Temperature control in a sintering furnace is a critical aspect of the sintering process, ensuring that the material reaches the optimal temperature for diffusion and particle fusion without exceeding the melting point. Various methods and technologies are employed to achieve precise temperature regulation, including PID controllers, thermocouples, and AI-based systems. These controls are designed to maintain uniformity, accuracy, and efficiency throughout the heating, cooling, and sintering phases. Additionally, controlled atmospheres such as nitrogen-hydrogen, vacuum, and others are used to prevent oxidation and enhance the sintering process. Below is a detailed exploration of the key temperature controls used in sintering furnaces.
Key Points Explained:
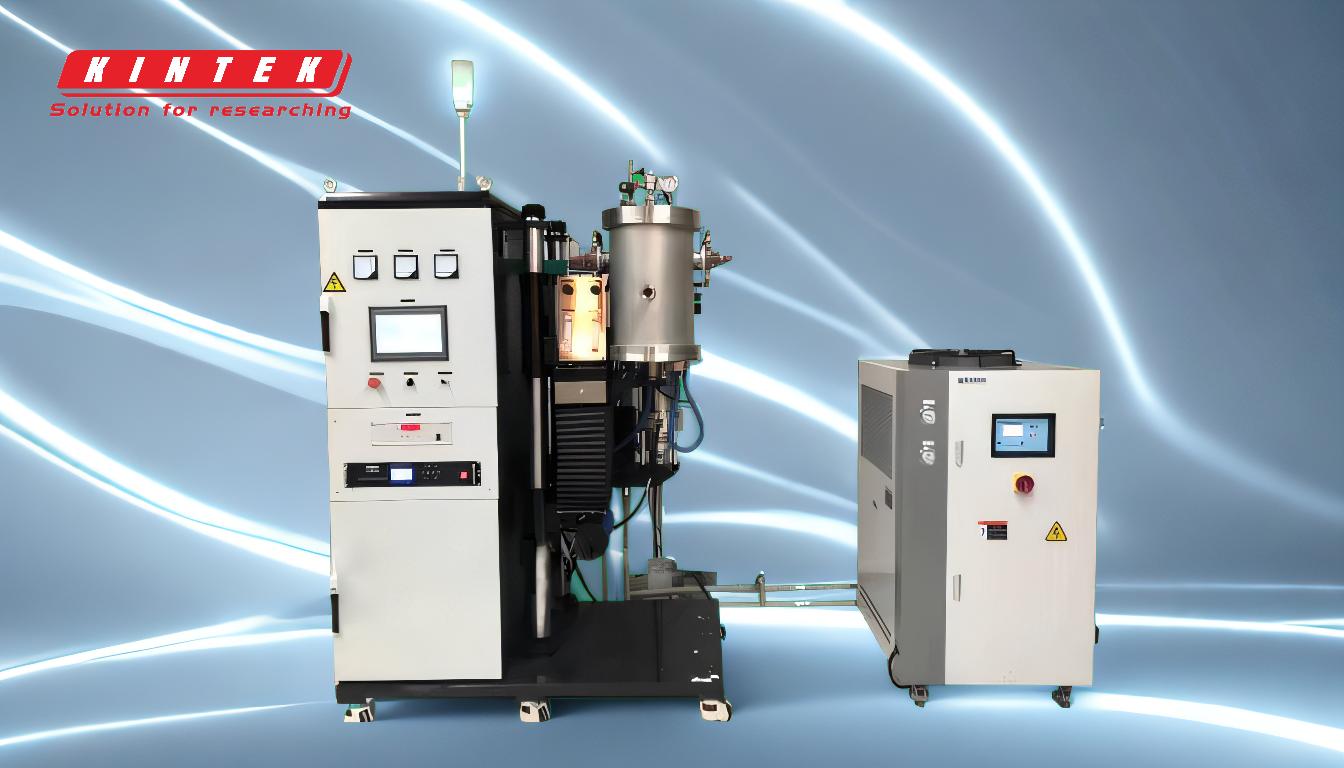
-
PID Control Mode:
- PID (Proportional-Integral-Derivative) controllers are widely used in sintering furnaces to automate the heating and cooling processes. Once the program is set, the system adjusts the temperature automatically without manual intervention.
- This method ensures precise temperature regulation, minimizing deviations and maintaining consistency throughout the sintering process.
-
Temperature Monitoring with Thermocouples:
- Thermocouples are essential for measuring and controlling temperature in sintering furnaces. They are strategically placed at specific locations, such as the hottest and coldest spots identified during temperature uniformity surveys.
- Load thermocouples are also used to simulate part temperature, providing accurate readings that reflect the actual conditions experienced by the material being sintered.
-
Infrared Temperature Control:
- For high-temperature ranges (1000-2000°C), infrared technology is employed for automatic temperature control. This method is particularly effective in ensuring precise regulation at elevated temperatures.
-
AI-Based Controllers:
- Advanced sintering furnaces utilize AI-based controllers to maintain precise temperatures across all zones. These systems enhance efficiency, reduce power consumption, and provide real-time adjustments to optimize the sintering process.
-
Manual Warm-Up and Power Adjustment:
- For temperatures below 200°C, manual warm-up procedures are often used. In a vacuum state, the heating process is initiated by pressing the start button, and the power is adjusted manually to ensure the current does not exceed safe limits (e.g., 1100A).
-
Controlled Atmospheres:
- The use of controlled atmospheres, such as nitrogen-hydrogen, hydrogen, vacuum, dissociated ammonia, and endothermic gas, plays a vital role in temperature control. These atmospheres prevent oxidation and create an environment conducive to effective sintering.
-
System Accuracy Tests:
- Regular system accuracy tests are conducted to ensure that temperature readings are accurate and that the furnace performs as expected. These tests help maintain the reliability and consistency of the sintering process.
-
Role of Temperature in Sintering:
- Temperature is critical in sintering as it must be high enough to facilitate atomic diffusion and particle fusion but remain below the material's melting point to prevent liquefaction. Precise control ensures the desired material properties are achieved.
By integrating these temperature control methods, sintering furnaces can achieve the necessary precision and uniformity required for high-quality sintering processes. Each method contributes to the overall efficiency, accuracy, and reliability of the furnace, making them indispensable in industrial and laboratory settings.
Summary Table:
Temperature Control Method | Key Features |
---|---|
PID Control Mode | Automates heating/cooling, ensures precise regulation, minimizes deviations. |
Thermocouples | Measures temperature at strategic spots, simulates part temperature for accuracy. |
Infrared Control | Effective for high-temperature ranges (1000-2000°C), ensures precise regulation. |
AI-Based Controllers | Enhances efficiency, reduces power consumption, provides real-time adjustments. |
Manual Warm-Up | Used for temperatures below 200°C, ensures safe power limits. |
Controlled Atmospheres | Prevents oxidation, enhances sintering with gases like nitrogen-hydrogen or vacuum. |
System Accuracy Tests | Ensures reliable and consistent furnace performance. |
Optimize your sintering process with advanced temperature controls—contact us today to learn more!