Chemical Vapor Deposition (CVD) is a widely used technique for creating high-performance thin solid coatings in various industries. It involves the use of volatile precursors that are injected into a chamber, typically under vacuum, and heated to a reaction temperature. This causes the precursor gas to react or decompose, forming a solid coating that bonds to the material surface. There are several types of CVD methods, each suited for specific applications and materials. Examples of CVD methods include Atmospheric Pressure CVD (APCVD), Low Pressure CVD (LPCVD), Plasma Enhanced CVD (PECVD), and Metal-Organic CVD (MOCVD). These methods differ in the conditions under which they operate, such as pressure, temperature, and the use of plasma or lasers to enhance the deposition process.
Key Points Explained:
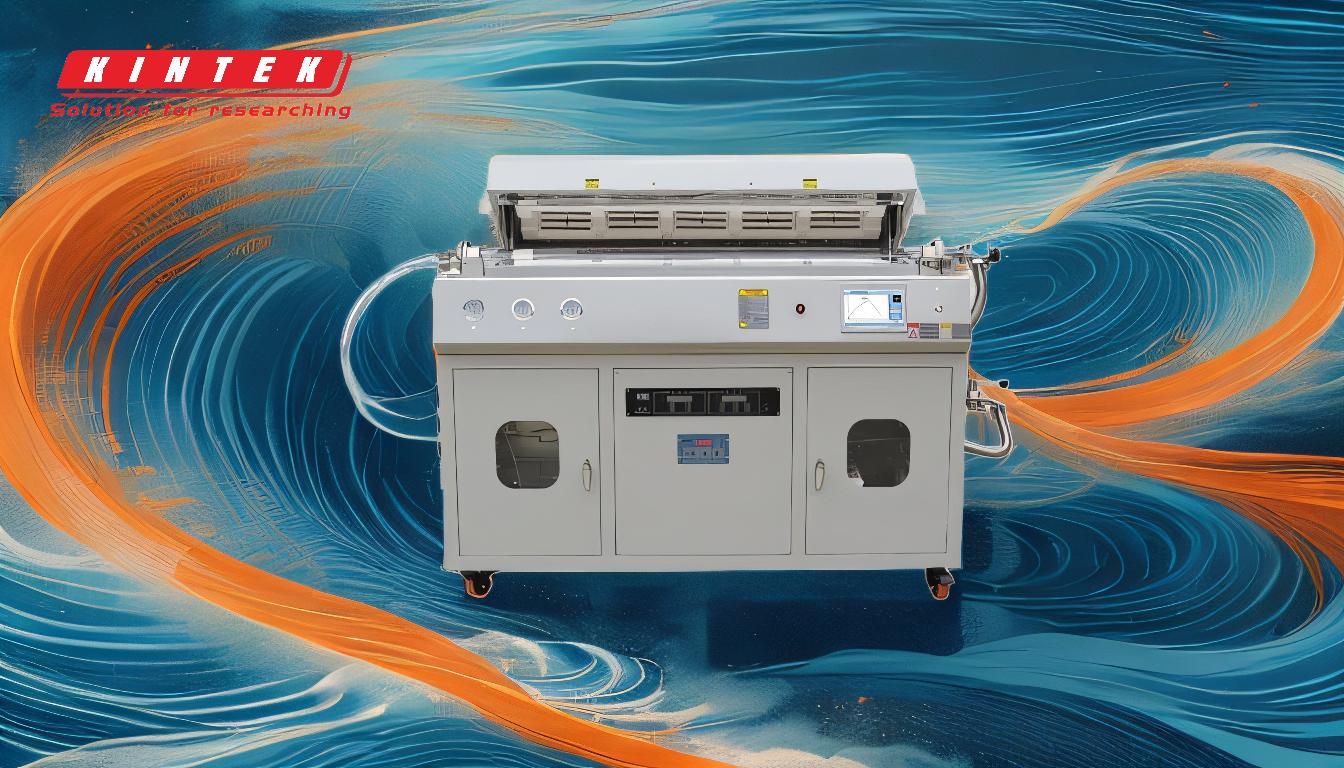
-
Definition of Chemical Vapor Deposition (CVD):
- CVD is a process where volatile precursors are introduced into a chamber, typically under vacuum, and heated to a reaction temperature. The precursor gas reacts or decomposes, forming a solid coating that bonds to the material surface. This method is used to create thin, high-performance coatings for various industrial applications.
-
Types of CVD Methods:
- Atmospheric Pressure CVD (APCVD): This method operates at atmospheric pressure and is often used for depositing oxides and nitrides. It is suitable for large-scale production due to its relatively simple setup.
- Low Pressure CVD (LPCVD): LPCVD operates at reduced pressures, which allows for better control over the deposition process and results in more uniform coatings. It is commonly used in the semiconductor industry.
- Plasma Enhanced CVD (PECVD): PECVD uses plasma to enhance the chemical reactions at lower temperatures, making it suitable for temperature-sensitive substrates. It is widely used in the production of thin films for solar cells and displays.
- Metal-Organic CVD (MOCVD): MOCVD uses metal-organic precursors and is particularly important in the deposition of compound semiconductors, such as gallium nitride (GaN) used in LEDs and laser diodes.
-
Applications of CVD:
- CVD is used in a variety of industries, including electronics, optics, and mechanical engineering. It is particularly important in the semiconductor industry for creating thin films and coatings that are essential for the fabrication of integrated circuits and other electronic components.
-
Advantages of CVD:
- CVD allows for the deposition of high-purity, high-performance coatings with excellent adhesion and uniformity. It can be used to deposit a wide range of materials, including metals, ceramics, and polymers, making it a versatile technique for various applications.
-
Comparison with Physical Vapor Deposition (PVD):
- Unlike CVD, which involves chemical reactions to form the coating, PVD methods such as evaporation and sputter deposition rely on physical processes to deposit material onto a substrate. PVD is often used for decorative coatings and functional coatings in industrial applications, but it generally does not offer the same level of control over the chemical composition of the coating as CVD.
In summary, Chemical Vapor Deposition is a versatile and powerful technique for creating thin, high-performance coatings. The different types of CVD methods, such as APCVD, LPCVD, PECVD, and MOCVD, offer various advantages and are suited for different applications, particularly in the semiconductor and electronics industries. Understanding the specific requirements of each application is key to selecting the appropriate CVD method.
Summary Table:
CVD Method | Key Features | Applications |
---|---|---|
APCVD | Operates at atmospheric pressure, simple setup | Deposition of oxides and nitrides, large-scale production |
LPCVD | Reduced pressure for better control, uniform coatings | Semiconductor industry, thin film fabrication |
PECVD | Uses plasma for lower temperature reactions | Thin films for solar cells, displays, temperature-sensitive substrates |
MOCVD | Uses metal-organic precursors, critical for compound semiconductors | LEDs, laser diodes, advanced semiconductor materials |
Discover the right CVD method for your application—contact our experts today!