Chemical vapor deposition (CVD) is a highly advantageous process used in various industries due to its versatility, precision, and efficiency. It is relatively affordable, offers high deposition rates, and provides uniform coatings with excellent adhesion. CVD is capable of producing high-purity products and is a non-line-of-sight process, making it suitable for coating complex and precision surfaces. Additionally, it allows for the creation of ultra-thin layers of materials, which is crucial for applications like electrical circuits. The process is adaptable to a wide range of materials, including ceramics, metals, and glass, and can be optimized for properties such as corrosion resistance, abrasion resistance, and high purity. CVD also results in durable coatings that can withstand extreme temperatures and high-stress environments. Furthermore, it offers better thickness control, smoother surfaces, and improved electrical and thermal conductivity compared to other deposition technologies. The process is environmentally friendly, with a reduced CO2 footprint, and the equipment used is simple to operate and maintain.
Key Points Explained:
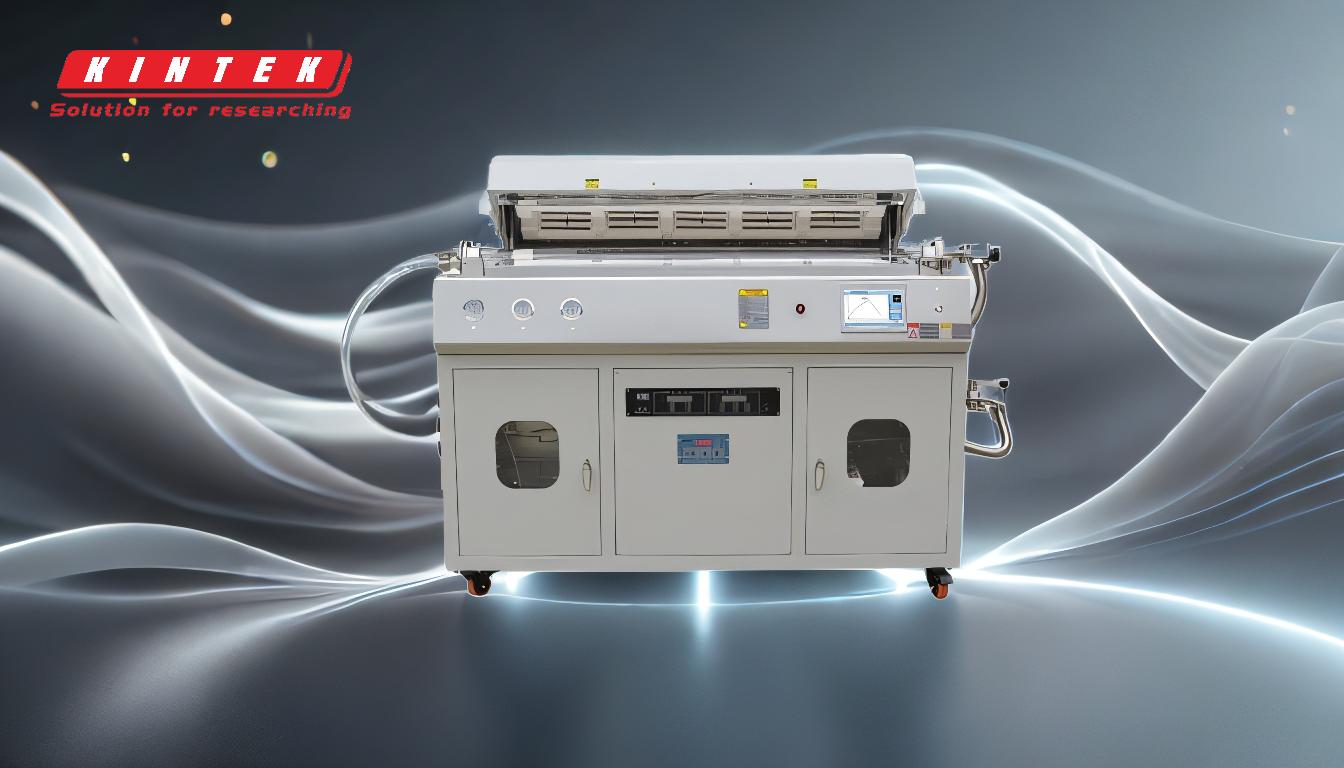
-
Versatility and Wide Range of Applications:
- Chemical vapor deposition can be applied to a variety of materials, including ceramics, metals, and glass. This versatility makes it suitable for numerous industries, from electronics to aerospace.
- The process can be tailored to optimize specific properties such as corrosion resistance, abrasion resistance, or high purity, depending on the application requirements.
-
High Deposition Rate and Uniform Coating:
- CVD offers a high deposition rate, which is beneficial for large-scale production. The uniform coating ensures consistent quality across the entire surface, which is critical for applications requiring precise material properties.
- The non-line-of-sight nature of CVD allows for the coating of complex and intricate surfaces, ensuring even coverage on all parts of the substrate.
-
High Purity and Dense Films:
- The films produced by CVD are of high purity and density, which is essential for applications where material integrity is crucial, such as in semiconductor manufacturing.
- The process allows for the creation of ultra-thin layers, which are necessary for the production of electrical circuits and other high-tech applications.
-
Durability and Resistance to Extreme Conditions:
- Coatings produced by CVD are highly durable and can withstand high-stress environments. This makes them ideal for use in harsh conditions, such as in aerospace or industrial machinery.
- The coatings maintain their properties even when exposed to extreme temperatures or rapid temperature variations, ensuring long-term performance.
-
Precision and Control:
- CVD provides excellent control over the thickness of the deposited layers, resulting in smoother surfaces and better performance characteristics, such as improved electrical and thermal conductivity.
- The process parameters can be adjusted to control the properties of the coating, allowing for customization based on specific application needs.
-
Environmental Benefits:
- Compared to other deposition technologies, CVD has a reduced CO2 footprint, making it a more environmentally friendly option. This is increasingly important as industries seek to reduce their environmental impact.
- The equipment used in CVD is simple to operate and maintain, reducing operational costs and downtime.
-
Economic Advantages:
- CVD is relatively affordable compared to other advanced coating technologies, making it accessible for a wide range of applications.
- The high deposition rate and uniform coating reduce waste and improve efficiency, further enhancing its economic benefits.
In summary, chemical vapor deposition offers a combination of versatility, precision, durability, and environmental benefits, making it a preferred choice for many industrial applications. Its ability to produce high-quality coatings on a wide range of materials, along with its cost-effectiveness and ease of operation, ensures its continued relevance in advanced manufacturing processes.
Summary Table:
Advantage | Description |
---|---|
Versatility | Applicable to ceramics, metals, and glass; customizable for specific properties. |
High Deposition Rate | Ensures uniform coatings and efficient large-scale production. |
High Purity & Dense Films | Produces ultra-thin layers for high-tech applications like electrical circuits. |
Durability | Withstands extreme temperatures and high-stress environments. |
Precision & Control | Offers excellent thickness control and smoother surfaces. |
Environmental Benefits | Reduced CO2 footprint and simple equipment operation. |
Economic Advantages | Affordable, reduces waste, and improves efficiency. |
Unlock the full potential of chemical vapor deposition for your applications—contact our experts today!