Muffle furnaces are designed to handle high-temperature processes, and the materials used in their construction are critical to their performance. The muffle, or inner chamber, is typically made of ceramic materials like alumina, zirconia, or quartz glass, which can withstand extreme temperatures and resist chemical corrosion. The outer body is usually constructed from thick mild steel or stainless steel, ensuring durability and structural integrity. These materials are chosen for their ability to maintain high thermal efficiency, prevent heat loss, and provide a stable environment for processes like sintering, debinding, and metal injection molding.
Key Points Explained:
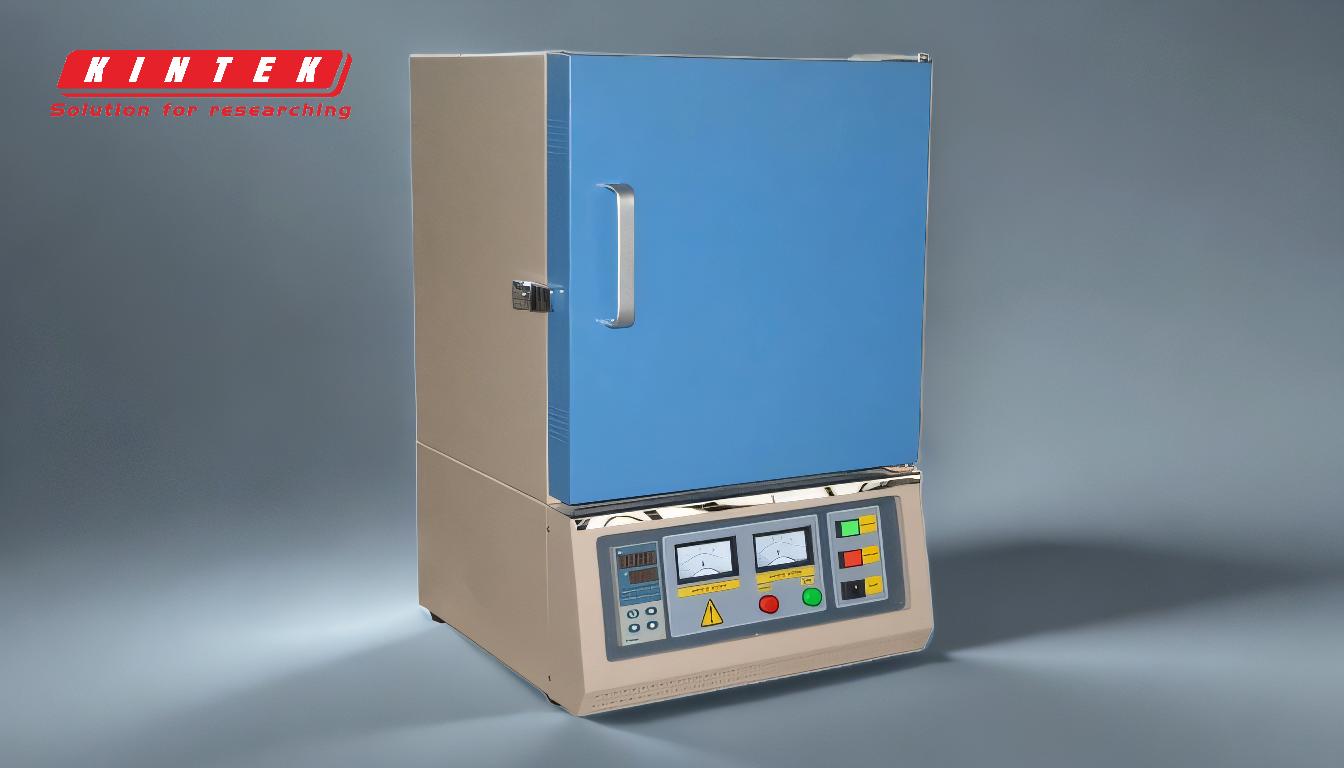
-
Inner Chamber Materials:
-
Ceramic Materials: The inner chamber, or muffle, is primarily made of ceramic materials such as alumina, zirconia, or quartz glass. These materials are chosen for their high-temperature resistance and chemical stability.
- Alumina Ceramic: Commonly used due to its ability to withstand temperatures up to 1800°C and its resistance to chemical corrosion. It is ideal for high-temperature experiments and processes.
- Zirconia Board: Used in furnaces requiring temperatures up to 1600°C. Zirconia offers excellent thermal insulation and mechanical strength.
- Quartz Glass: Provides high transparency, allowing for visual observation of the process. It is suitable for applications requiring moderate temperatures and optical clarity.
-
Ceramic Materials: The inner chamber, or muffle, is primarily made of ceramic materials such as alumina, zirconia, or quartz glass. These materials are chosen for their high-temperature resistance and chemical stability.
-
Outer Body Construction:
- Mild Steel: The outer body of a muffle furnace is typically made of thick mild steel, often powder-coated for durability and corrosion resistance. This material provides structural strength and protects the inner components.
- Stainless Steel (Optional): For applications requiring higher corrosion resistance, such as in pharmaceutical or food industries, stainless steel (SS 304/316) is used. This ensures compliance with Good Manufacturing Practices (GMP).
-
High-Temperature Applications:
- Molybdenum Disilicide: In advanced muffle furnaces, such as the 'Rapid Temp' series, Molybdenum Disilicide is used to achieve temperatures up to 1800°C. This material is essential for sophisticated metallurgical processes like sintering and metal injection molding.
- Thermal Insulation: The furnace is insulated to minimize heat loss, ensuring efficient energy use and maintaining a stable internal temperature. Insulation materials are chosen based on their thermal conductivity and compatibility with the operating temperature range.
-
Durability and Efficiency:
- The combination of high-temperature-resistant ceramics and robust outer materials ensures the furnace's durability and longevity. These materials also contribute to effective heat transfer and uniform temperature distribution within the chamber, which is critical for consistent experimental results.
-
Specialized Applications:
- Alumina Ceramic vs. Quartz Glass: Alumina ceramic is preferred for most high-temperature applications due to its superior thermal and chemical resistance. Quartz glass, on the other hand, is used when visual monitoring of the process is necessary.
- Zirconia and High Alumina Bricks: These materials are used in furnaces designed for extreme temperatures, offering excellent thermal insulation and mechanical stability.
By carefully selecting materials based on their thermal, chemical, and mechanical properties, muffle furnaces are optimized for a wide range of high-temperature applications, ensuring reliability, efficiency, and safety.
Summary Table:
Component | Materials | Key Features |
---|---|---|
Inner Chamber | Alumina, Zirconia, Quartz Glass | High-temperature resistance, chemical stability, and optical clarity (quartz). |
Outer Body | Mild Steel, Stainless Steel | Durability, corrosion resistance, and structural integrity. |
High-Temperature | Molybdenum Disilicide | Enables temperatures up to 1800°C for advanced metallurgical processes. |
Thermal Insulation | Zirconia, High Alumina Bricks | Minimizes heat loss and ensures uniform temperature distribution. |
Looking for a muffle furnace tailored to your needs? Contact our experts today for personalized solutions!