The Chemical Vapor Deposition (CVD) process involves the use of various gases to deposit thin films or coatings on substrates. These gases serve as precursors, reactants, or carriers, depending on the specific application and desired material properties. The process typically involves introducing gaseous precursors into a reaction chamber, activating them through heat or plasma, and allowing them to react on the substrate surface to form the desired material. Byproducts are then removed from the chamber. The choice of gases depends on the material being deposited, the reaction conditions, and the desired film properties. Common gases used in CVD include bulk gases like argon (Ar), helium (He), nitrogen (N2), and oxygen (O2), as well as reactive gases such as silane (SiH4), ammonia (NH3), and metal-organic compounds. These gases play critical roles in the decomposition, reaction, and deposition processes.
Key Points Explained:
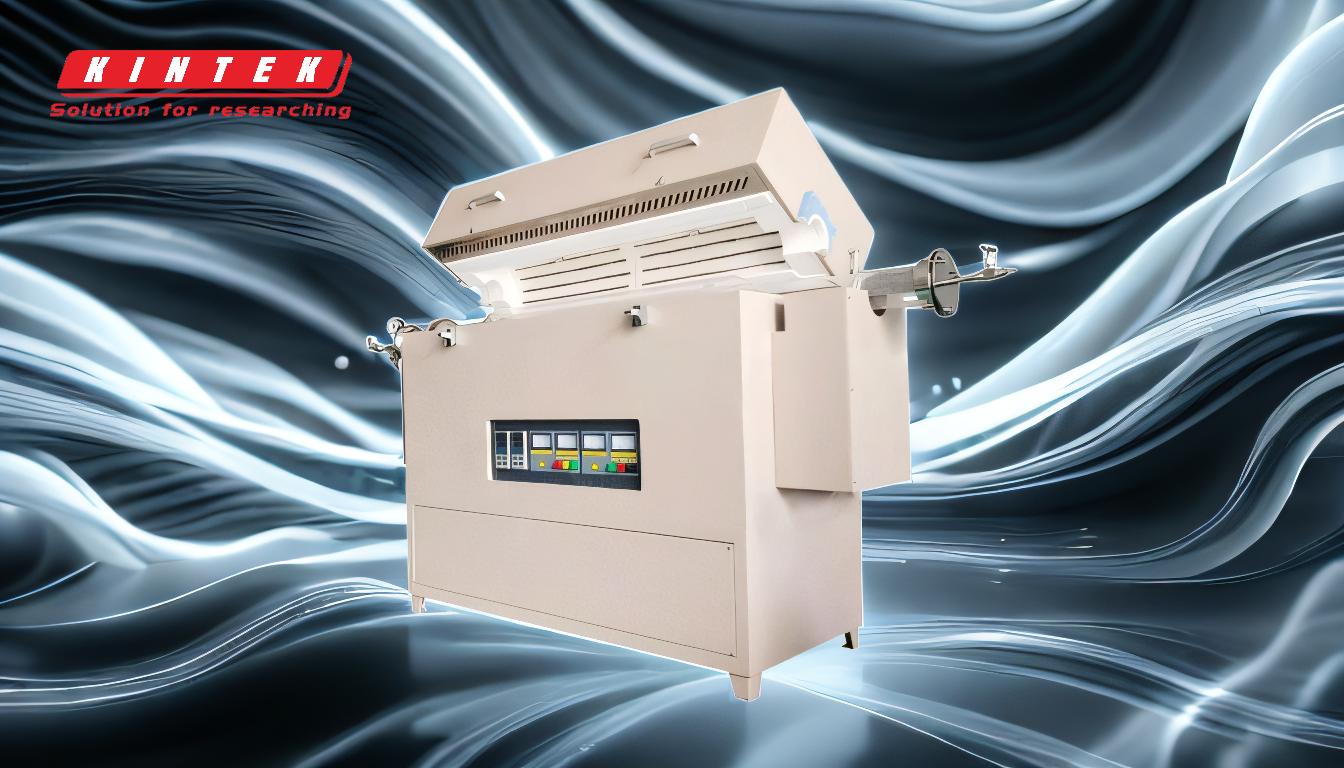
-
Bulk Gases in CVD:
- Bulk gases like argon (Ar), helium (He), nitrogen (N2), and oxygen (O2) are commonly used in CVD processes. These gases serve as carriers or diluents, helping to transport reactive gases and maintain stable reaction conditions.
- Argon and helium are inert gases that provide a non-reactive environment, preventing unwanted reactions during deposition.
- Nitrogen and oxygen can act as reactive gases in certain CVD processes, such as the formation of nitrides or oxides.
-
Reactive Gases:
- Reactive gases are essential for the chemical reactions that lead to film deposition. Examples include:
- Silane (SiH4): Used for depositing silicon-based films, such as silicon dioxide (SiO2) or silicon nitride (Si3N4).
- Ammonia (NH3): Often used in combination with other gases to deposit nitride films.
- Metal-organic compounds: These are used in Metal-Organic Chemical Vapor Deposition (MOCVD) to deposit metals and metal oxides.
- Reactive gases are essential for the chemical reactions that lead to film deposition. Examples include:
-
Chamber Clean Gases:
- Gases like nitrogen trifluoride (NF3) are used for cleaning the reaction chamber. NF3 is highly effective in removing residual deposits from the chamber walls, ensuring consistent deposition quality.
-
Role of Gases in Surface Reactions:
- The CVD process involves several key surface reactions, including decomposition, adsorption, and desorption. Gases like silane and ammonia decompose at high temperatures, releasing reactive species that adsorb onto the substrate surface and form the desired film.
- Volatile byproducts, such as hydrogen (H2) or hydrochloric acid (HCl), are desorbed and removed from the chamber.
-
Process-Specific Gas Selection:
- The choice of gases depends on the specific CVD process and the material being deposited. For example:
- Silicon-based films: Silane (SiH4) and oxygen (O2) are commonly used.
- Nitride films: Ammonia (NH3) and nitrogen (N2) are key reactants.
- Metal films: Metal-organic compounds and hydrogen (H2) are often used.
- The choice of gases depends on the specific CVD process and the material being deposited. For example:
-
Energy and Waste Considerations:
- The use of gases in CVD contributes to energy consumption and waste generation. For instance, the decomposition of reactive gases like silane or ammonia requires significant thermal energy.
- Efficient gas utilization and byproduct management are critical for minimizing environmental impact and operational costs.
In summary, the CVD process relies on a combination of bulk, reactive, and cleaning gases to achieve precise and high-quality film deposition. The selection and optimization of these gases are crucial for the success of the CVD process, ensuring the desired material properties and minimizing waste.
Summary Table:
Gas Type | Examples | Role in CVD Process |
---|---|---|
Bulk Gases | Argon (Ar), Helium (He) | Serve as carriers or diluents, maintain stable reaction conditions. |
Nitrogen (N2), Oxygen (O2) | Can act as reactive gases for nitrides or oxides. | |
Reactive Gases | Silane (SiH4), Ammonia (NH3) | Essential for chemical reactions to deposit silicon-based or nitride films. |
Metal-organic compounds | Used in MOCVD to deposit metals and metal oxides. | |
Cleaning Gases | Nitrogen Trifluoride (NF3) | Effectively clean reaction chambers, ensuring consistent deposition quality. |
Optimize your CVD process with the right gases—contact our experts today for tailored solutions!