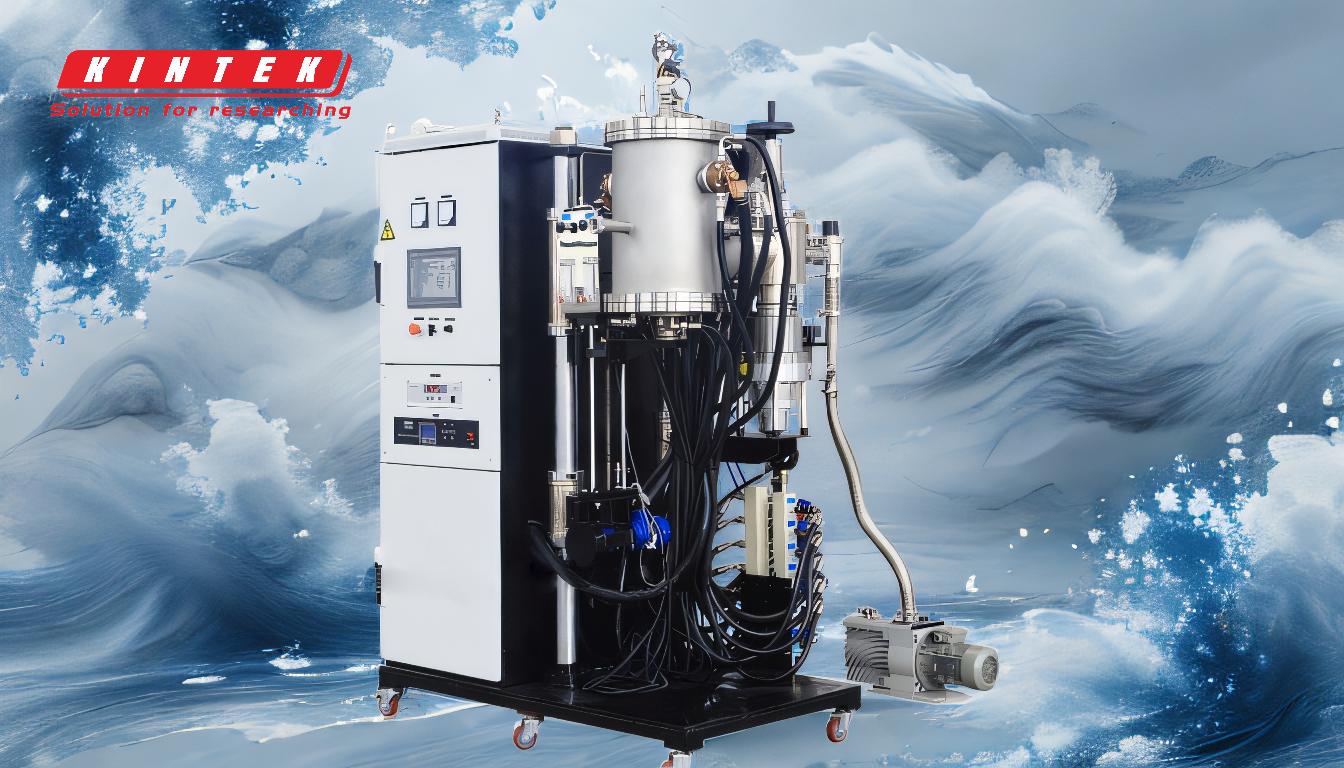
-
Aerospace Industry:
- Laser sintering is used to manufacture lightweight, high-strength components such as turbine blades, brackets, and structural parts.
- The ability to create complex geometries and reduce material waste makes it ideal for aerospace applications.
- Example: Producing custom metal forms for jet engine components that require high precision and durability.
-
Healthcare and Medical Devices:
- Laser sintering is employed to create custom dental implants, prosthetics, and surgical tools.
- It allows for the production of patient-specific medical devices with biocompatible materials.
- Example: Manufacturing porous metal implants that promote bone growth and integration.
-
Prototyping and Custom Manufacturing:
- Rapid prototyping using laser sintering enables designers to quickly produce and test functional prototypes.
- It is cost-effective for creating custom metal forms and small-batch production.
- Example: Developing intricate 3D-printed parts for testing in automotive or consumer electronics.
-
Electrical and Optical Components:
- Laser sintering is used to produce semiconductors, electrical contacts, and optical fibers.
- The process enhances conductivity and precision, making it suitable for high-tech applications.
- Example: Creating micro-sized components for electronic devices with high thermal and electrical performance.
-
Industrial and Structural Applications:
- The technique is used to manufacture structural steel parts, self-lubricating bearings, and cutting tools.
- It improves material properties like strength and wear resistance, extending the lifespan of industrial components.
- Example: Producing tungsten wiring for high-temperature environments or magnetic materials for motors.
-
Material Enhancement:
- Laser sintering enhances the strength, conductivity, and translucency of metals, making them suitable for specialized applications.
- Example: Creating porous metals for filtering or self-lubricating bearings that reduce friction in machinery.
By leveraging laser sintering, industries can achieve greater design flexibility, material efficiency, and performance optimization, making it a cornerstone of modern manufacturing.
Summary Table:
Industry | Applications | Benefits |
---|---|---|
Aerospace | Turbine blades, brackets, structural parts | Lightweight, high-strength, reduced material waste |
Healthcare | Dental implants, prosthetics, surgical tools | Biocompatible materials, patient-specific designs |
Prototyping | Functional prototypes, custom metal forms | Rapid production, cost-effective for small batches |
Electrical/Optical | Semiconductors, electrical contacts, optical fibers | Enhanced conductivity, precision for high-tech applications |
Industrial | Structural steel parts, self-lubricating bearings, cutting tools | Improved strength, wear resistance, extended lifespan |
Material Enhancement | Porous metals, self-lubricating bearings | Enhanced strength, conductivity, and translucency for specialized uses |
Unlock the potential of laser sintering for your industry—contact us today to learn more!